Metallurgist Vyv Cox’s guide to anodes, explaining how they work, debunking the myths and showing ways of improving performance
The purpose and function of boat anodes can be complex, leading to confusion as to their location, connection and operation.
This article explains the basics of how they work, how to use them and why we need them.
Why do we need boat anodes?
The majority of metals, whether a single element or an alloy of two or more, undergo a gradual return to their natural lowest energy state, a process known as corrosion.
The rate at which metals corrode is determined by the environment to which they are exposed, so in the air most metals degrade quite slowly, in fresh water faster and in sea water, a very aggressive environment, sometimes quite quickly.
Some alloys, such as stainless steels and aluminium, benefit from the formation of surface films that resist corrosion, whereas others such as carbon steels corrode rapidly in their natural condition.
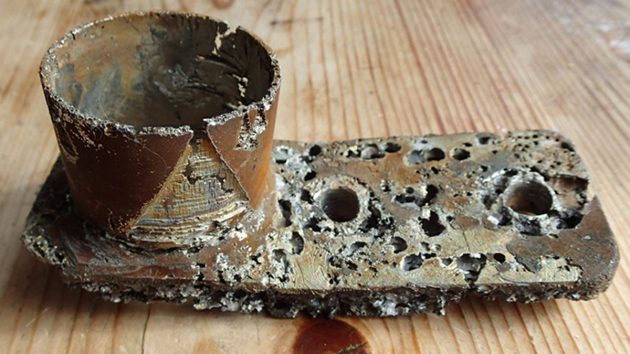
If the passive film on the surface of stainless steel is damaged the result can be pitting, caused by a galvanic reaction between the passive surface film and the active substrate. Credit: Vyv Cox
Unfortunately, these passive films can be compromised by local damage, which allows aggressive environments access to the underlying unprotected metal, resulting in pitting.
Many means of delaying or preventing the corrosion of underwater components are used on boats, including galvanising, painting and impervious coatings of various types but for a variety of reasons these may not be applicable.
Instead, we use boat anodes, which instead of excluding water from the metal’s surface use chemistry to protect them.
How do boat anodes work?
To demonstrate the simplest case we connect two dissimilar metals electrically, either by direct contact or with a wire between them, and immerse them in a liquid. Two things will happen.
Firstly, one of the metals will corrode and the other will not. Secondly, a voltage will be generated between them. We have just invented the battery!
This mechanism can be observed with every combination of single elements and alloys in existence, numbering thousands of combinations.
During well over a century the voltages between metals have been measured, but for simplification, all are now measured against a reference electrode made from silver, coated with silver chloride.
The voltages measured against this standard electrode can be plotted in a table, but for greater convenience, they are normally shown graphically in what is known as the Galvanic Series.
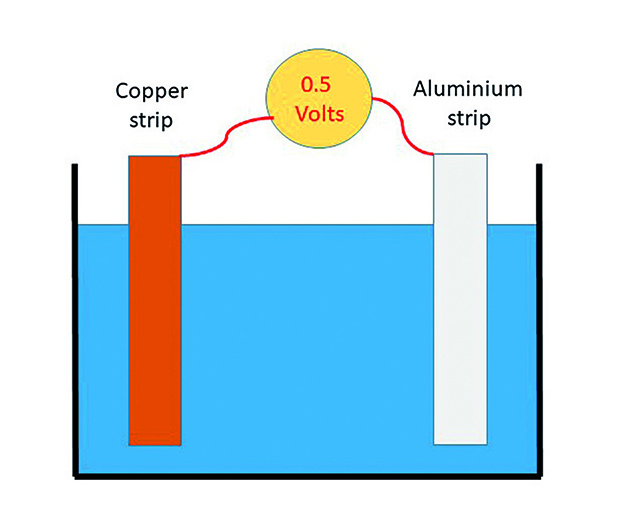
Connect two dissimilar metals and immerse them in seawater and two things will happen – one of the metals will start to corrode and a voltage will be generated between them. Credit: Vyv Cox
The series differs according to the environment but for this article, the galvanic series in seawater will be used.
The chart (below), from my book Metals in Boats, is a simplified version that shows only the most common metals and alloys.
It can be seen that metals on the left side of the chart have a neutral or slightly positive voltage, known as noble, whereas those on the right are negative and known as anodic.
Reference to this chart tells us which of the metals in our immersion test will corrode: it will always be the anodic one.
Thus the metals at the extreme right of the chart are those that we know as anodes, namely magnesium. zinc and aluminium.
Each of these may be used in differing circumstances and, in practice, are not composed of pure metals but are alloys with small additions of other elements.
How to use boat anodes
You may have seen photographs of offshore steel fabrications before launch.
These structures are liberally supplied with anodes to delay the onset of corrosion. Once launched they are replaced regularly by divers.
These anodes are universally made from aluminium, which is cheaper, more plentiful and lighter for transport purposes than zinc.
This application is the simplest example of cathodic protection, the aluminium anode corrodes in protecting the steel.
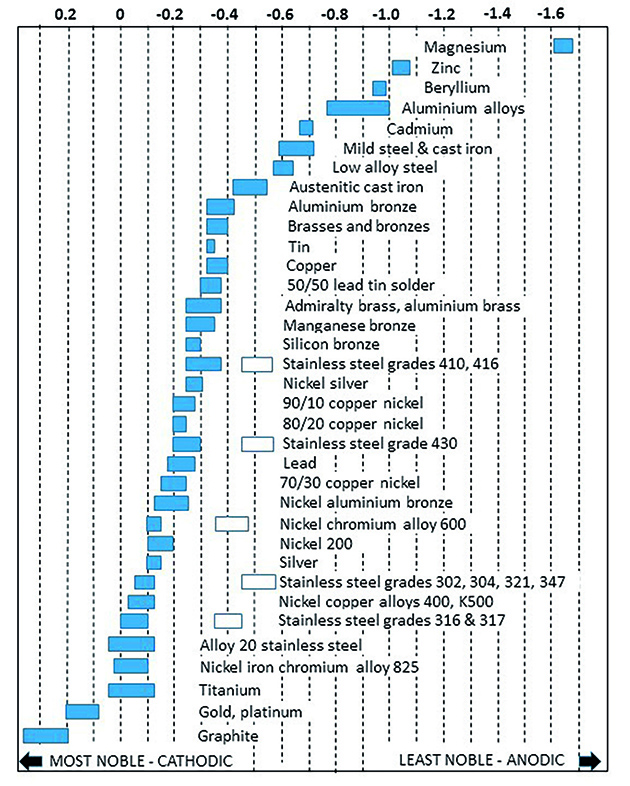
The galvanic series of common metals and alloys. Noble, or cathodic metals to the left, less noble or anodic to the right. Note that metals whose corrosion resistance is derived from a surface film have both passive (surface) and active (substrate) voltages. Credit: Vyv Cox
In boats, the use of anodes is more complex because we are dealing with more than one construction metal.
For example, a manganese bronze propeller on a stainless steel shaft is in itself a galvanic couple.
Reference to the chart shows manganese bronze to have a voltage of -0.3 and 316 stainless steel -0.05.
This means that without protection the propeller will be consumed in protecting the shaft, a far from ideal situation.
The addition of a zinc or aluminium anode changes the situation, with the anode now being consumed in preference to either of the others.
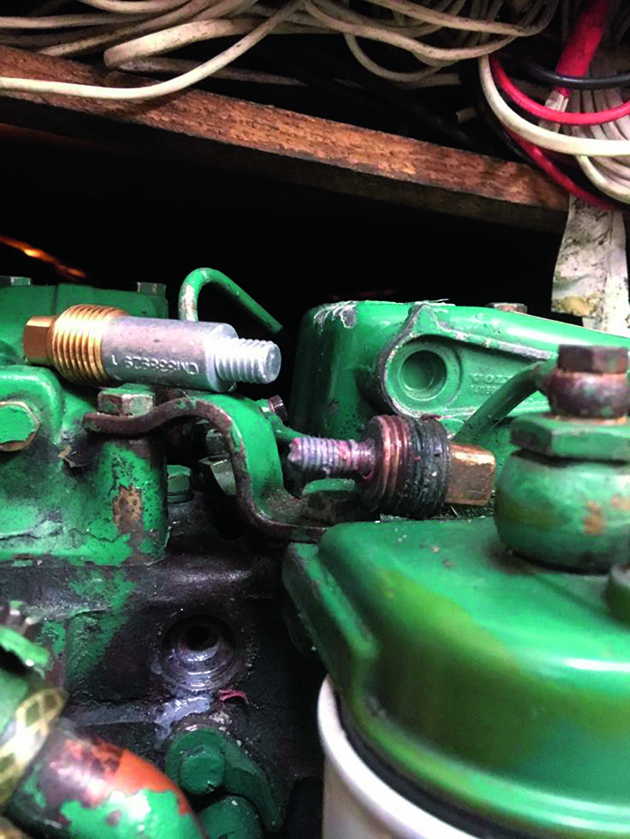
Engine anodes protect the internals of the cooling passages. They are a pencil-type that screws onto a short bolt that is itself screwed into the engine block. Some heat exchangers have similar anodes
The situation becomes more complex with folding or feathering propellers, where the hub and blades may have different compositions, being assembled using stainless steel pins.
Again, an anode will protect the total combination.
Some simple rules apply to the use of anodes to derive maximum benefit from them.
Firstly, they must be in good electrical contact with the object being protected.
When checking these connections with a meter the total resistance should be less than 0.2 ohms and ideally zero.
Seeing straight
Although seawater conducts electricity, it does so to a limited extent, so the nearer the anode is placed to the object being protected the more effective it becomes.
Thirdly, the anode should be able to ‘see’ the object being protected. Ions in seawater travel in almost straight lines and do not like to turn corners, so a hull anode placed amidships is unlikely to protect anything at all and definitely not stern gear.
Thus the shaft anode, placed a short distance forward of the P-bracket, satisfies all of these requirements well, which accounts for its popularity.
Continues below…
Why are boat owners being urged to switch to aluminium anodes?
Boat owners and boatbuilders across the UK are being urged to switch from zinc to aluminium anodes to help marine…
How to: check and change an anode
Galvanic corrosion is a phenomenon that affects the majority of boats. If you have two dissimilar metals, such as stainless…
Boat anode protection: How much do I need to prevent corrosion?
PBO reader Arthur Gilbert asks: “Is it necessary, and if so where, to fit anodes on my recently acquired Leisure…
Maintenance on a boat: 71-point skipper’s checklist
Make sure your boat is ready to go back in the water with Practical Boat Owner's comprehensive guide
In boats where the shaft is not exposed ahead of the propeller, it is normal to place an anode as close as practicable to the shaft and propeller while arranging a wire inside the boat to connect to the propeller.
This may be connected to the gearbox if there is good electrical continuity to the shaft via the coupling, or if this is not the case the coupling can have conductors bolted between the flanges on each side.
If this is not possible the wire can be connected to a brass brush that rubs on the shaft.
In many cases, after-market propellers with complex metallurgies will have their own anode that offers additional protection to supplement the action of the shaft anode.
Saildrives
Saildrive casings are made from an aluminium alloy. They are therefore susceptible to fairly rapid corrosion by seawater.
This can be exacerbated by the connection to more cathodic metals, particularly propellers.
Many original equipment propellers intended for saildrives have a rubber insulating bush between them and the shaft to avoid the possibility of galvanic corrosion.
If this propeller is to be replaced by an after-market one it should be ensured that the possibility of increased corrosion rates has been addressed.
Corrosion protection of saildrives is addressed in two ways.

The protective coating on this saildrive is failing and needs to be renewed after a thorough cleaning. Corrosion is beginning to take hold and both anodes need to be replaced. Credit: Vyv Cox
Firstly, a non-conducting paint film is applied. It is essential that this be kept in good condition and renewed as needed.
Copper-based antifouling, which would be cathodic to the aluminium alloy, must be avoided.
Modern Volvo saildrives and gearboxes are totally isolated from the engine and this isolation must be maintained by ensuring that the gaiter is kept clean and dry and that no connection is made between it and the rest of the boat.
Yanmar saildrives are not isolated, which makes the coating and anode particularly important.
The coating system used is epoxy based, requiring thorough cleaning before renewal.
As the heading anode materials shows, it is perfectly possible to use an aluminium anode to protect an aluminium saildrive leg.
Many manufacturers are now producing these, although zinc ones remain available.
Some misunderstandings about boat anodes
A small anode offers very little protection to a large component.
Many boat anodes might be needed as size increases. (In fact some structures have a Direct Current (DC) passed between anode and object so that the metal becomes more cathodic, suppressing corrosion further).
Attaching an anode to an iron keel serves no useful purpose.
The anode will be consumed quickly in trying to do its job but the effect will be minimal.
Painting the keel offers far more useful protection. An engine cannot be protected by an external anode.
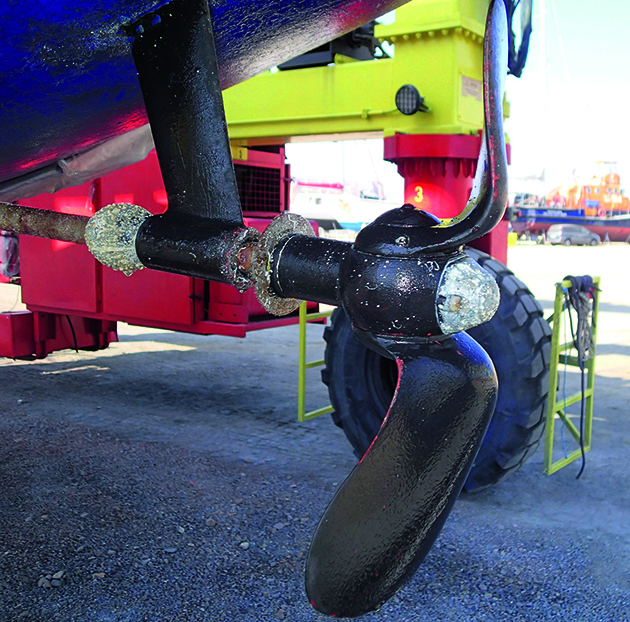
A propeller anode, secured with nylon screws to avoid excessive loss around metal ones, and a shaft anode attached close to the propeller. Anode life has doubled by painting the propeller, reducing the size of the cathode. Credit: Vyv Cox
A hose cannot possibly act as a substitute for a wire and thus ions cannot pass between the anode and engine.
Raw-water cooled engines and some heat exchangers have their own internal anodes, which thus will be in the same body of water where they can exchange ions.
Bonding, which is the practice of connecting underwater components such as seacocks together by a wire inside the boat, and thence to an anode, has no merit for corrosion protection (although it is common on USA-built boats primarily for lightning protection).
Not only is it virtually impossible for an anode to ‘see’ all of the components in the circuit but any poor connection or loss of the anode can result in one seacock corroding preferentially to protect another.
Modern thinking is to make seacocks from materials that resist corrosion, such as DZR, bronze and plastic that need no additional protection.
Never connect an anode to your battery.
Connection to the positive terminal can lead to massive amounts of damage in a very short time and even a negative connection may show a slight voltage compared with the earth of the engine, gearbox or keel.
Improving anode performance
If anodes are consumed more rapidly than required by annual haul-out periods there are a few things that can be done.
Shaft anodes can be doubled up, larger propeller anodes can be fitted and an anode on a wire, connected to the drive shaft, can be hung over the side when berthed, again following the ‘line of sight’ rule.
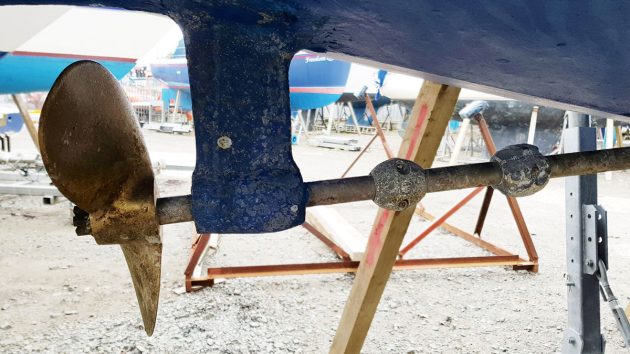
This anode would be more effective if placed nearer to the propeller. There is no reason to separate it by such a large distance. Credit: Vyv Cox
Another option is to paint the object being protected, typically a propeller.
This reduces the area of the cathode, making the anode’s life easier.
I have done this with my propeller, resulting in a doubling of both prop and shaft anode life.
Anode materials
Over many years the basic anode metallic elements have been subtly modified to improve performance and overcome problems.
One is that in fresh water, zinc develops a white insoluble coating of zinc hydroxide that inhibits its operation.
Rapid corrosion can ensue when the now unprotected boat returns to the sea.
For many years it was suggested that aluminium anodes should be used in these circumstances but of course, this did not apply to saildrives.
To address this situation the manufacturers developed an aluminium alloy that has the same galvanic potential as zinc and this can be used in all circumstances as a substitute.
At present, anodes are available in both metals but it is likely that the far more expensive zinc version will gradually be phased out.
As can be seen in the diagram above, the galvanic potential of zinc to the specification Mil-A-18001H and aluminium with small additions of zinc and indium are almost identical.
Both are anodic to the aluminium alloys used for saildrives.
Magnesium anodes can be used in fresh water lakes but they will be consumed in a matter of days in brackish or sea water.
What about anodes for wooden boats?
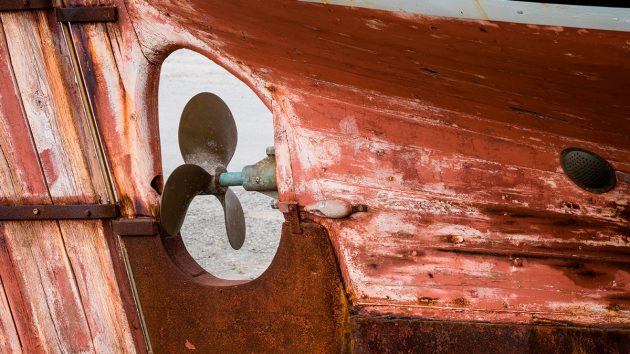
Caution needs to be taken when fitting an anode to wooden boats with a high moisture content; it could soften the wood. Credit: Alexander McClearn/Alamy
PBO sought advice from James Beale, the managing director of MG DUFF, which specialises in marine cathodic protection systems and boat anodes
With older wooden vessels you do need to be careful with sacrificial anodes.
The byproduct of cathodic protection is an alkaline environment generated around the anode and items that are being protected in the bonding circuit (prop, A- or P-brackets, rudder stock etc).
Older wooden vessels may have high moisture content in the timber, allowing the alkalinity to affect the structure of the timber making it soft.
This is known as electrochemical decay (ECD).
Signs that you may be suffering from ECD are softening to the planks and white crystals forming internally on the bonded items.
These white crystals should be washed away with fresh water.
On wooden vessels already showing these signs I’d advise not to fit a hull-mounted anode.
Instead, use a hanging anode, this moves the anode away from the hull lessening the effect of the alkalinity while still providing protection.
Another option would be to fit a shaft and prop nut anode only.
These items will only provide good protection to the prop and shaft, though.
Enjoyed reading Boat anodes: a practical guide for sailors? 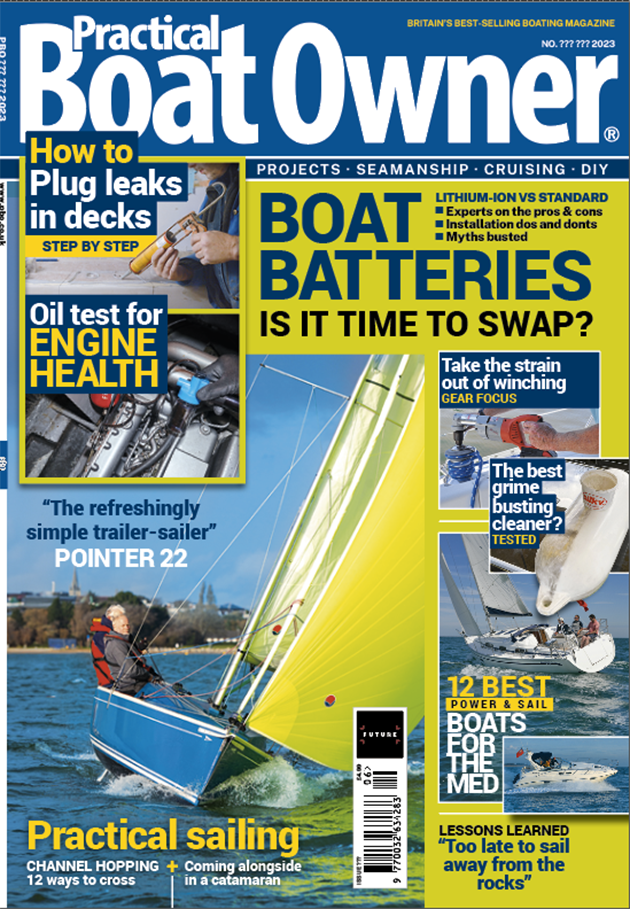
A subscription to Practical Boat Owner magazine costs around 40% less than the cover price.
Print and digital editions are available through Magazines Direct – where you can also find the latest deals.
PBO is packed with information to help you get the most from boat ownership – whether sail or power.
-
-
-
- Take your DIY skills to the next level with trusted advice on boat maintenance and repairs
- Impartial in-depth gear reviews
- Practical cruising tips for making the most of your time afloat
-
-
Follow us on Facebook, Instagram, TikTok and Twitter