Every boat owner should know some basic engine maintenance. Stu Davies shares how to tension the alternator drive belt
Alternator belt tensioning: step-by-step
V-belts, also known as alternator belts or fan belts, (a throwback to our car days when the belt drove the cooling fan for the radiator), are used on boat engines to transmit power to water pumps and alternators.
The V name we use for its shape is not strictly correct, but is in common use.
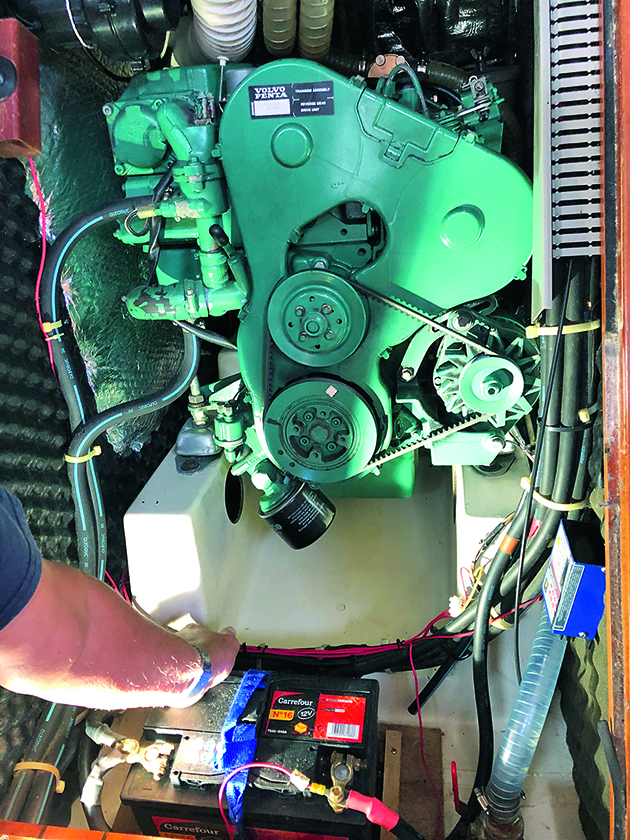
On most boat engines, the V-belt is easy to access and adjust. Credit: Stu Davies
The correct name for the belt’s shape is trapezoidal, a quadrilateral with one pair of parallel sides. V-belts are usually made from rubber or synthetic material with built-in reinforcing fibres.
They’re simple but efficient.
Alternator belt tensioning: how the belt works
Their V shape allows them to fit into a matching groove on a pulley. Not many people realise that V-belts ‘drive’ through their sides which offers greater contact surface area between the belt and pulley.
They are tensioned to keep that contact with the sides of the V, NOT the bottom of the pulley.
If the belt wears sufficiently to touch the bottom of the pulley it is effectively worn out and will slip as it loses contact with its driving V.
V-belts are available in many different sizes, but in the marine environment, we normally only see the A-size, which has a small 13mm width.
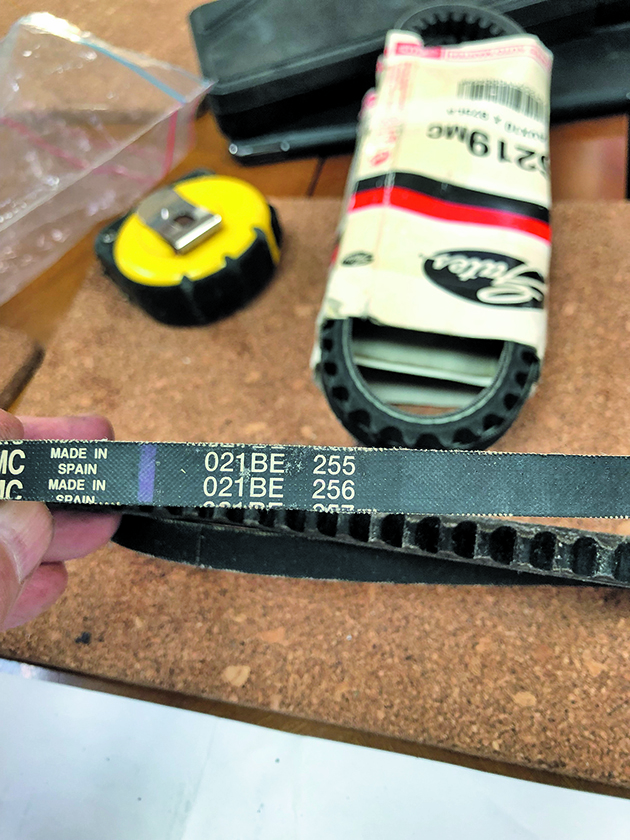
Stu prefers a ribbed V-belt which provides better contact. Credit: Stu Davies
Bigger ones can transmit more power but also absorb more power as they pass over the pulleys.
Usually on boat engines, the manufacturer uses a double A configuration if more power is needed.
Some of them come with just a simple solid V-shape while others – which I prefer, – come with ribs which allow more flexibility and better contact between the contact surface area between the belt and pulley.
I suspect they also run cooler than solid V-belts due to their better flexibility.
They have their limitations and the A-size belt on my Volvo Penta MD22 is about at its limit driving my 60A alternator with its Sterling alternator booster.
Originally I had a simple solid V-belt which wore quickly; fitting the ribbed belt cured that. Drive belts are widely available online from a variety of specialist retailers and motor manufacturers.
When to change your the belt
A sure sign that your V-belt is wearing is seeing black dust gathering in the alternator area.
Tensioning it is quite simple BUT there are several caveats.
Usually, they drive the fresh water pump as well as the alternator and tightening them too much puts excessive strain on the pump’s bearings.
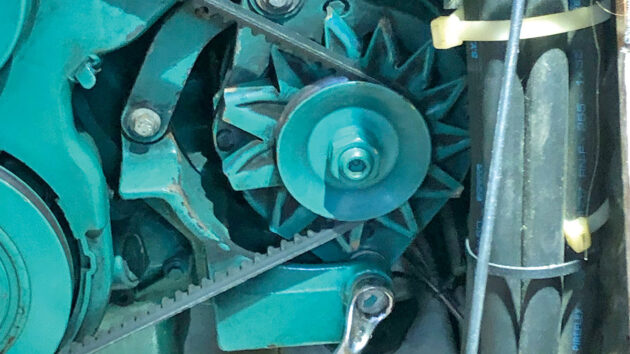
Black dust is a sure sign that your belt is worn. Credit: Stu Davies
The alternator is usually where the tension adjustments are made. The alternator has a major pivot point bolt, usually about 12mm thick, several minor adjustment bolts and a slotted plate.
If you see black dust gathering and hear the pulleys making a squealing noise then it is time to adjust the tension.
A good clue is that if you can grip the alternator pulley and turn it even slightly with your fingers, it is too slack.
Before carrying on, it’s a good idea to check that the V-belt hasn’t worn so much that it is bottoming on the pulley
Alternator belt tensioning
To tension the V-belt, the large pivot point bolt has to be slackened just enough to allow the alternator to swivel.
The adjusting slotted plate needs its minor swivel bolt slackening; the slot bolt should also be loosened.
A bar or something similar is needed to ‘lever’ the alternator until the V-belt is tight.
The slotted plate bolt is then nipped up followed by the major pivot bolt.
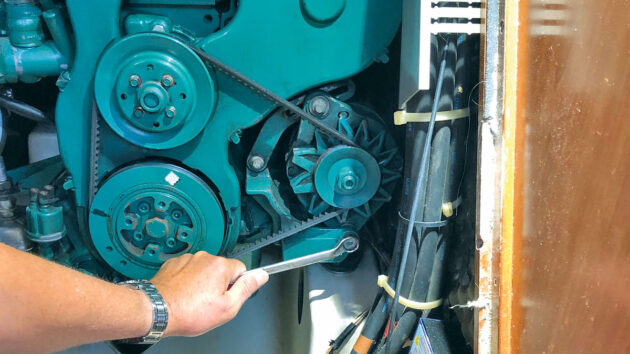
The large main alternator pivot point bolt, which needed to be loosened. Credit: Stu Davies
People often ask if the bar can be levered on the alternator to tighten the belt. Care is needed so that you don’t lever on something fragile.
I’ve found that a hammer’s wooden handle is the right fit between the alternator and the engine casting and can be safely used because it is relatively ‘soft’ and doesn’t damage anything.
A piece of brush handle can be handy in situations like this too.
I have also used a spanner because I knew I could position it so it wouldn’t cause any damage.
Use whatever you have to lever the alternator away from the engine, being careful not to use too much force, and then ‘nip’ the adjusting pivot and slot bolts to hold the alternator in place.
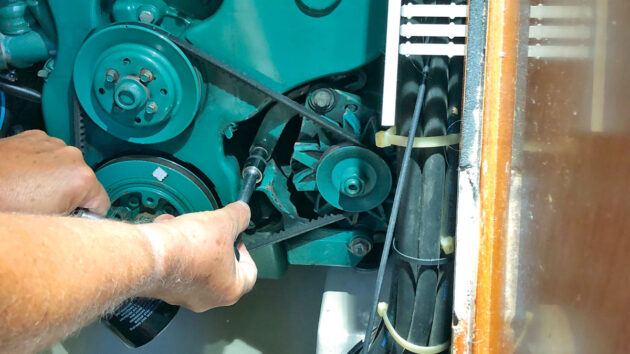
The minor swivel bolt on the adjusting slotted plate. Credit: Stu Davies
Then tighten up all the adjusting pivot bolts and check the tension on the V-belt.
This is done by pushing with a finger on the longest side span of the V-belt.
The belt is correctly tensioned when it can be deflected (pushed in) by 1cm. Much less than that and it’s too tight, any more and it’s too loose.
That’s it; a simple job that’ll save you a bit of cash by doing it yourself.
The belt should be checked regularly (every 20 sailing hours) for tension, cracks and wear.
5 top causes of boat engine failure – and how to avoid them
Jake Kavanagh talks to Sea Start marine engineer Nick Eales about how to avoid the five major causes of an…
How to change a water pump impeller
Stu Davies shows you how to check and replace an engine’s raw water pump impeller, and explains why it’s an…
How to service an outboard engine: step by step
Stu Davies shares useful maintenance tips on how to keep your 2-stroke and 4-stroke outboard motors running sweetly
How to service a marine diesel engine in 12 simple steps
It was time to service the marine diesel engine on our Maxi 84 cruiser. Knowing how to diagnose and fix…
Want to read more practical articles like Alternator belt tensioning: step-by-step?
A subscription to Practical Boat Owner magazine costs around 40% less than the cover price.
Print and digital editions are available through Magazines Direct – where you can also find the latest deals.
PBO is packed with information to help you get the most from boat ownership – whether sail or power.
-
-
-
- Take your DIY skills to the next level with trusted advice on boat maintenance and repairs
- Impartial in-depth gear reviews
- Practical cruising tips for making the most of your time afloat
-
-
Follow us on Facebook, Instagram, TikTok and Twitter