Everything you need to know to make an invisible gelcoat repair, from preparation and filling to topcoat and polishing
How can you repair a scratch or dent to the hull yourself, and when is it time to call in the gelcoat repair experts? Ali Wood looks at the options…
Chances are, if you own a GRP boat at some point you’re going to have a ding, resulting in scuffs, scrapes and dents. Or in the case of Maximus, our PBO Project Boat, you might inflict gouges yourself with some over-eager antifoul paint scraping!
Don’t panic, the beauty of composite hulls is they’re easy to repair – although getting a smooth finish and the correct colour does require precision. Before starting a gelcoat repair it’s worth understanding how GRP boats are made, and why gelcoat is so important.
Hull construction
Composite hulls are made from two or more materials with different chemical properties which, when combined, create new characteristics. This may be resin combined with glass fibres (GRP) but there are other types too, such as carbon fibre and ferrocement, or wood combined with epoxy resin.
Sandwich construction, which you find in Sadlers and Etap yachts, is also considered composite. Here you might have a balsa or foam core sandwiched between skins of GRP. These hulls are well insulated and unsinkable as their foam core provides buoyancy.
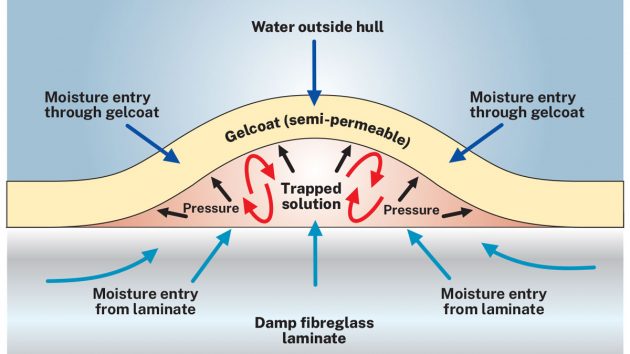
How osmosis occurs
Osmosis
GRP layers are known collectively as a ‘laminate’, and during production small voids, air pockets and micro cracks will form within the resin and at the interface of the resin and glass fibres.
All laminates will allow water molecules to pass through, but where the water gets trapped it can break-down components in the laminate such as acids and alcohols. It’s these tiny concentrated pockets of solution where osmosis (hull blisters) begin.
Gelcoat
Most GRP boats are finished with a thin (0.25 – 1mm) outer skin of gelcoat, which is made of polyester resin. As this dries, it hardens, creating a shell-like layer over the fibreglass, protecting the hull from water, UV damage, chemicals and scratches.
If you maintain your boat regularly, gelcoat can protect the hull for a decade or two, but it does go chalky over time, which is when you’ll want to polish your gelcoat.
Moisture in the hull
Our Maxi 84 Project Boat is made of woven roving and chopped strand mat (CSM) and coated with an off-white gelcoat backed with polyester resin.
When we invited marine surveyor Ben-Sutcliffe Davies to survey Maximus, he brought along his moisture meter.
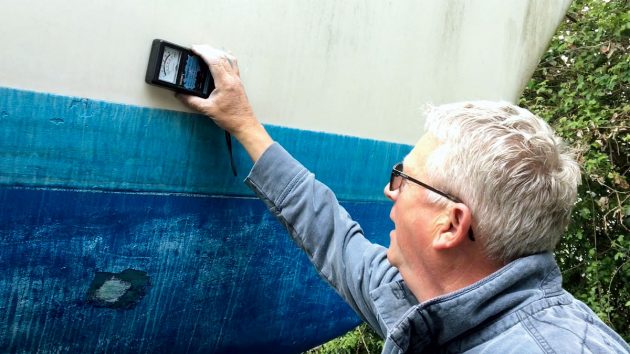
Ben measures moisture levels in Maximus’s hull
Ben explained that when laminate gets saturated it loses about 25% of its strength and that’s when you start to see high moisture readings.
Fortunately, Maximus scored between 15 to 30, so was considered dry.
Anything above this would suggest moisture-related defects not yet detectable, and by the time you get to 46-60 you should expect to see signs of moisture damage.
Over 61 and there’s likely laminate damage as well as osmotic blistering.
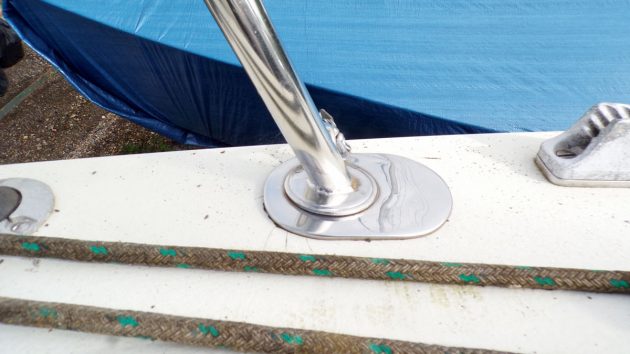
Stress cracks in gelcoat can form around deck fittings – although repairs aren’t deemed necessary here
Gelcoat checks
When inspecting your hull check for chips in the gelcoat that may need filling, and surface scratches if noticeable.
Cracks in the gelcoat might indicate damage beneath or stress caused by a deck fitting, for example.
Blisters on the hull, as noted already, are a sign of osmosis. If you’ve owned the boat for a few years, check if these are getting worse.
If there are just a few, you may be able to deal with them by grinding them out, leaving the laminate to dry, and then filling it.
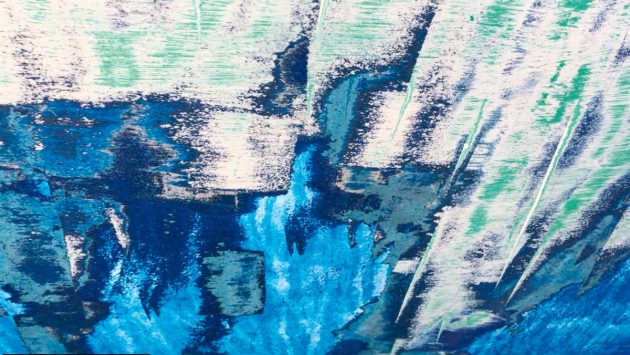
These hull gouges will be easily fixed with epoxy filler and no colour-matching is required as we’ll be antifouling over the top
When Ben inspected Maximus he suggested the topsides were in need of a compound and polish.
He also pointed to a gelcoat repair that didn’t match the original colour and an area that had been sanded too far back.
“They’ve actually started going through to the laminate below,” he advised. “You’ve got to be very careful about doing much more here in the way of T-cutting.”
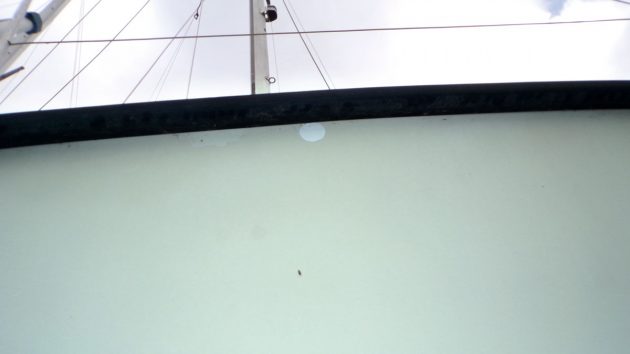
This gelcoat repair in Maximus wasn’t colour-matched
Repairing gelcoat
A gelcoat repair isn’t always critical right away. If you get a ding, you can usually wait until the boat’s next in the yard. However, if the damage has gone through the gelcoat, exposing the laminate, a temporary repair with gelcoat filler should prevent water ingress.
But what happens if you ignore gelcoat damage? Aaron Logan of Small Boat Services warns that over time water will wick into the laminate and the more moisture there is in the hull the bigger the repair will be.
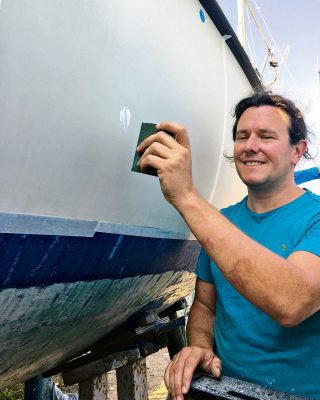
Fixing a small dent in Maximus’s gelcoat. Sadly we didn’t get the colour-matching quite right!
“Your boat’s not going to sink but that £400 repair will be £500 the following year or worse,” he warns. He adds that it’s impossible to cost a gelcoat repair without seeing the damage.
The unit price can be quite high even for a small repair, and ironically you may get ‘more for your money’ repairing a bigger area.
Price varies too according to the colour of the gelcoat. A professional repair is a full day’s work or longer. Once the boat’s laid up, if you decide to do a gelcoat repair yourself the temperature needs to be over 16°C otherwise the gelcoat won’t harden.
This isn’t usually compatible with a British winter, but you may be OK if you can find boat storage under cover.
Epoxy or resin?
There are two main types of resin for repairs: epoxy and polyester. Each has different properties: polyester, for example, is combined with a catalyst in order to bond, whereas epoxy is combined with a hardener.
It’s essential the catalyst or hardener is mixed thoroughly to ensure an even cure. Polyester is much cheaper but epoxy is stronger and resistant to osmosis. For longer-lasting repairs, especially below the waterline, epoxy is the best option.
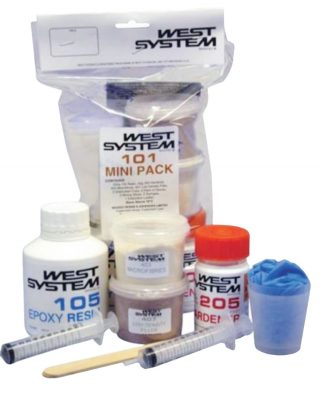
West System repair kit
Gelcoat repair kits
PBO expert Stu Davies keeps both types of resin on board. For minor dents and scratches, he uses Osculati White Gelcoat (polyester-based). It works like a regular filler. “Just paste it on then rub with 800-grit, going up to 1200, 1800 and 2500, then finish with a polish,” he says.
For larger repairs on his Beneteau, Stu uses epoxy-based West System Fibreglass Repair kit. He warns that for the perfect colour-match, though, he’d still pay a professional to do the job.
“No boat is ever just generic white,” he says. “Check to see if there’s a colour code given on a data plate in the cockpit then tell that to the repairer.” If you decide to do a repair yourself the most economical way would be to order a kit with small quantities of everything you need.
East Coast Fibreglass Supplies sells a white or black gelcoat repair kit which includes polyester isophthalic gelcoat, along with mixing cups, sticks, wet and dry paper, protective equipment, acetone, UV wax and polishing compound. For non-white hulls, you need to select the clear resin option and add pigment. A full list of colours is on their website.
West System, on the other hand, sells a fibreglass repair kit using epoxy resin. This includes plain weave and biaxial glass so you can cover a range of repairs from dinks to bigger holes.
Note: We may earn a commission when you buy through links on our site, at no extra cost to you. This doesn’t affect our editorial independence.
Step-by-step gelcoat repair
Gelcoat repair step 1: Preparation and matching the colour
The first job in any gelcoat repair is to check the damage closely, both inside and out. Sometimes a hard knock can cause delamination within the hull, in which case a more serious repair will need to be carried out first. In this example damage to the hull at the stem is fairly typical of a modest dockside shunt, and proved to be cosmetic rather than structural.
If the edges hadn’t been sharp we’d have first had to remove any loose material with a Skarsten scraper. As it is, in this case we can simply give the damage and the surrounding area a good wipe over with acetone to remove any wax or dirt.
Before any repair is made you need to know the true colour of the hull – there’s no point matching a repair to a faded pigment which will change when it’s polished. Ideally, then, you need to polish the hull back to as close to its original colour as possible. Chalking and superficial scratches had already been polished out of our example boat’s hull, so we have a true colour to work to. If it had been an untreated hull we’d have needed to prepare a small area first.
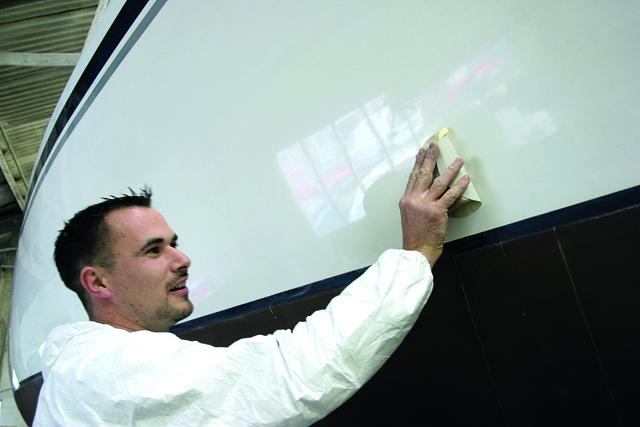
1. First choose a part of the hull identical in colour to the damaged area. This will become the mixing palette on which to colour-match the gel coat. Go over the area with 1,000-grit abrasive paper to remove scratches and chalking.
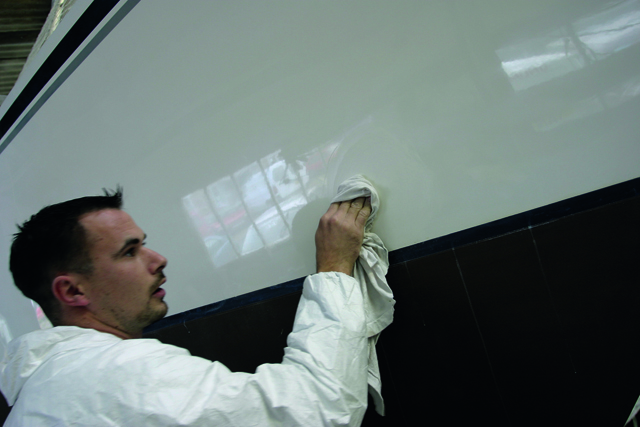
2. Using a rubbing compound, the area is then flatted to restore the original colour of the gel coat, leaving it with a slightly matt finish.
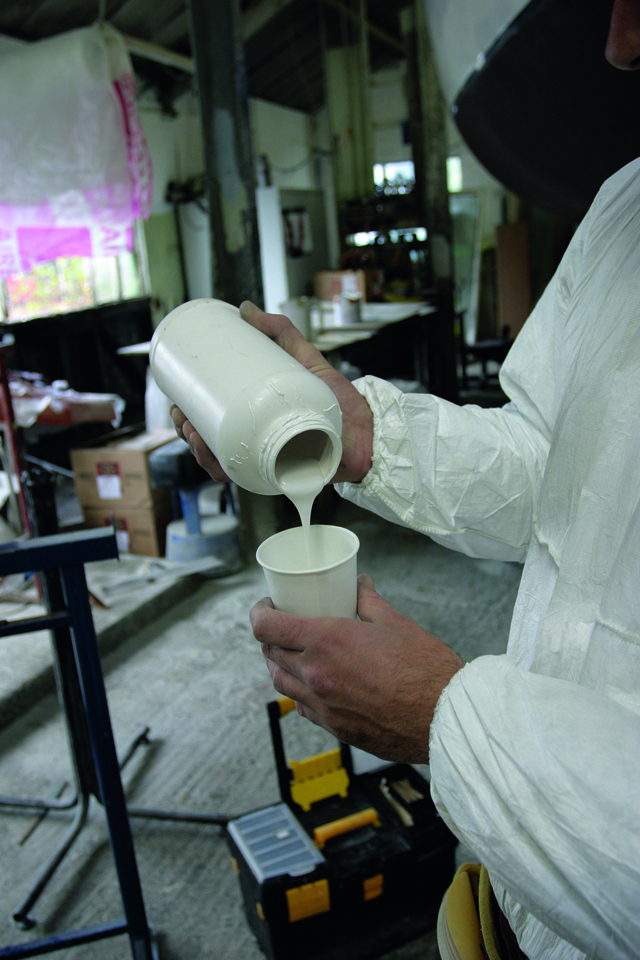
3.Enough plain white pigment is decanted to complete the entire repair. A small amount will be placed onto the prepared palette area.
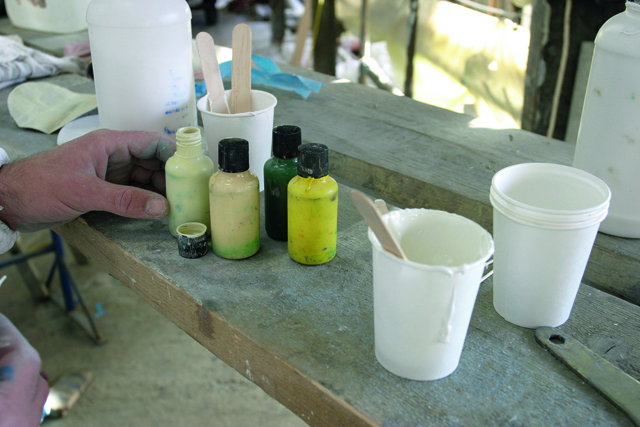
4.The hull may appear white, but look closely to see what colour tints might be necessary for a perfect match – in this case a hint of green, with a trace of yellow and a touch of cream.
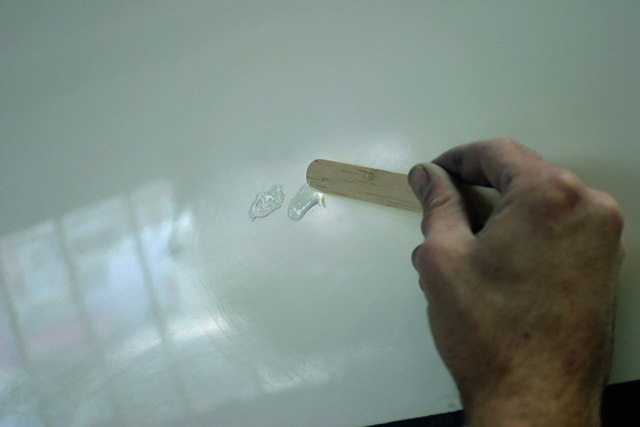
5. Using a mixing stick, place a few dabs of uncatalysed white gel coat onto the hull. These will become your testers (because they haven’t been activated with catalyst, they can later be wiped off with acetone)
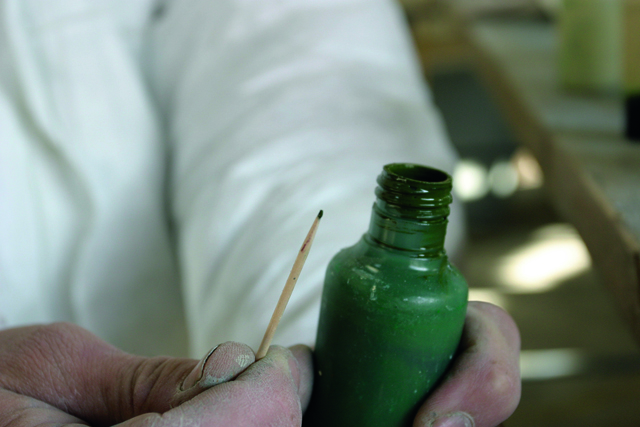
6. Now for the tricky bit. A tiny dab of the dominant colour is placed on the end of a cocktail stick…
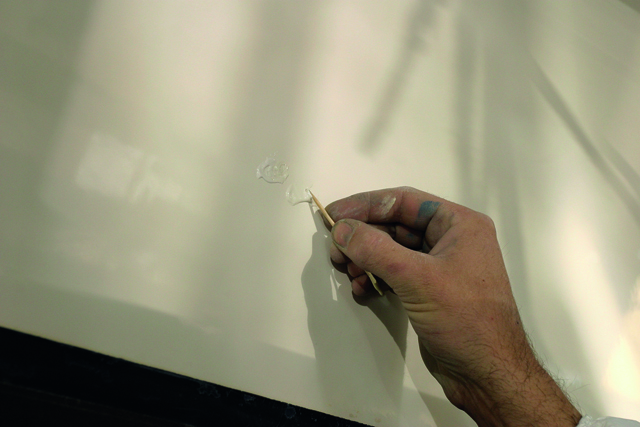
7. … and is then mixed into the tester. Care is needed to ensure all the pigment is evenly distributed, which requires some dexterity.
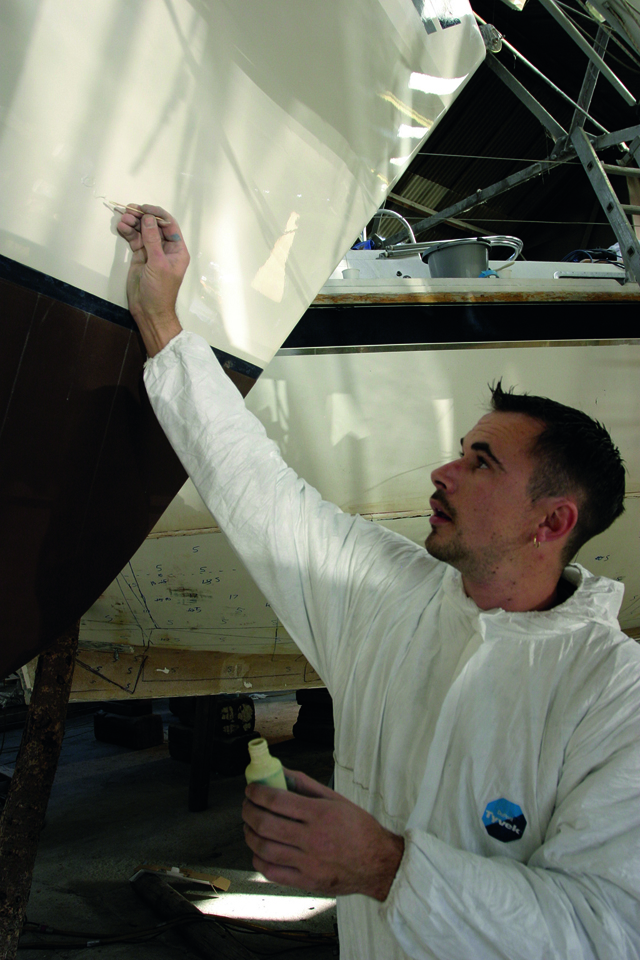
8. When you are confident you have the green element of the match, you can then switch to the next colour, cream, and repeat the process. If the match goes wrong, start again.
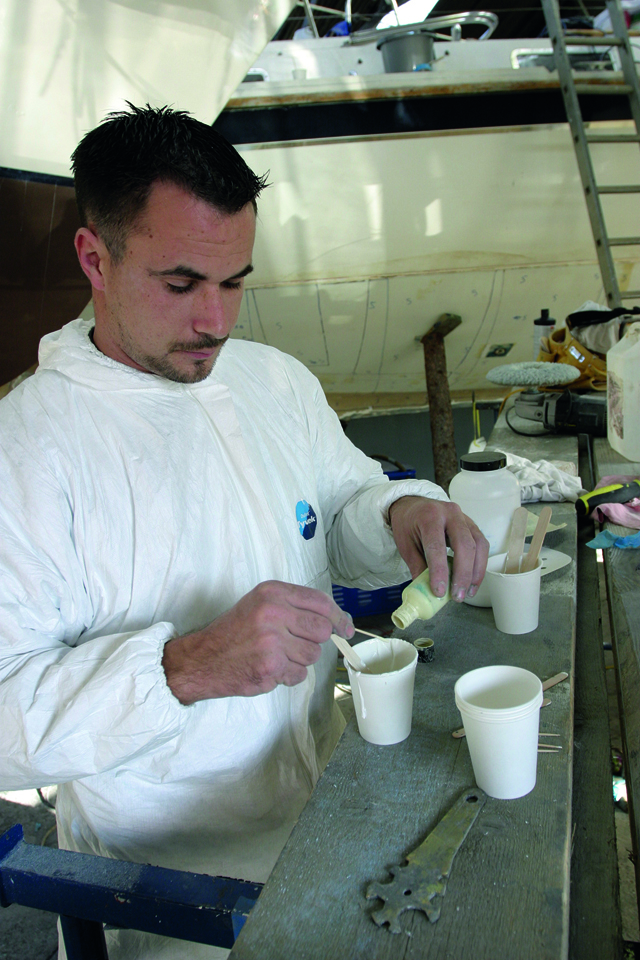
9.Throughout the process, keep a mental note of how much of each pigment you have used for the match. When you’re happy with the result, use this experience to multiply the ratios to make a full batch of gel coat, enough to complete the whole repair.
Gelcoat repair step 2: Filling the hole
Once mixed, the colour-matched batch is then split, with some being kept back for the finishing coat. The majority will be used for the initial fill, and here a filler powder is added to bulk out the gel coat so it stays put, making sure the colour remains the same.
As a check, it can be dabbed back onto the hull at any stage. It’s important that the entire repair is colour-matched and not just the surface layer. That way if the hull is abraded back any time in the future, the repair will remain invisible.
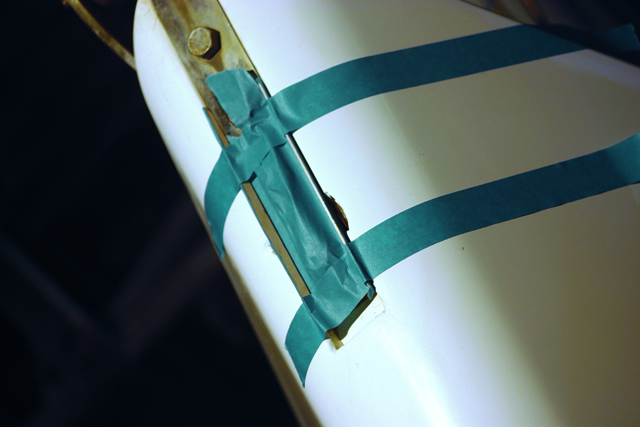
1. The repair site on the stem is masked off to protect the stainless steel strap. Note strips of cardboard used to make small cofferdams.
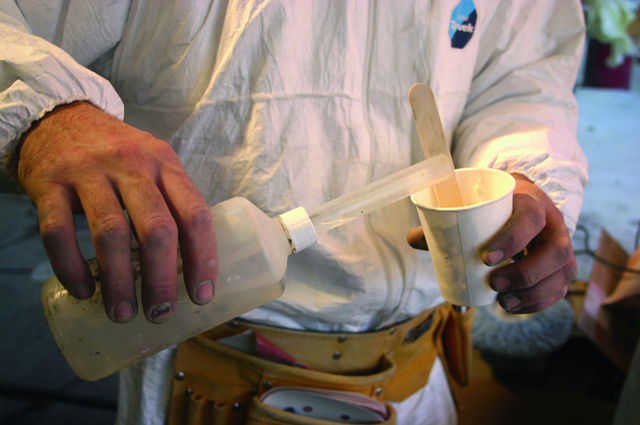
2. The thickened mix then receives some catalyst at a ratio of 1%. It’s important not to add any more than this to hasten the cure. The heat generated by a fast cure can actually alter the colours, making them darker.
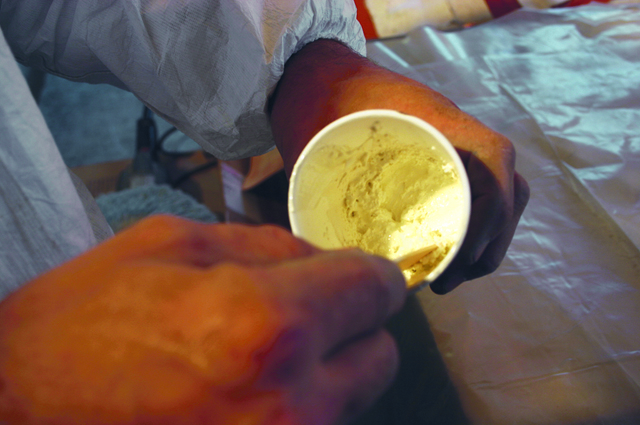
3. The colour-matched filler is then thoroughly stirred together to make sure all the catalyst is mixed in…
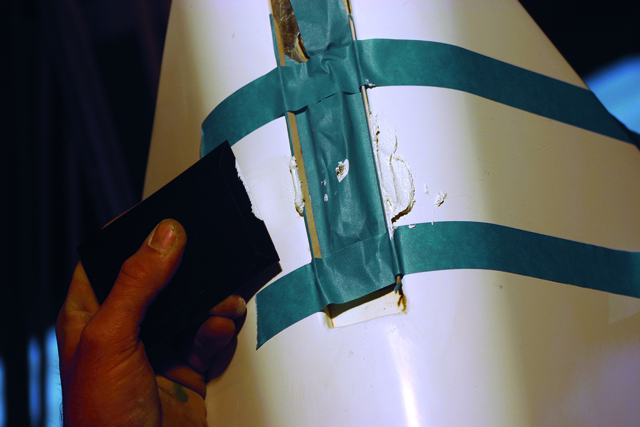
4. …before being applied firmly to the holes with a flat scraper. The excess is then taken off with the scraper’s leading edge until the filler is standing just slightly proud.
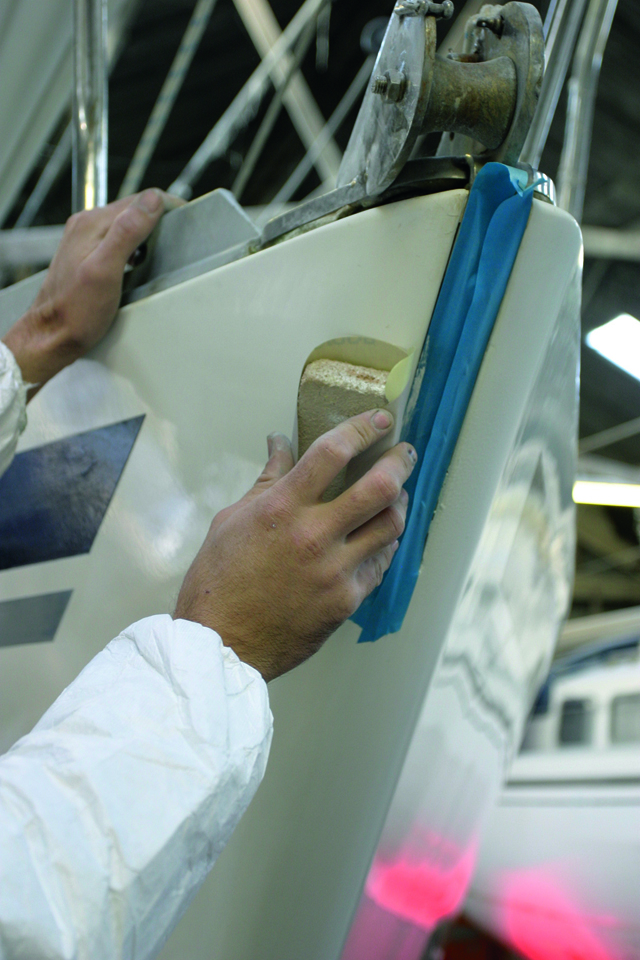
5. Once fully cured, the area is then sanded back flat with 240-grit paper on a sanding block. Using a block is best as pressure from fingertips and sandpaper alone can sometimes produce an uneven finish.
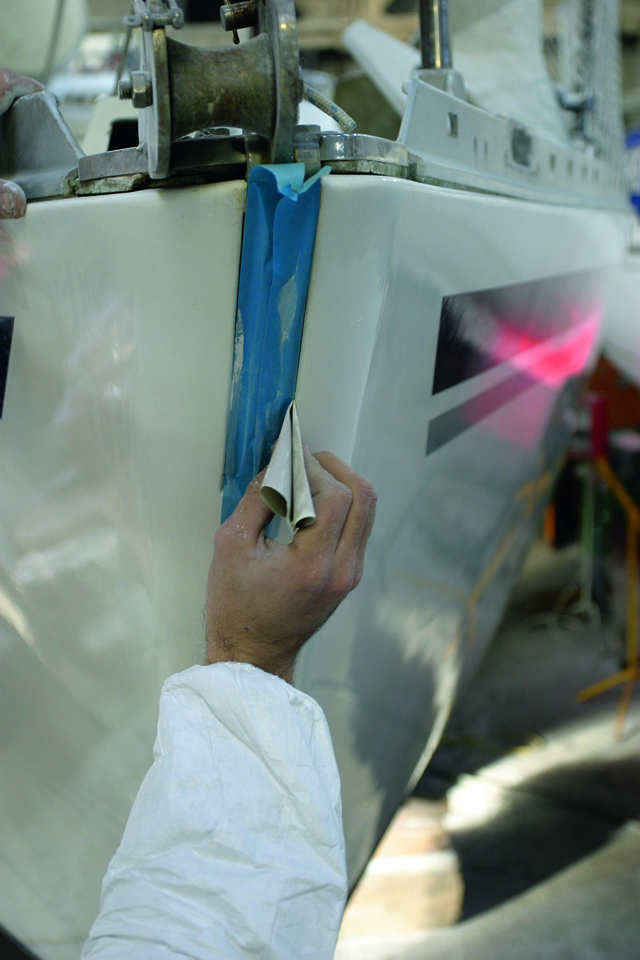
6. With the area flatted, it can then be tidied as shown here, making the edge of the repair smooth. The masking tape stays on the stainless strap to protect it from scratches.
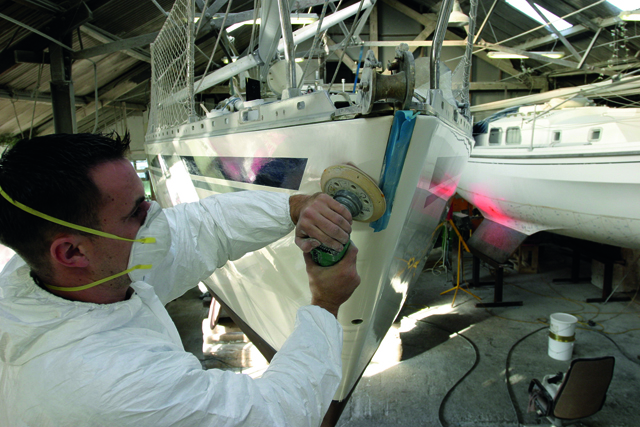
7. The next job is to go over the repair with a random-orbit sander fitted with a 400-grit disc. This will match the final blend of the filler to the rest of the hull, and give a super-smooth surface for the last stages.
Gelcoat repair step 3: Applying the topcoat
The critical stage is to apply the topcoat. This is our last batch of colour-matched gel coat, and it is unthickened. The addition of a little wax-in-styrene (2%) before the catalyst is added will slightly improve the flow, and make the curing easier.
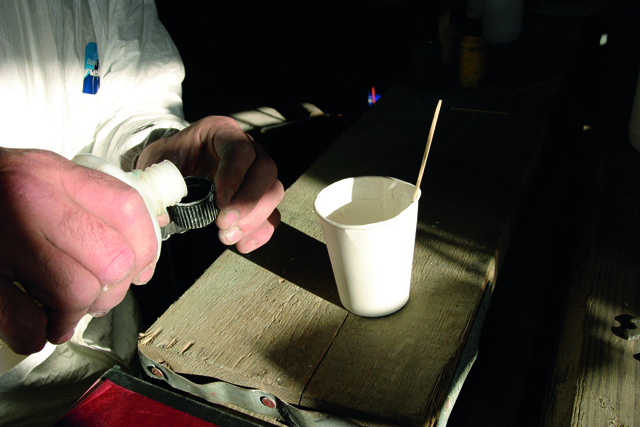
1. A 2% addition of wax-in-styrene is mixed into the final batch of gel coat. It is stirred well, and then the catalyst is added.
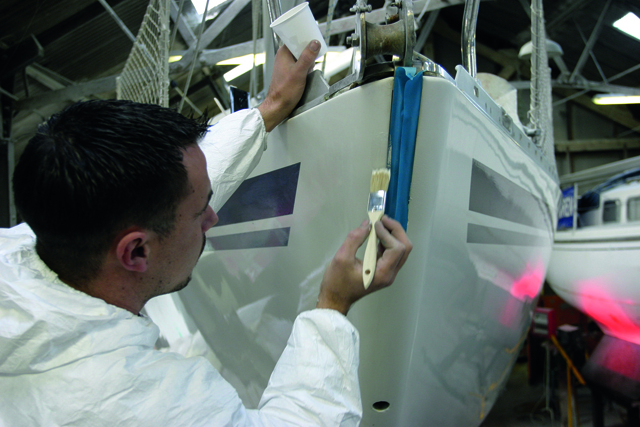
2. Now gently paint your activated gel coat over the whole repair, avoiding brush marks and making sure you get a fairly wide coverage.
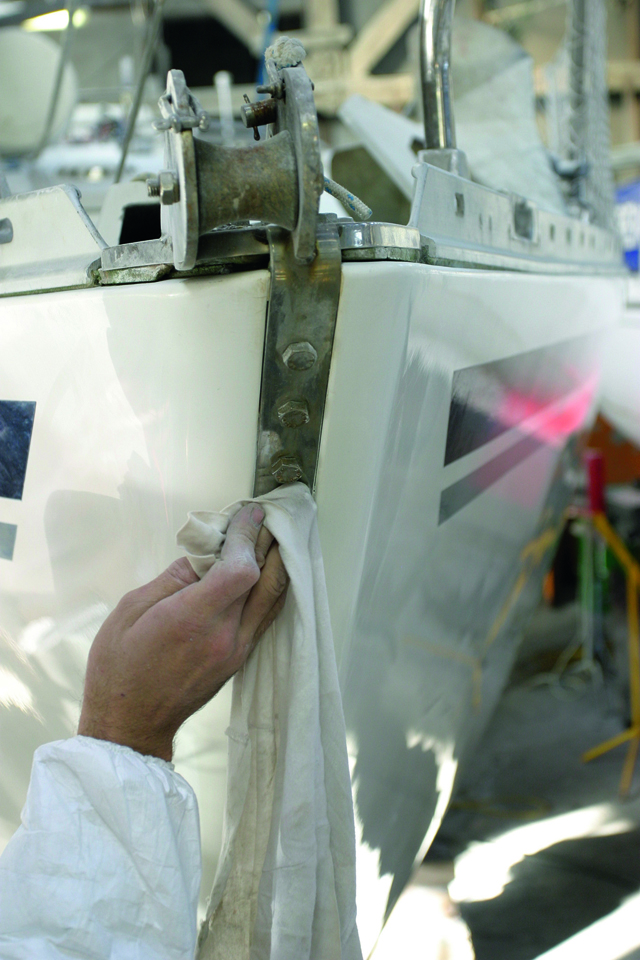
3. Once the topcoat has dried, usually in about an hour, the masking tape can be removed. The surface is given a wipe down with acetone to remove the wax, and also any splashes that may have got under the tape. The metal is colder than the hull, so gel coat splashes on it might still be quite soft and easy to remove.
Gelcoat repair step 4: Final polishing
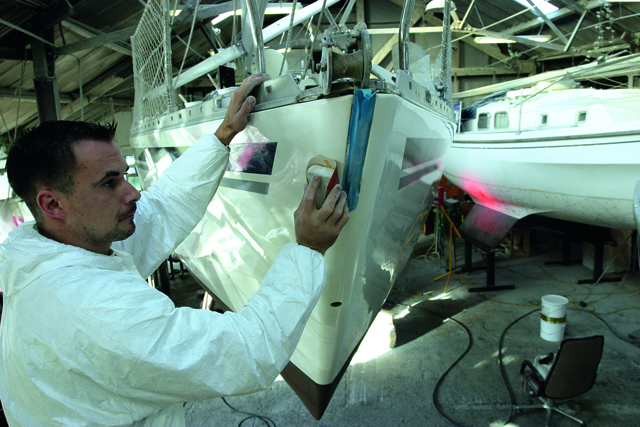
1. Using a sanding block again, a 400-grit paper gently flattens off the topcoat, not forgetting details such as the edges around the strap.
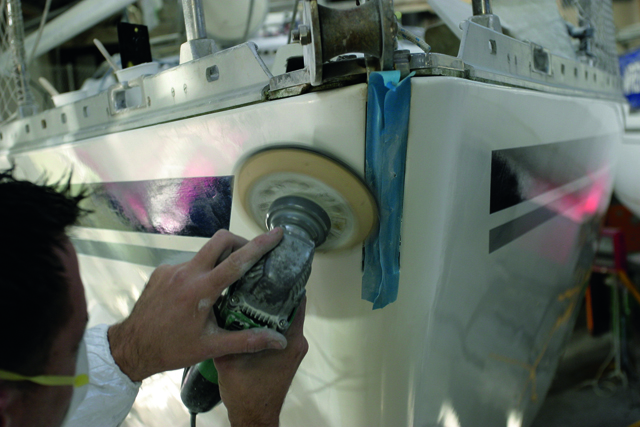
2. Switching to a finer 800-grit paper, the repair is now machine-sanded, paying attention to the stippled edges. Everything is done in short bursts, and with great care.
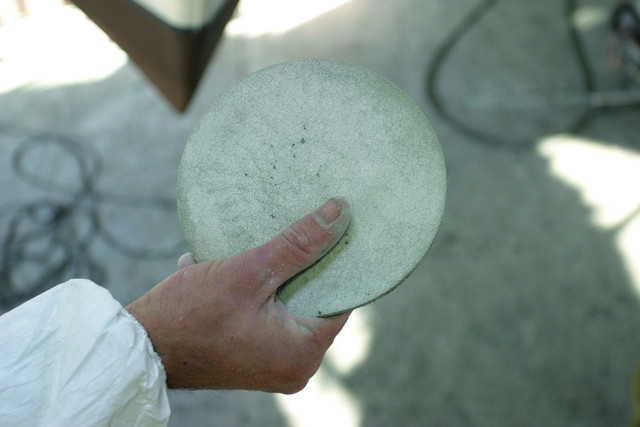
3. The final stage is with a 3,000-grit abrasive disc. This can bring out a perfect shine by itself – but one final stage is yet to come.
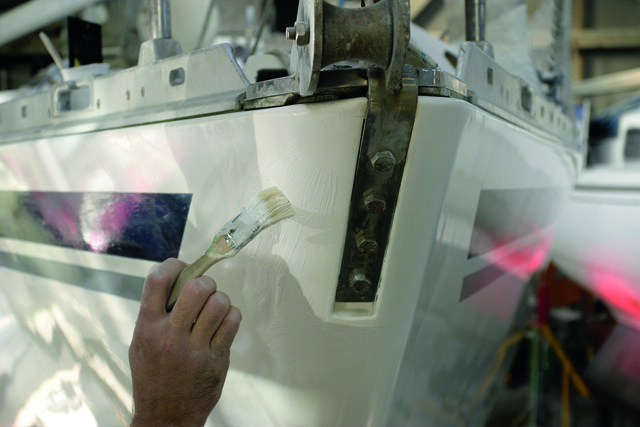
4. Polishing compound is now applied with a brush. Adding a little solvent to the mix makes the polishing compound smoother and workable for longer.
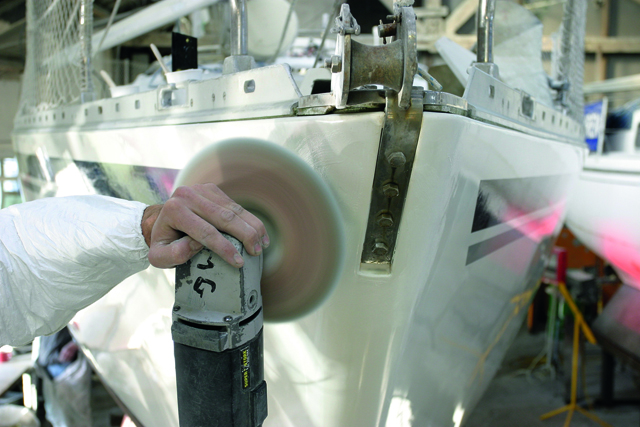
5. Using a lambswool buffing head on a slow- running rotary polisher, the repair is given a final polish to really bring out the shine.
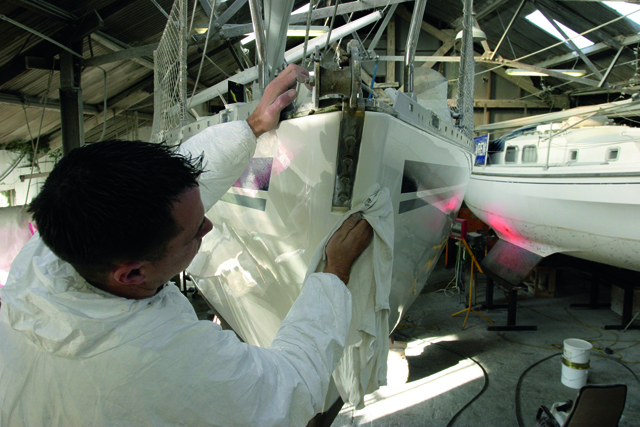
6. Job done. A layer of UV protective wax can now be applied to protect the hull – and its invisible repair – from UV fading.
Gelcoat repair: Top tips
- The catalysed gel coat will set in about 30 minutes, but the cure could be accelerated by heat from the hand. If you don’t want this to happen, hold the mixing pot by the rim.
- Once the wax and catalyst have been thoroughly mixed, tap the container a few times on the worktop and let it stand for a few seconds. This allows any air bubbles to make their way to the surface. Bubbles trapped during application will leave pinprick voids in the finish.
- Use the brush to stipple around the edges of the topcoat. This will give you a seamless merging of the gel coat with the surrounding hull when it has been sanded back.
Coloured hulls
This repair has been to a ‘white’ hull, but exactly the same principles apply to pigmented hulls. The only major difference in that case is that you would use a clear gel coat to carry the deep colours required, rather than a white one. To bulk out a clear coat, a colloidal silica would be used instead of the filler powder we used for this job.
Thanks to Aaron Logan of Small Boat Services, and to Hayling Yacht Company for the loan of their shed.
Alternatively you can read how to do a simpler colour match using a clear kit you can buy from a chandlery below
Gelcoat repair colour matching – the quick way
A basic colour match may not be perfect – but in most cases it’ll do the job and is much…