Filtration and fuel polishing can remove non-organic impurities but the solution to the dreaded diesel bug may be closer than you think
Engine maintenance is a mainstay of boat ownership but new technology has enabled the average boat owner to spend more time on sailing and less with his or her head in the bilge diagnosing engine ‘difficulties’.
However, where one door closes, another opens… and the diesel your old engine could happily convert into propulsion and exhaust might not be clean enough for any brand new souped-up replacement.
As marine diesel engines increasingly benefit from higher pressure fuel injection systems, the requirement for fuel purity also goes up. Filters and polishing will only get you so far: additives are also major players in the war against diesel bug and general fuel tank muck and sludge.
According to fuel treatment and testing experts CFCS, water contamination is present in diesel fuel from the moment it leaves the refinery, and it is water that leads to diesel bug. “Water in the fuel inhibits engine performance and will rapidly wear and oxidise engine components resulting in injection damage and seizure.”
So what is the solution? As we’ll see here, fuel polishing and filtering won’t cure diesel bug, but the contamination can cause fuel to damage the injectors and fail standard purity tests. An all-round fuel additive such as Coval Aquasolve dissolves any water mixed into the fuel while also stabilising and improving engine performance and reducing emissions.
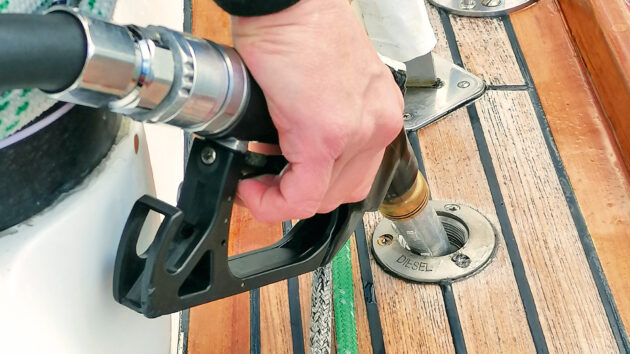
Filling diesel tanks is usually via a deck fitting – but a faulty filler screw cap can also allow water into the tank
Fuel standards
Diesel is tested for purity by means of a standardised ‘filter blocking tendency’ (FBT) test. The FBT determines whether fuel can potentially block filters in the distribution network or during use in a vehicle or power plant.
White diesel (EN590) and Red diesel (BS2869) are both modern low-sulphur diesel products that must conform to a measured level of FBT. The fuel is tested by passing 300ml through a 1.6µm (micron) disposable filter and recording the results.
There are two main reasons why a fuel can fail FBT testing: soluble compounds (also known as organic compounds) and insoluble (or hard) compounds.
Soluble compounds include diesel bug, cold-flow additives de-bonding within the fuel, waxing of fuel and metal carboxylates (soaps) – to name but a few.
Insoluble compounds can be in the form of induced contamination as particulates, just like we experience dust build up in our homes from particulates in the atmosphere.
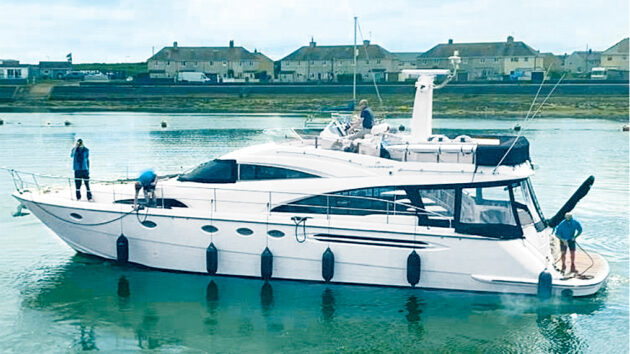
The owner of this Fairline Squadron 58 Flybridge uses Aquasolve
Particulate contamination
Engine manufacturers are constantly refining fuel injection systems to reduce emissions, improve performance and fuel consumption. Injection pressures have been increasing; currently, they have reached more than 2,000bar. Such levels of injection pressure demand reduced orifice sizes and component clearances, typically from 2-5µm in injectors. Small, hard particles, which may be carried into these engine parts, are potential sources of engine failure. Excessive diesel fuel contamination can cause premature clogging of diesel fuel filters, depending on the level of both hard and organic particles, and premature wear of modern fuel injection system parts. These impacts, depending on the size and the nature of the particles, will lead to:
- Reduced part lifetimes
- Part malfunction
- Engine failure
- Increased exhaust emissions
Insoluble contamination can be removed from the main fuel tanks by fuel polishing, utilizing different size micron rated filters.
The Worldwide Fuel Charter recommends that fuel should be supplied at a particulate level of 18/16/13 as expressed in the ISO4406 protocol.
The cleanliness code ‘18/16/13’ is made up of three numbers that identify the number of particles that are present in one millilitre of fuel:
- The first number (18) indicates the level of contamination by particles greater than 4µm
- The second number (16) indicates the level of contamination by particles greater than 6µm
- The third number (13) indicates the level of contamination by particles greater than 14µm
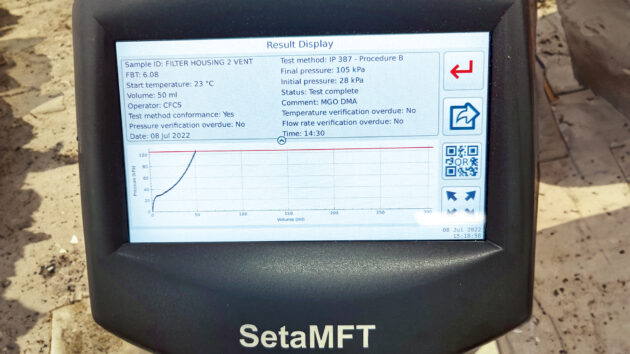
CFCS has tested Aquasolve’s effectiveness. These are the results of untreated fuel which failed with an FBT of 6.08. Once Aquasolve was added the organic compounds were solubilized and the fuel passed with a FBT of 1.07.
Additive advantages
The table below translates each of the range numbers into particle quantities:
Unfortunately, the ISO4406 testing protocol doesn’t identify whether it is soluble or insoluble compounds that are causing the fuel to fail. If the fuel is out of specification due to soluble compounds suspended within, the recommendation for fuel polishing would be the wrong course of action, as soluble compounds are not affected by fuel polishing.
A surfactant additive such as Aquasolve will sink to the bottom of the fuel tank where the water resides and, upon agitation, will permanently dissolve it – bonding the molecules to the fuel. If more water is introduced to the tank, Aquasolve will act upon that as well.
In addition, Aquasolve will:
- Improve fuel quality reducing consumption by up to 10%
- Reduce harmful emissions by up to 70%
- Reduce carbon residue in diesel fuel by 50%
- Increase the cetane number
- Improve oxidation stability by over 50%
- Prevent rusting and corrosion of components
- Enhance overall engine performance, cleansing filters and injectors
- Decrease filter blocking tendency
- Reduce maintenance costs
- Stabilise biofuels and ethanol fuels
- Increase flash point
Aquasolve is tested by Intertek to EN590:2013 specifications and is globally insured. Coval Technologies completed 12 years of R&D including extensive independent testing by The City University London. CFCS Analytical Services has also conducted its own case studies and testing on the effects of the product.
CFCS can be contacted at:
cfcs@contaminatedfuel.co.uk
or by ringing 0800 246 1008