It’s packable, rowable, towable and sailable! Richard Drabble explains how he built a nesting Eastport Pram dinghy as a wedding gift for his daughter
In the days before inflatable dinghies it was common to have a hard dinghy, to be left on the mooring or hoisted onto the foredeck of your yacht, or atop the main deck forward of the cockpit.
Instantly launchable, it would be hard-wearing, characterful and unlikely to let you down.
There were many designs. A particularly attractive one was the 7ft 9in Humble Bee, which could be built in marine ply planking for lightness and stiffness and indeed can still be built using available plans.
While living in Canada I founded a boatbuilding academy as my night job, where we used plans for various small boats sourced within Canada and the USA.
Another small boat which caught my eye was the Eastport Pram. This 7ft 9in dinghy had pretty yet practical lines as a rowing yacht tender, and could also be sailed with a standing lug rig or motored with an electric or petrol outboard up to 2hp. Such a design could be brought to a conventional sharp bow.
However, this would reduce its stability and buoyancy, hence less load carrying for the given length, so the cut-off or pram bow shape is both practical and rather a quirky, attractive feature.
The designs are owned by Chesapeake Light Craft (CLC) in Annapolis, who can also supply a kit of building materials. You can also get them from Fyne Boat Kits in Kendal here in the UK.
I noticed there was a nesting dinghy version, which entails building the boat and then cutting it into two pieces so that one part cleverly stows away within the other. I have worked in Russia too and I thought they had this patent with their nesting dolls, but apparently it also works well with dinghies!
Now back in the UK, I decided to build an Eastport Nesting Pram dinghy in my winter workshop, aka the dining room.
My long-suffering wife was very accommodating, having to live in a dusty house all winter and seat guests at the kitchen table. It might have had something to do with it being a wedding present for our daughter Jocelyn and husband Henry, both sailors who live in Cowes on the Isle of Wight.
Construction
The advent of epoxy resins has revolutionised wooden boatbuilding, and so this boat is built as a composite in marine plywood, glassfibre and epoxy. This makes it possible to build a lighter yet stronger, stiffer and more durable boat.
It’s stitched together with wire in lapstrake marine plywood planks (6mm Okoume) around a temporary frame. It’s then epoxy bonded along the seams, strengthened and stiffened in the sole (floor) with glassfibre and epoxy either side of the plywood core.
The sandwich construction is then sealed with clear epoxy before varnishing and painting.
The epoxy bonded lapstrake planking is an advantageous hybrid between clinker and carvel, being both strong and stiff.
The bow, transom and internal connecting bulkheads are epoxy laminated in 9mm marine ply, so 18mm total thickness for strength.
A lot of wire stitching is involved to assemble the boat on a flat surface, usually on carefully levelled building trestles.
A daggerboard slot and mast foot is built-in, if your dinghy is to be sailed.
After epoxy bonding of the seams, the stitches are removed and work proceeds with fitting the mahogany gunwales and the glassfibre-epoxy strengthening of the sole.
The seat supports are then built in. You will have pre-assembled the two-piece internal connecting bulkheads with a sacrificial cardboard spacer in between, so that you can eventually cut the boat into two parts with a carefully chosen saw, steady nerves and a Mk 1 eyeball.
There are six machine bolts with winged nuts used to connect the two parts of the boat together, sandwiched between a neoprene waterproof gasket.
Folding Eastport Pram specifications
- Length: 2.36m (7ft 9in), or 1.45m (4ft 9in) when nested
- Beam: 1.26m (4ft 0in)
- Rowing draft: 13cm (5in)
- Sailing draft: 64cm (25in)
- Weight: 30kg (66lb)
- Load carrying: up to 3 persons
- Length of oars: 2 m (6ft 6 inches)
- Sail area: 3.9m2 (42ft2)
- Outboard: 2hp (electric or petrol)
Cutting a boat in half that you’ve just built is not easy on the nerves. The cut line was first proved with a row of 1mm drill holes (later filled and faired), then connected by a pencil line. Using a fine Japanese saw, a steady hand and a good Mk 1 eyeball, the cut was carefully executed. A stiff whisky was then required to settle the nerves, as the last act of that day!
Don’t underestimate the amount of work to round over edges, using a router, and sanding ahead of painting. I spent several days outside on mild days so as to minimise creating dust inside. This began with machine sanding and progressed to hand sanding for the fine finish, ready for clear epoxy coating. A dust mask, eye and ear protection is compulsory!
Thereafter, the entire boat, seats, foils and spars have to be prepared for painting by light sanding the epoxy coating with 240-grade (ready for varnish) and 120-grade (ready for paint primer) on the outside of the hull. I normally choose to use good quality 3M wet and dry paper, for wet sanding, as this is more effective, more user friendly and in addition it removes the water soluble surface amines produced by epoxy during the curing process.
Choosing the paint
I researched the paint options thoroughly and settled on Epifanes, who are technically most helpful and whose prices are competitive. I chose to use their two-component polyurethane coatings, both for the varnish and the hull paint. These are easy to apply with a roller and tip-off using a fine brush or foam brush. They also allow one coat each day without sanding, applied sequentially each day for four or five days (so four or five coats), so that there is a chemical bond between the coats. The two-component varnishes and paints deliver a harder, more durable finish, which should greatly exceed the performance of single component paints.
It’s worth noting that the varnish scheme was two coats of full gloss, followed by two coats of satin finish varnish. This is because the full gloss has a better UV resistance than satin varnish, so as to protect the underlying epoxy clearcoat, whilst the satin finish gives a lovely non-dazzle finish where you can actually see the wood grain. It’s also more forgiving of minor imperfections.
Lastly, a non-slip coat of satin finish varnish was applied over the sole tread areas using Epifanes micro-beads mixed into the varnish. This was then over-coated once to finish the job. With such two-component paints it is essential to ventilate your workroom thoroughly and wear a passive respirator mask to protect yourself against breathing paint solvents.
Extras and modifications
I estimate that the total build time for this tender, including painting, was about 180 hours, but I was not in a hurry and this was spread out over five winter months.
I did come across some aspects of the design, build and materials that I took issue with, and have fed these thoughts back to the supplier. For example, the bulkhead design required ugly, oversized epoxy fillets between the bulkheads and the lapstrake planking, and I discarded the gasket material in favour of something more suitable.
Installing both a gunwale (outwale) and an inwale, makes handling of the boat easier, and I also strengthened the mast foot, adding an oak mast retention peg.
A high quality Wichard foldable D-ring was through-bolted low down on the bow bulkhead as an effective towing point from a yacht, directional stability being aided by the hull skeg, which also provides great stability for rowing and sailing.
I also built a lightweight, compact launching trolley, which cleverly locks onto the hull architecture so that it doesn’t slip and slide as you roll over bumps on the beach.
1. DIY launch trolley
I designed my own lightweight, compact launching trolley, which locks onto the hull architecture so that it doesn’t slip and slide when rolling across the beach. It’s made of 18mm marine ply with corner strengthening, epoxy glued then epoxy clear coated before painting.
Holes were added for cargo straps. It’s well balanced with both the tender assembled and with it nested. It uses rust-free solid tyre wheels and stainless steel shouldered bolts as axles. The padding? Best quality Axminster!2. Centre mainsheet mounting
This was my own design. It involves 2x18mm laminated cheeks – so 36mm total thickness, which is strong for heavy weather gybing! This was epoxy glued onto the daggerboard slot. The roller bearing block was mounted by multiple threading 3mm cord through a short length of 15mm radiator hose!
3. Waterproof gasket
The forward joint bulkhead carries a glued-on waterproof gasket of 8mm neoprene – actually an Aldi exercise mat. This squeezes down into a gap of 4mm once the six wing nuts are tightened, making a waterproof connection and a nice firm join between the two halves of the tender. The final assembled gap between the forward and aft halves along the hull planking, is just 1mm – the exact thickness of the Japanese saw used to make the cut.
The boat is best transported on a yacht while nested, strapped down ahead of the mast. Or by car with the two halves assembled, upside down on roof bars, which works well on most medium to large sized cars. This prevents the separate parts from jostling about on bumpy roads and chafing all that beautiful paintwork. Extra length roof bars are required to accommodate the 4ft beam, but these are reasonably priced and will fit your existing roof bar feet. My wife made a kit-bag shaped waterproof cover but we don’t use that during car topping due to airflow effects causing chafe. And we acquired a thick stainless steel security cable so as to help retain ownership!
In total, the project came to £2,812 . Is it worth it compared to a rubber dinghy? The kit seems expensive and it could be built for less by sourcing your own materials. However, it made a nice winter project, and is a very special boat with multiple uses. It looks classic and simply beautiful. And, after all, it’s not every day your daughter gets married!
Cost breakdown
- Dinghy kit of materials: £1,280
- Sailing kit of materials (including timber for mast, boom and gaff, timber for rudder, tiller and daggerboard, a good quality lug sail and battens): £980
- Varnish, paint and painting materials: £200 (includes 2lt of varnish, 1lt of paint primer, 2lt of topcoat)
- Ropes and sailing fittings including buoyancy bags: £150
- Trolley wheels and wheel mountings: £65
- Oars and one extra pair of rowlock brackets: £137
Total cost: £2,812
Joss and Henry took her out for the first time in the summer at Newtown Creek, Isle of Wight. There was only a light breeze, but sufficient to see that the tender sails well with two adults aboard and that it will be pretty nimble sailed as a single-hander!
This useful little dinghy will have multiple uses for trips across the bay, the lake or up the river, as a yacht tender, for rowing, sailing, motoring, fishing and more. With its light weight at about 30kg it will be easy to handle and with its nesting design it will be handy to stow. And one day our grandchildren-to-be will learn to row, sail and mess about in boats in this excellent little dinghy.
Step by step: building a nesting Eastport Pram
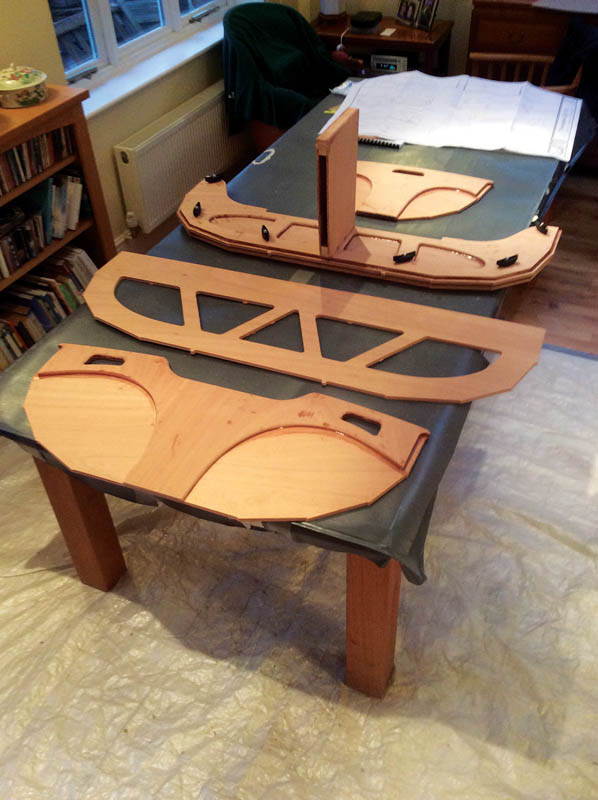
1. Assemble the laminated bulkheads (from top) bow, doubled-up centre bulkheads with daggerboard case and six wing-nuts under trial-fit, one temporary building frame, transom.
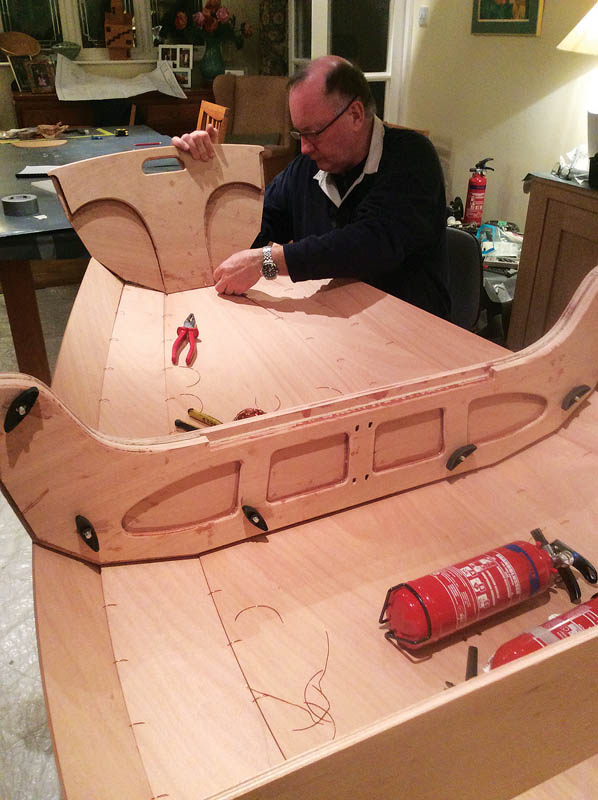
2. Stitch-in the bulkheads and bow section using copper wire. Fire extinguishers are there to provide weight to keep the curvature of the keel!
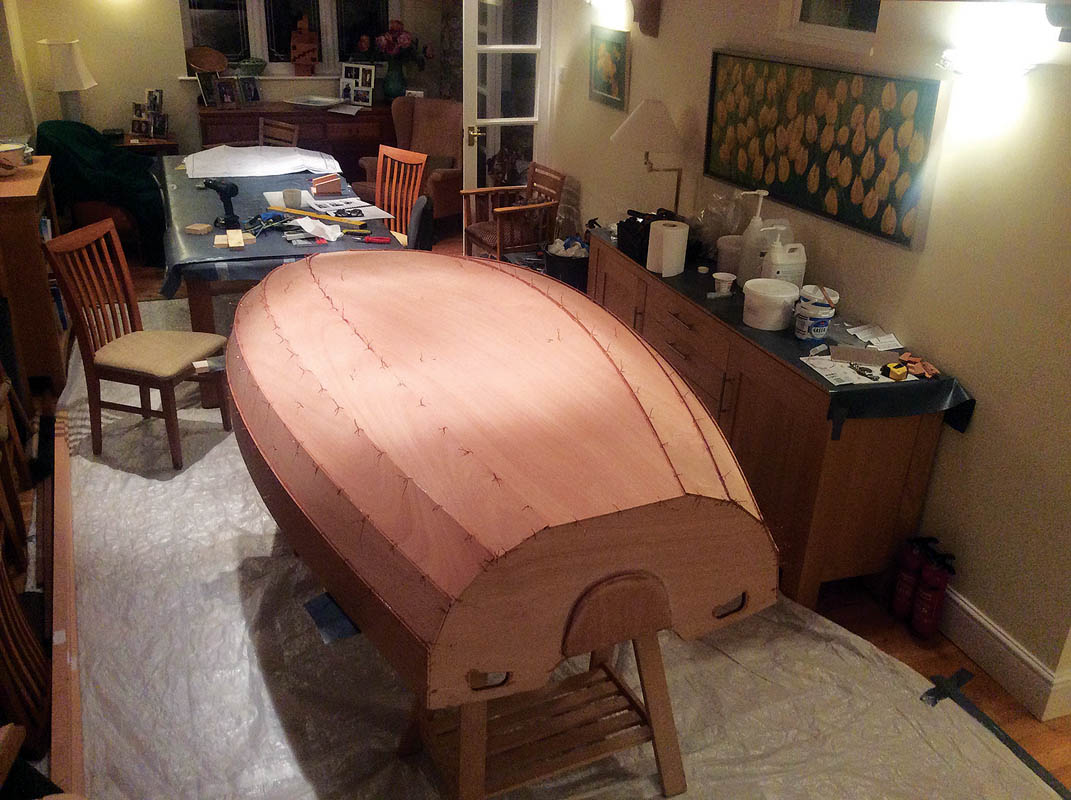
4. Invert the tender and level it carefully so as to remove any twist, ready to epoxy glue the seams.
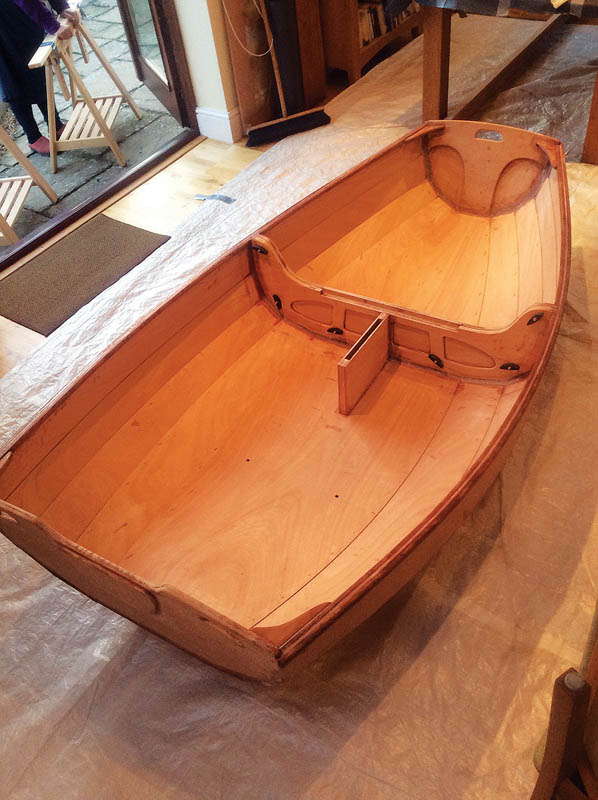
6. The temporary frame is removed, ready to commence glassfibre cloth/epoxy reinforcement of the sole. No seats yet visible!
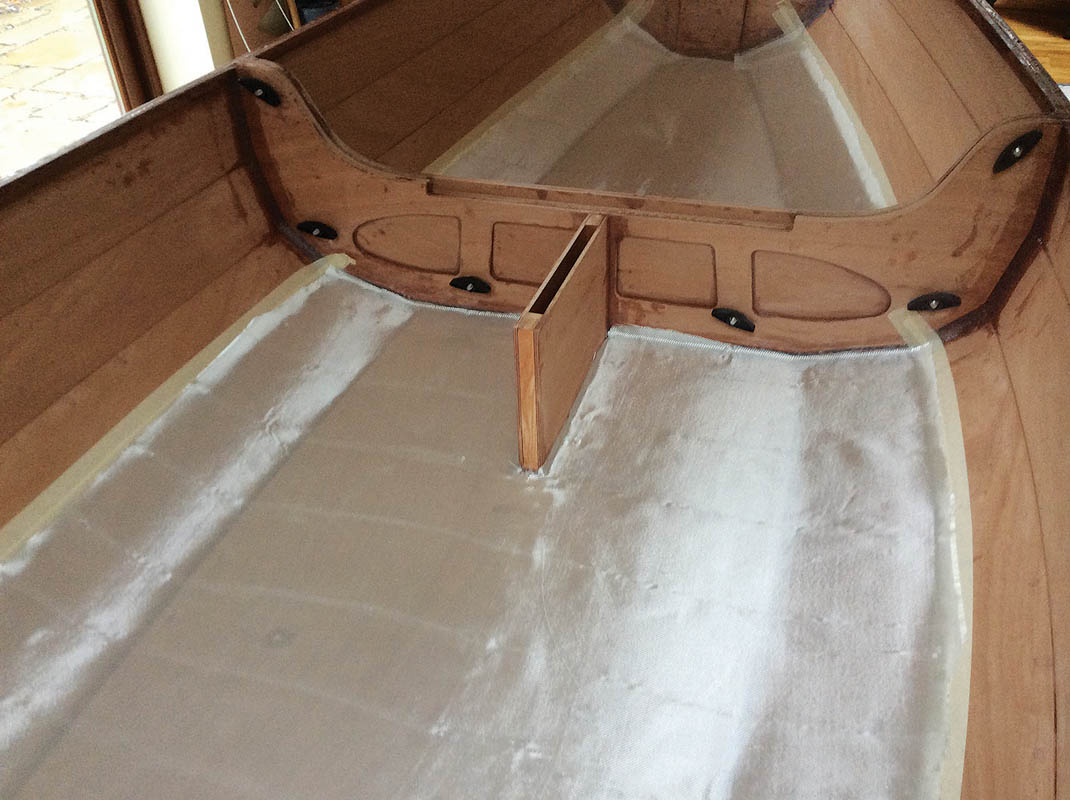
7. The glassfibre cloth is ready for roller-application of epoxy resin. Tape off the edges with masking tape.
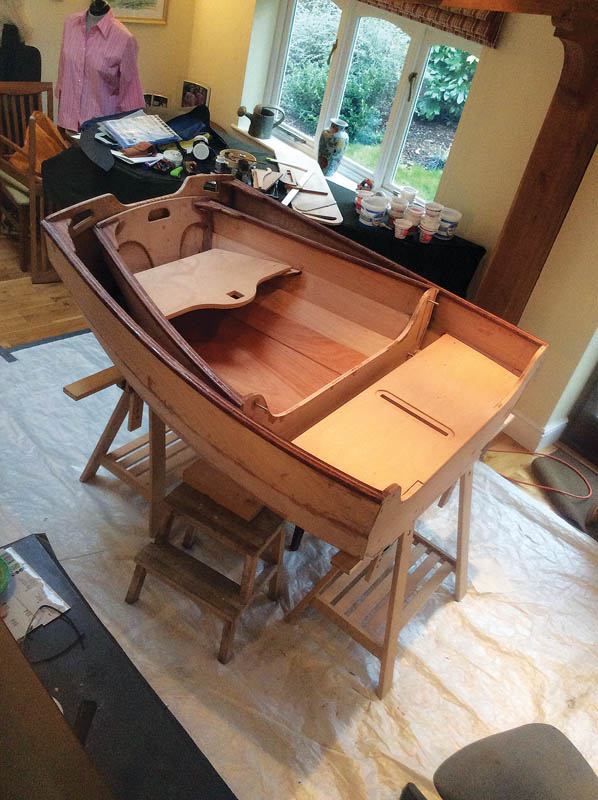
9. Epoxy glue the skeg and rubbing strips to the glassfibre epoxy-stiffened sole then cut the boat into two pieces. Here’s the two separated halves, showing how they nest.
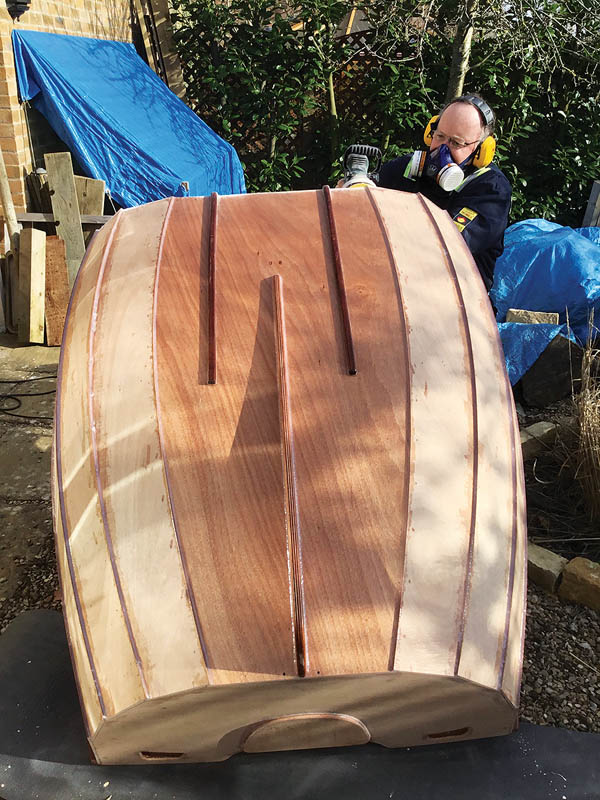
10. Machine-sand the hull as much as possible (this takes about two days) then move on to hand-sanding where the machine won’t reach.
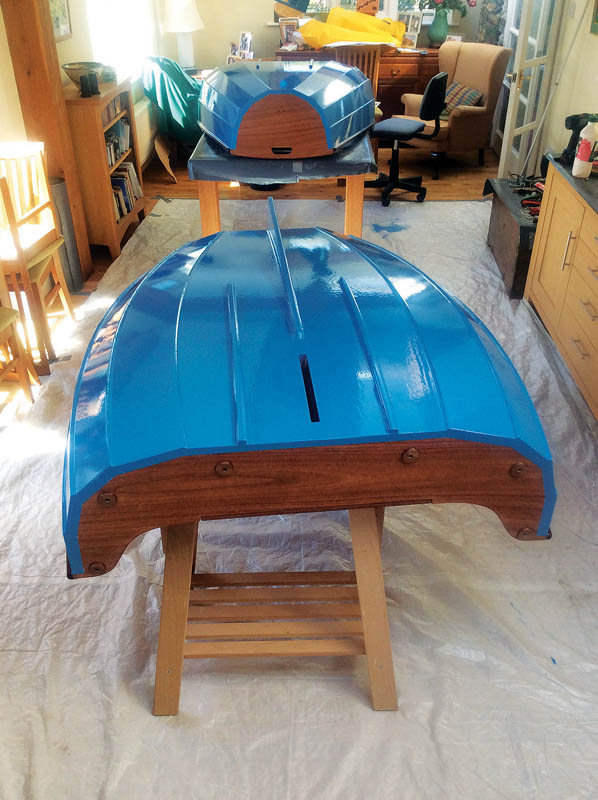
15. Paint the two hull halves. Note the 4mm thick spacers on the connecting bulkhead to control the joint stiffness and dimensions when bolted together.
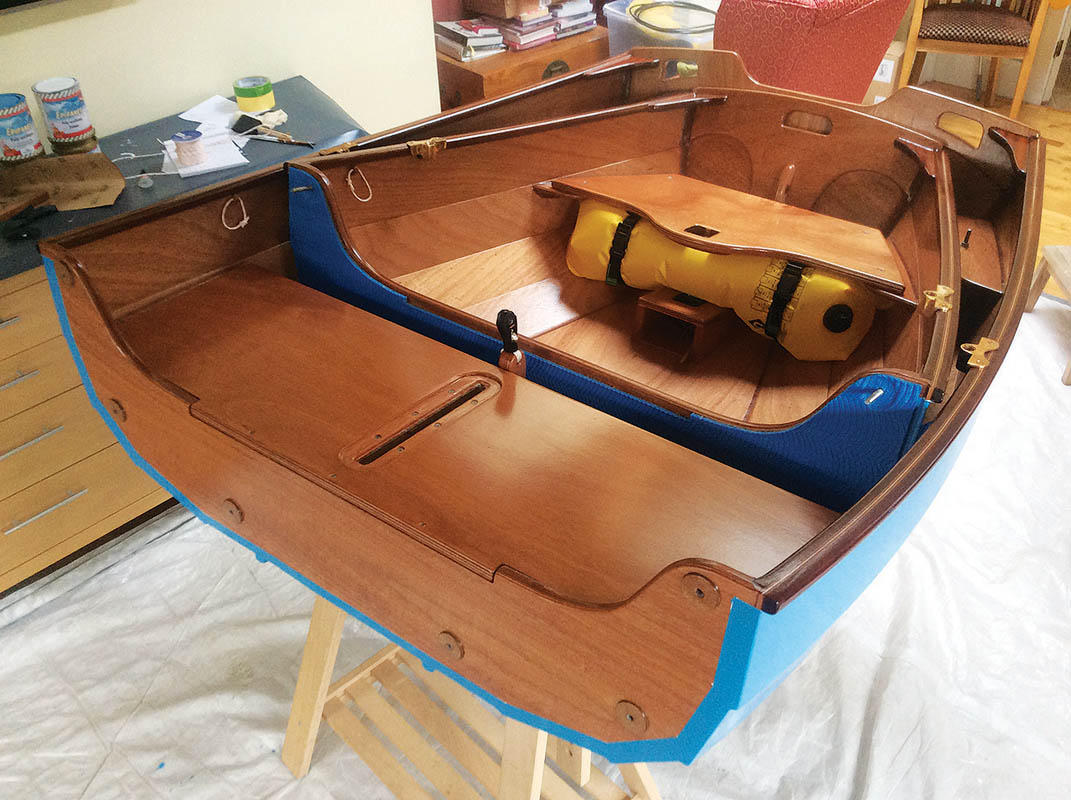
17. The bow half should now nest neatly inside the stern half. Note the aft seat is removed for nesting.
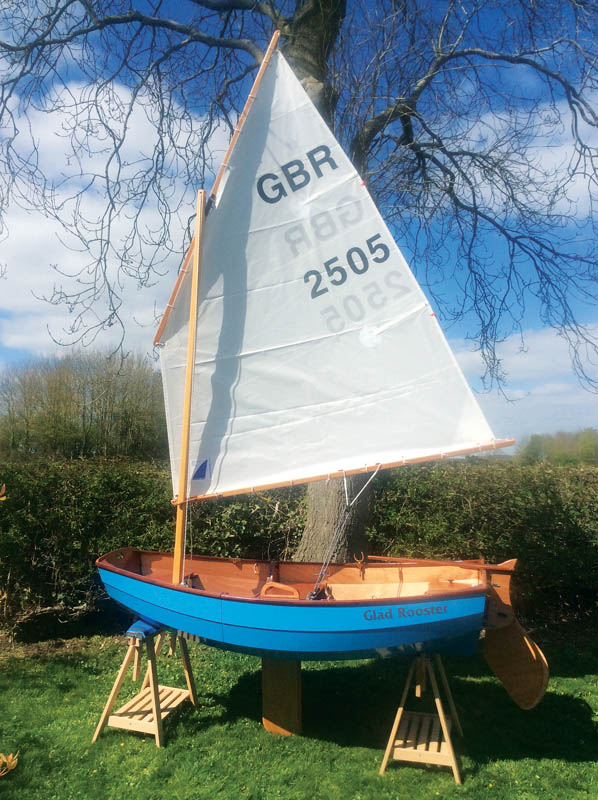
18. Time to trial-rig the sail. This one was provided by Goacher Sails. The sail number refers to the 25th May, the wedding day! Glad Rooster is Dutch for ‘slippery grid’ as in cattle grid!
Originally published in PBO Oct19