Myles Lubbock explains how he converted his Albatross Mk3 Runabout to run off electric power alone...
Having bought an unfinished project boat from a couple who had started to convert a memorable aluminium craft into an electric boat, I was faced with the decision of whether to revert back to internal combustion (petrol) engine or continue to electric vehicle. I decided on the latter.
Now, after three years’ work, my Project eBoat of an Albatross 691 is complete. The boat sports a 30kW (40hp) water cooled motor, runs at 96V and can pull 500A at full speed.
The first year of the project focused on motor and controller integration, the second year saw trials with lead-acid batteries at 48V and year three’s focus was lithium-ion batteries at 96V. Recent trials have seen the boat achieve just under 30mph.
She’ll happily trundle the Broads rivers at 6mph for around four hours – so she has the ability to honour the original boat’s 1950s design.
The start
In the summer of 2019 I came across one of those ‘Marmite’ boats which, given its lack originality, doesn’t appeal to the well-seasoned Albatross fraternity.
It was an unfinished project by a couple who had wanted to convert one of these classic aluminium runabouts to electric propulsion, but unfortunately for one reason or another they were unable to see it through – so I bought it.
Article continues below…
Electric inboard boat motors: 3 yacht owners explain why they made the switch
Just a few years ago there were perhaps half-a-dozen manufacturers making electric outboards. Now there are nearly 40. We covered…
Why I chose serial electric hybrid propulsion with lead carbon batteries for my narrow boat
During the first lockdown in March 2020, my wife, Kay, and I began musing about the possibility of trying to…
Albatross Marine was a company formed shortly after the Second World War, utilising the skills and materials available to hand at the time to good effect. A riveted aluminium construction was the hull design and it weighed in at a modest 72ish kg.
The company was formed by Archie Peace and the honourable Peter Hives, son of the Rolls Royce chairman, and was based in St Olaves, near Great Yarmouth, in Norfolk.
Previous engine
The original boat was fitted with inboard marinised Ford Anglia 93A and 100E power plants, approximately 20-50hp, depending on spec and upgrades, later fundamentally up-spec’d to a 1,220cc Coventry Climax motor where a more significant and eyebrow raising power delivery of up to 70hp could be achieved with the much lighter power unit.
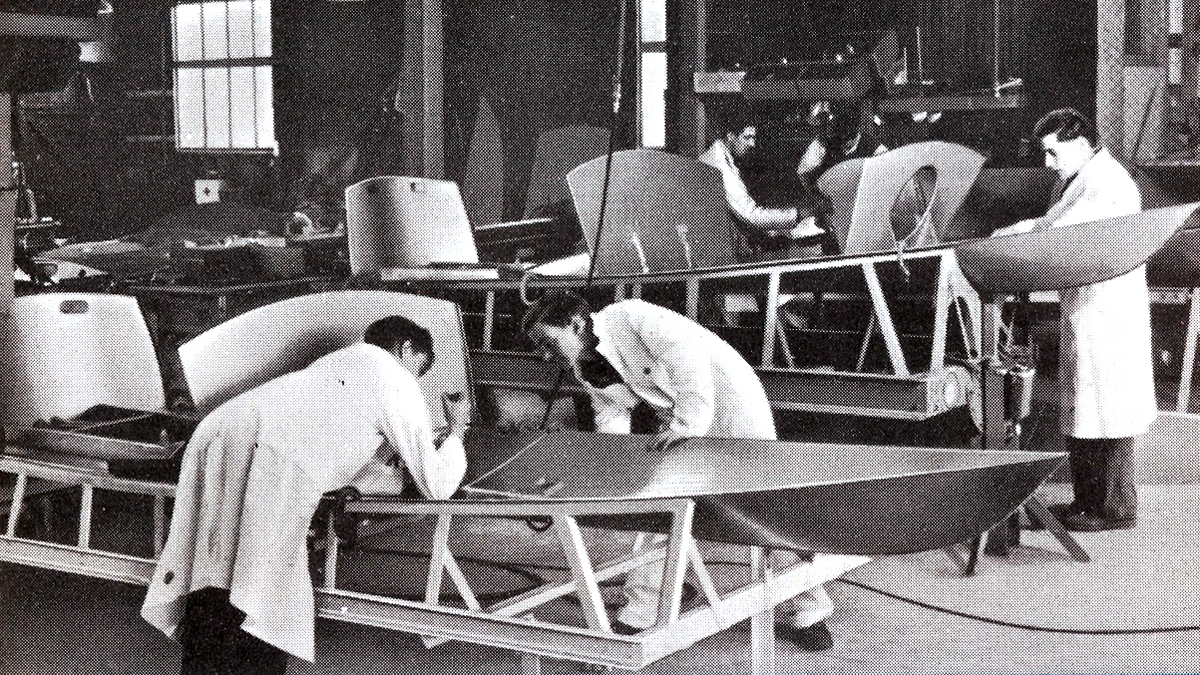
Albatross Marine workshop in full swing. Photo: Albatross Marine
This became a common water-skiing workhorse as well as a stylish tender for sizeable Mediterranean yachts. Customers included Brigitte Bardot, Aristotle Onassis, Prince Rainier of Monaco, Grace Kelly, George Formby, Prince Phillip, actor Jon Pertwee and the Prince of Greece.
Fibreglass construction techniques and outboard engines paved the way to the end of this post-war marque in the early 1960s. There was, however, to be light at the end of the tunnel; John and Charlotte Fildes have done an outstanding job of reviving the Albatross Marine name with an online parts shop, lots of knowledge, expertise, and advice.
As well as supplying original and reproduction parts, they also restore the original boats to their former glory, if not slightly better, in my opinion! The history of Albatross Marine is fascinating and more can be found on their website: AlbatrossMarine.co.uk
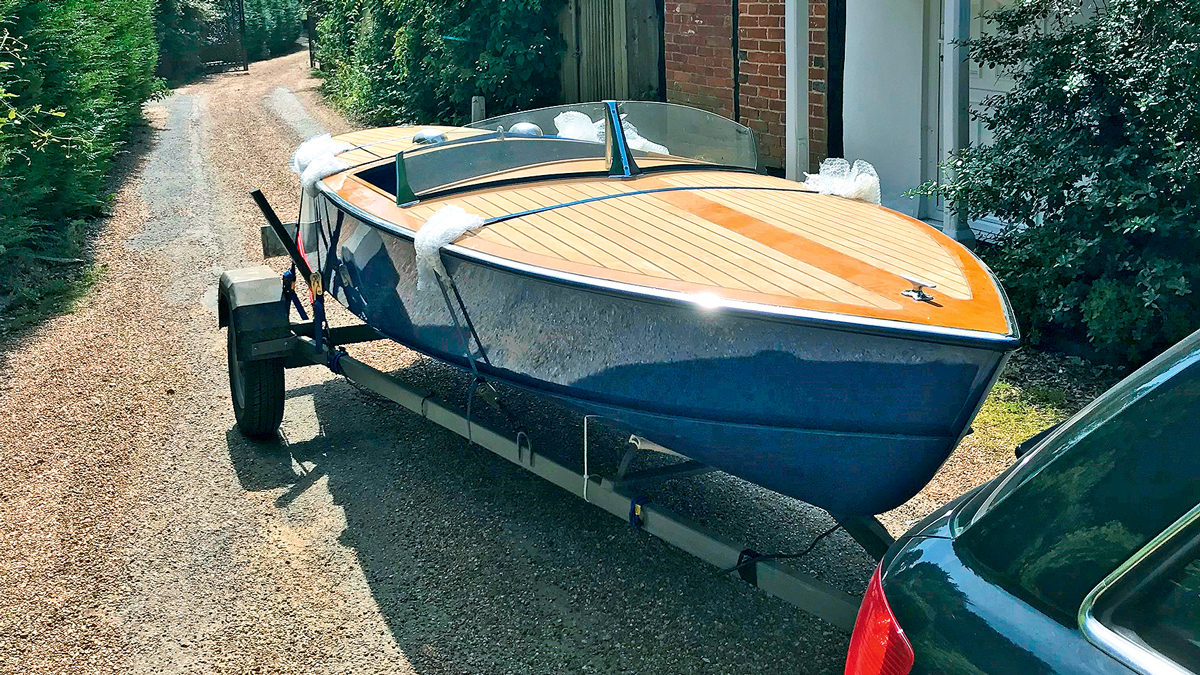
Day one, pick up
Carte blanche
The first year focused on specification, design and installation. I ventured to London to pick up the boat, and a few hundred yards down the road I had to stop and take stock of my purchase – Wow, what a stunner, though not necessarily to everyone’s taste!
All restoration credit must go to John and Charlotte, of Albatross Marine, who I’m sure put numerous hours into this craft to get it to this stage. Soon after the collection of the boat I had some decisions to make: a) return it to its former glory with a Coventry Climax engine (rare as the proverbial hen’s teeth!) or b) continue the quest of converting the boat to electric propulsion.
Having an interest in electro-mechanical gadgetry and having been advised that trying to lay my hands on a Coventry Climax was as challenging and costly as a trip to the moon, I decided to proceed with going electric. How hard could it be?
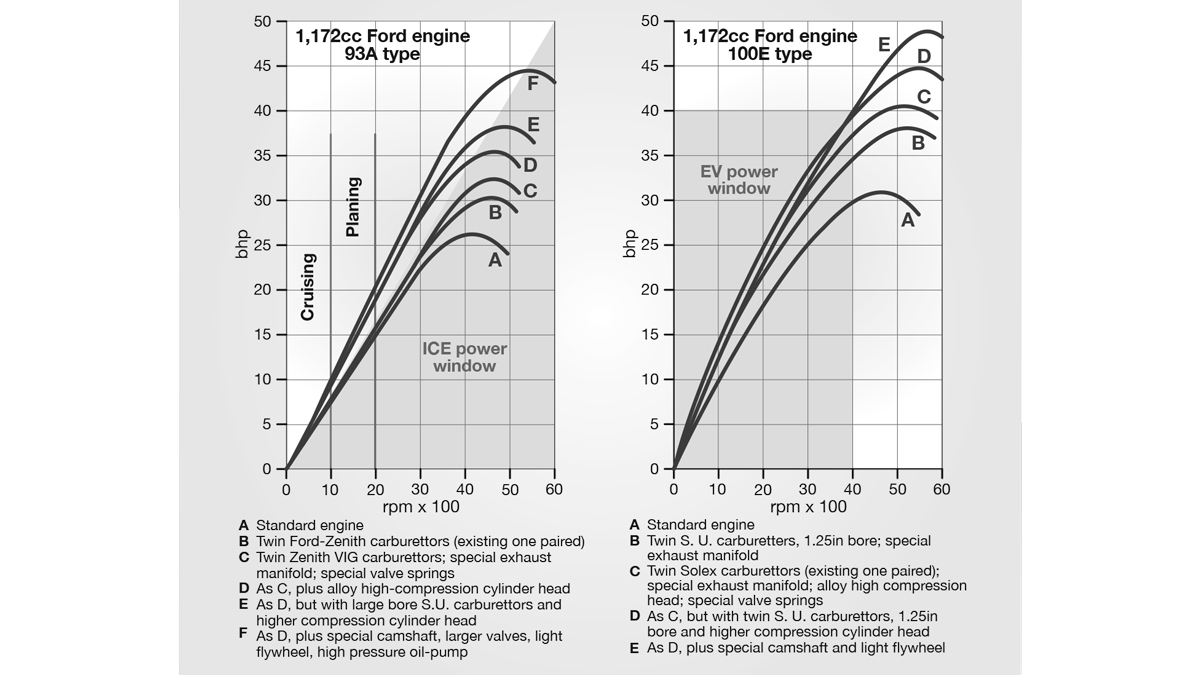
Original power outputs for Ford 93A & 100E engines
Firstly, I sought costs from specialist conversion companies to do the integration. They all asked: what capacity, voltage, prop speed and range do you want to achieve? I did some rudimentary fag-packet calculations and soon became horrified when I realised the weight and the cost of what I wanted.
One company quoted ‘Speedboats remain a frontier, due to low battery power density and maximum voltage limitations’. ‘The battery for your project would be too heavy.’
Knowing battery chemistry and this technological field was advancing rapidly, I thought I could compromise on range but wanted to honour the original ability to plane and, ideally, pull a water-skier. I put some ideas in to graphical representations in an attempt to understand the scope of what I was trying to achieve.
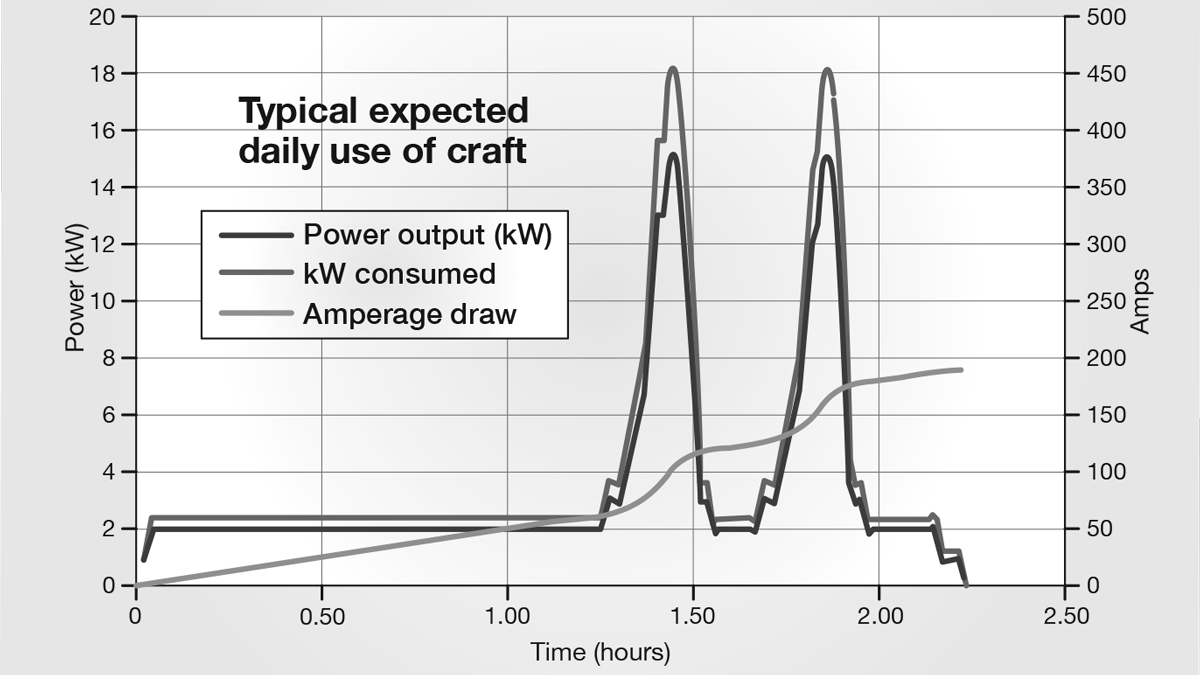
Assumed duty cycle and energy consumption
After much to-ing and fro-ing I came up with some approximations for motors, controllers and batteries to give me a starting point:
- Motor >30kW (40hp)
- Battery 48-100V (initially lead-acid)
- Controller 500A peak (which requires approximately 70mm2 cables!) and fully software configurable
- 2 hours range at river speed (around 4kWh)
- 15 minutes range at full beans
Given this as a starting point I could look for the equipment for the installation. Other than the complexity of situating the equipment, I was faced with a question of whether I needed to gear up or down to the propshaft.
I was advised I needed a 2:1 ratio (motor:prop) to maximise motor efficiency. River trials I initially opted for 48V lead-acid batteries – a combination of four extremely large and heavy 12V leisure batteries connected in series. For the first year this seemed the most sensible, cost-effective route.
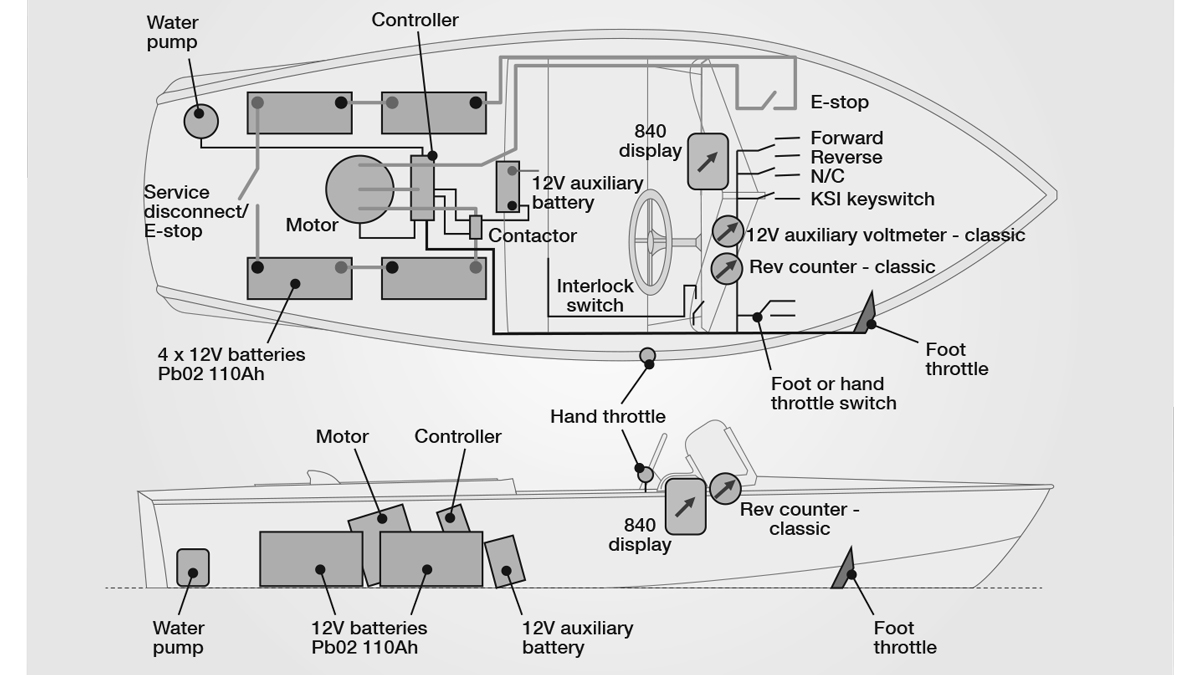
Electrical layout
Meanwhile, a 2:1 belt driven gear ratio system was also adopted. A breathtaking sum of ‘hobby money’ was costed towards re-engineering the controller software to include subtle features to pay homage to the original design, including twin throttle, foot and hand controls, an analogue rev-counter to show prop speed on a nice Smiths-like gauge.
A new wiring loom also had to be designed from scratch to accommodate service disconnects, contactors, as well as a safe domestic charging system. In the second year, the first trials with the 48V lead-acid batteries took place.
My friend Mike Bishop, owner of an Albatross Mk3 and a Continental, offered to chaperone my maiden voyage on the Orwell at Levington Marina. Before we did, I registered the boat with the Norfolk Broads Authority and got it BSS certified.
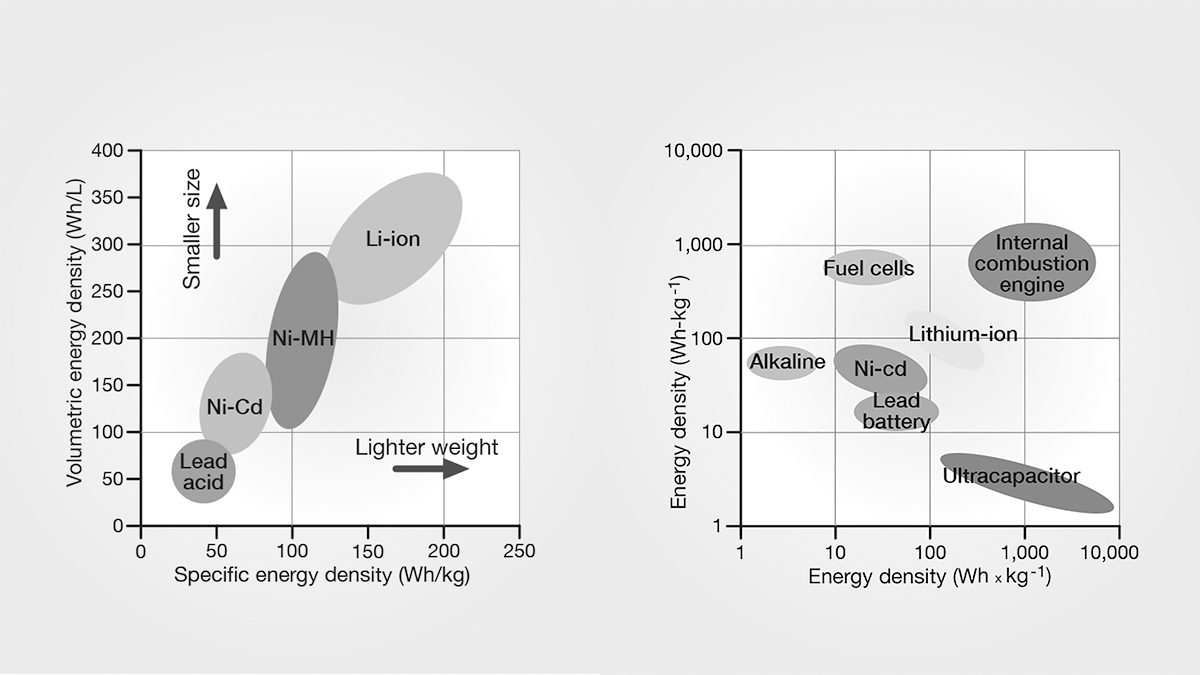
Battery chemistry & power estimations
I thought a second set of well experienced eyes and some third-party insurance would be a worthwhile investment. CC Marine at Beccles was happy to oblige. Initial trials were good, benign and rather uneventful. It functioned well but didn’t reach anywhere near its desired potential.
I recorded a maximum of around 8mph on my Garmin cycle computer at full speed. I had some thinking to do. On the plus side it was completely dry in the engine compartment. It had very usable manoeuvrability which the original design lacked due to the propshaft being directly attached to the crankshaft.
A negative was the whine from the belt drive gearbox – electric vehicles should be quiet. More importantly, at full throttle I was only seeing 8mph! Electric motors are intrinsically linked to voltage, so no matter how much current you have to hand the motor would not spin more than approximately 45 times the voltage.
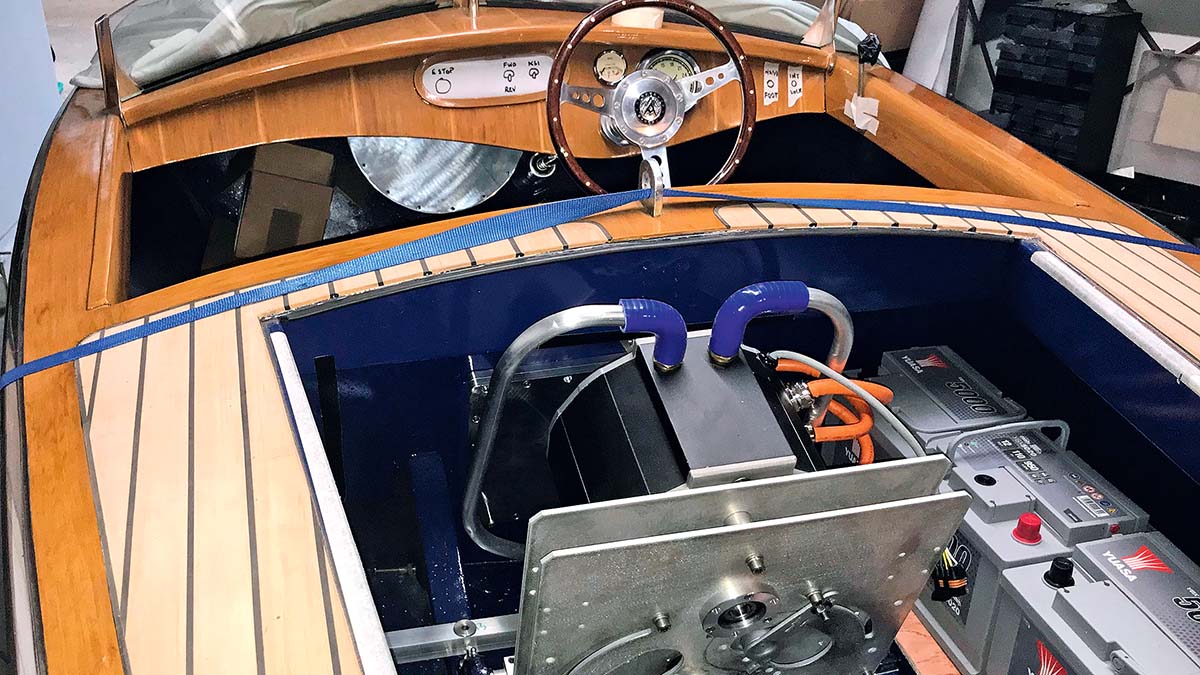
Motor and gear system installed in-situ with battery layout
In my case that was around 2,000rpm at the motor and only 1,000rpm at the prop – little more than tickover! Drivetrain In the project’s third year, I removed the belt-driven gearbox and decided to go direct drive.
This would at least double my output at the prop and improve efficiency by losing the rotating masses, and shedding a little bit of mass. This meant I would lose efficiency at low rpm, but was a compromise I was willing to accept as now I aimed to get to at least 2,000rpm; in fact somewhere north of 4,000rpm peak is where I was heading.
At yet more expense the lead-acid batteries were replaced with lithium-ion modules. I opted for four packs offering a nominal voltage of 90V. This would notionally achieve 4,300rpm at the prop and as the weight of the battery pack was around half that of the lead-acid I felt we were heading in the right direction.
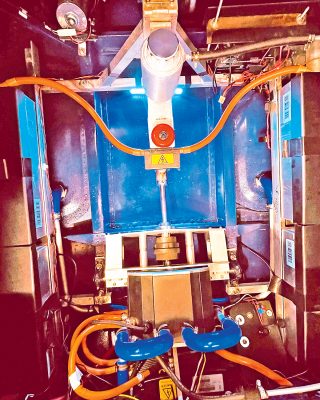
Installation year three – direct drive and lithium-ion batteries
I spent a large chunk of year three trying to get my head around a suitable battery management system (BMS) for this application.
In simplistic terms a good BMS will monitor cell voltage and temperature, current flowing in and out of the entire pack and make decisions whether the battery pack is stable.
If not, the circuit is broken via circuit breakers. As well as keeping the pack running in a ‘safe’ operating window, a suitable BMS will balance the cell voltages; a good sequence of cells in series ensures all links in the chain are strong.
Sea trials
Last autumn, we took to the water with a lighter, more powerful boat. Alas, something was still amiss. The prop would only rotate at about 1,500rpm, not enough for it to ‘get over the hump’ and plane.
After much drifting along the Orwell, tweaking software parameters, I found a technical glitch with the speed control algorithm, freed it up and off we went, as it should, like a rocket… it was electric! I recorded 28.8mph on the Garmin and it planed from about 1,600rpm.
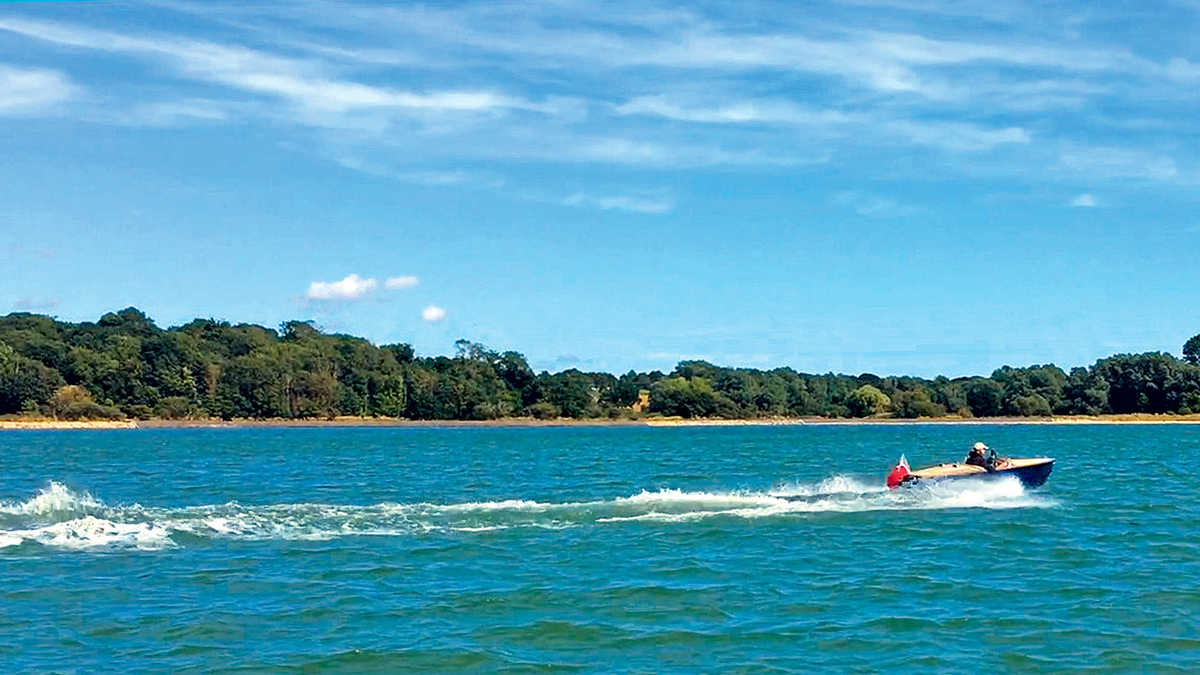
Albatross at speed on the Orwell
We did four full speed runs and logged as much data as possible. Mission almost accomplished. Very usefully, data can be recorded from the controller.
In the diagram below you can see the prop speed recorded on the day was around 4,000rpm, maximum current of approximately 400A and, given the pack voltage was 90V we can calculate that the power peaked at about 36kW.
A trip down the river for a benign trundle was the last outing for 2022. I launched the boat at Brundall Marine and headed towards Cantley along the river Yare. My target was to cruise at 5-6mph while monitoring power consumption to get a feel for the range and current consumption in the interests of efficiency.
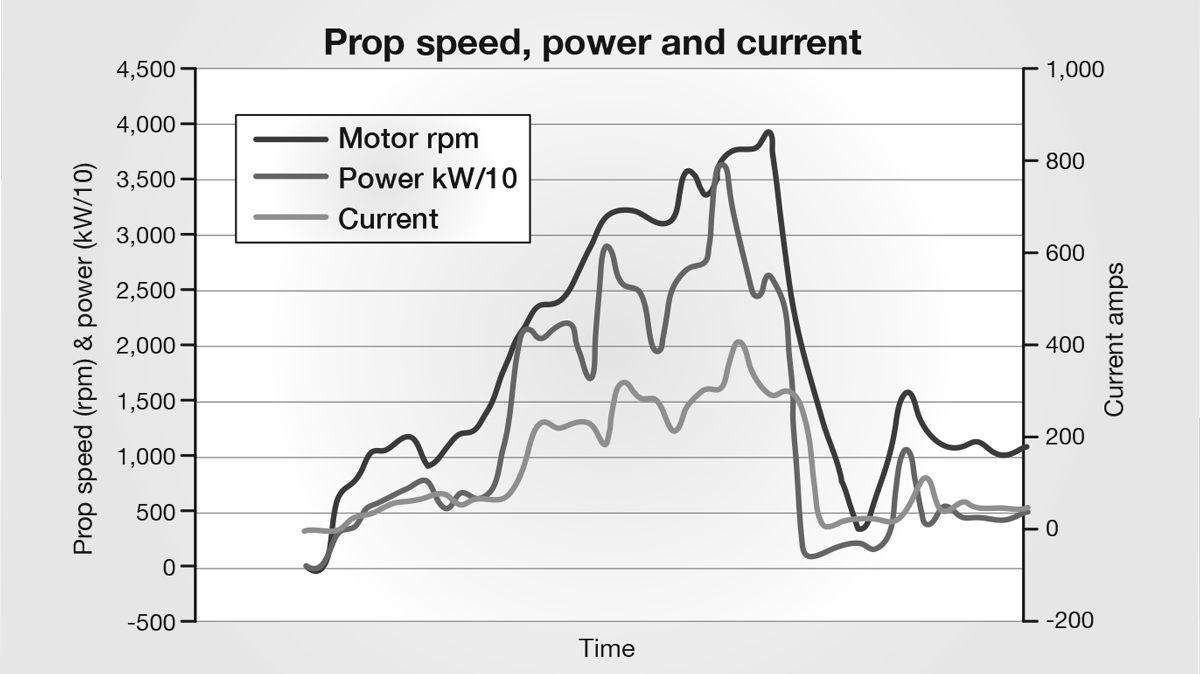
Data logged for power run on the Orwell
This proved a worthwhile exercise; I realised there was a significant difference between 5mph and 6mph in terms of power consumption. I started the trip at 96V and ended around 91V so roughly about 50% state of charge – perfect for a four-hour river trundle.
Work to do
Next upgrade will be to adopt a domestic charging system which can be charged at home or on the Broads. Plus, housing the lithium-ion batteries in splash-proof boxes with battery management on display through polycarbonate lids.
Until I’ve successfully pulled a waterskier, I won’t be entirely happy, but with a bit of luck that should be on the cards for early 2023. And of course, giving it an appropriate name!
Electric boat conversion costs
- Hull and associated parts: £4,500
- Drivetrain: £2,000
- Controller and software: £6,000
- Batteries and electrical: £5,000
- Consumables: £1,000
- Total: £18,500 (approx)
- Hours: 1000’s!
Why not subscribe today?
This feature appeared in the May 2023 edition of Practical Boat Owner. For more articles like this, including DIY, money-saving advice, great boat projects, expert tips and ways to improve your boat’s performance, take out a magazine subscription to Britain’s best-selling boating magazine.
Subscribe, or make a gift for someone else, and you’ll always save at least 30% compared to newsstand prices.
See the latest PBO subscription deals on magazinesdirect.com