Boatbuilder and finisher Lyndon March explains which types of wood work best for different repairs and modifications on board
Boat wood: a complete guide for yacht owners
Repairs, replacements and restorations are very much part and parcel of boat ownership.
At some point most of us will have to tackle a small, niggling woodwork repair ourselves, or undertake a larger-scale project.
However, are you making the correct choices when it comes to choosing the timber to use?
Like most items associated with boats, there is not a definitive right or wrong approach, but guidance is useful.
We often think of stout working boats as built of larch or oak and finer yachts dripping in teak and mahogany.
This is not always the golden rule though.
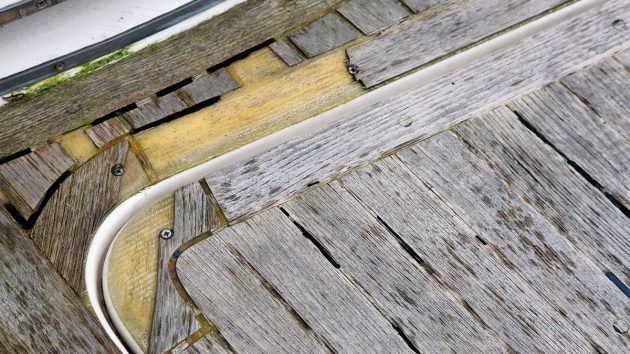
You may be able to source reclaimed teak to make repairs to small areas of deck
It’s worth keeping in mind the three key points when looking for the right wood for your project: durability, movement and structural integrity.
If your choice in material is informed by these golden rules you can make smart decisions and execute a lasting repair or update to your vessel.
Most commonly it’s the high-impact areas of a boat that require renewing, like grab rails, rubbing strakes and toe rails.
Exposed, vulnerable and rarely finished with more than a simple oil, these are the parts of the vessel that take a pounding during the season, doing very little for the longevity of the timber.
For most craft manufactured pre-1990, these areas will almost certainly be made of teak.
Owners are advised to look after teak with careful cleaning to increase its life, especially as teak is scarce.
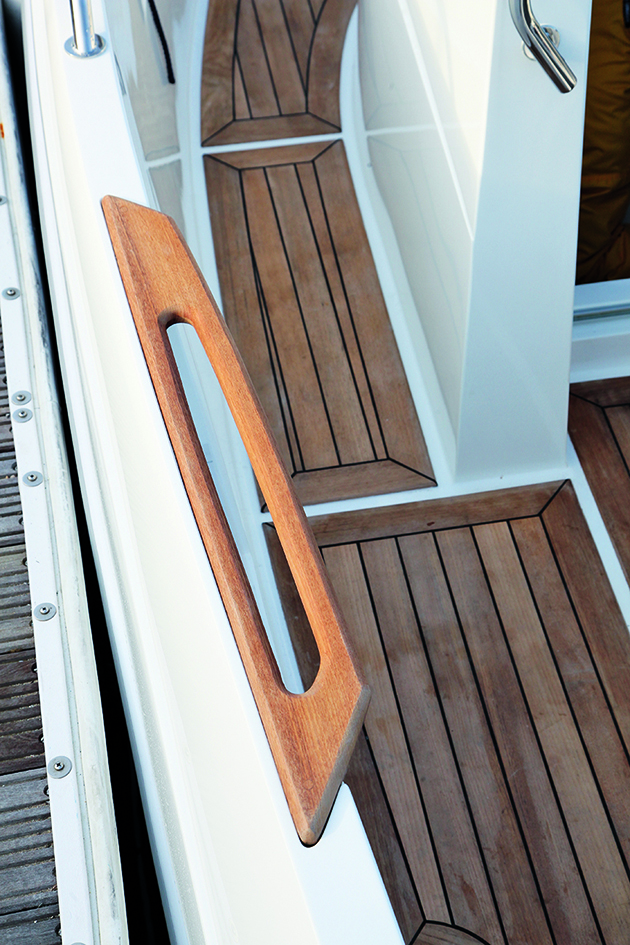
Grab rails and toe rails are often made of teak, so look after them. Credit: William Payne Photography
However, if it does need replacing, you may be able to grab a bargain on the second-hand market, given the small amount of wood you’re likely to need.
Teak is a wonderful material, with an ability to weather gently and an almost self-oiling quality.
It also fits all of our key points – scoring highly on durability and movement as well as structural integrity.
Teak can also be used almost anywhere in a vessel; as demonstrated in my own 1901 rowing dinghy which is entirely built of teak.
Fortunately, but not without some hunting around, there are small quantities of teak still lurking in timber yards around the country, and certain specialists such as Trinity Marine carry stocks of reclaimed teak; however, it is expensive and requires some careful machining to minimise wastage.
There are big challenges in sourcing teak which is legal and ecologically sustainable.
Boat wood: Alternatives to teak
Being realistic about the affordability of the wonderful oily teak forces us to look within the mahogany family or iroko.
Both meet our three golden rules; with iroko giving us a bit more structural integrity and providing much more durability in the weather if left uncoated or oil finished.
Khaya, sapele and utile mahoganies will easily hold up as toe rails and rubbing strakes and, much like iroko, give us wonderful grain results but really require a varnish to add protection and longevity.
A future world without the availability of teak forces us to look at other areas of our vessels that might need repairs; decks, cockpit gratings, hatches and skylights.
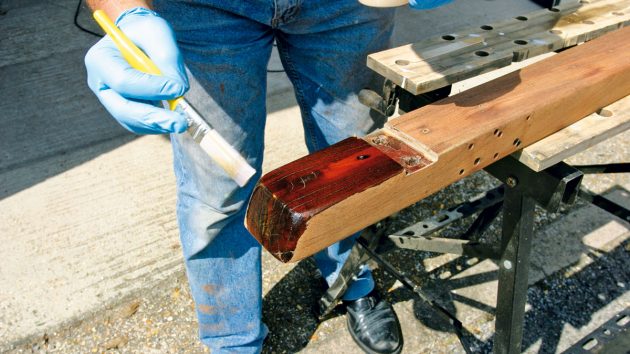
Mahogany needs varnishing in order to protect the wood and increase longevity
If these are teak, then it pays to look after them.
Those of us fortunate enough not to have a traditional laid deck might still have deck planking or at least deck coverings.
It’s not uncommon for vessels to have a teak-clad deck or at least some teak trim, pulpit perches or cockpit locker lids.
Years of enthusiastic deck scrubbing, clumsy feet, or gentle sanding often leave teak decks in a bad state of repair, with the screw plugs barely hanging on for life.
For smaller sections, you may be able to hunt down some elusive teak but for bigger areas of decking, you’ll need to look for an alternative.
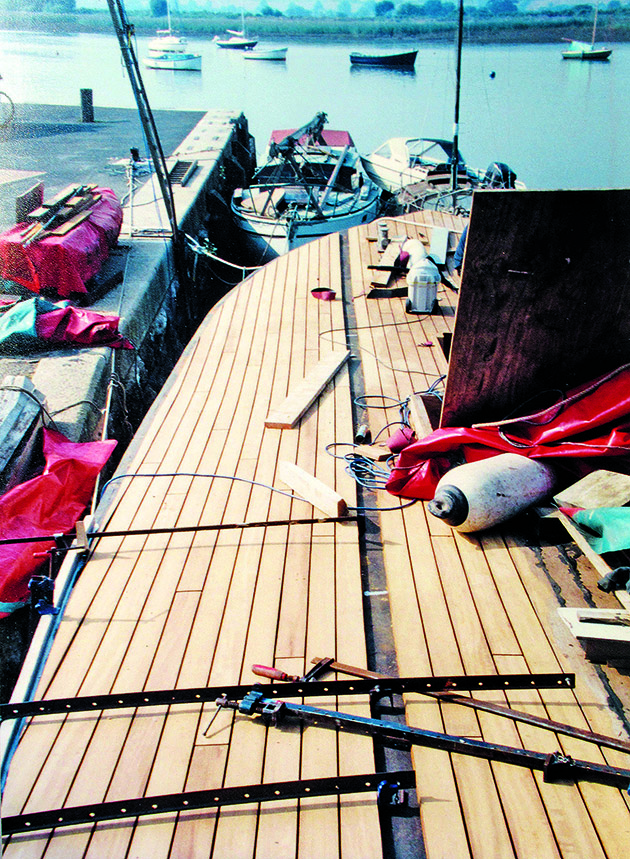
Iroko can be matched to existing teak, which makes it ideal for decking. Credit: Hazel McCabe
Iroko could be the perfect alternative to teak. Unfortunately, it’s not particularly nice to work with and some people have suffered allergic reactions to it, so it’s advisable to don personal protective equipment (PPE) when working with iroko.
Iroko can, however, provide you with a teak-style of deck that should give a hardly noticeable match to existing teak.
It can be left to weather or be oiled and varnished with stunning results.
If you’re replacing a large area, or laying all new decking, I’d recommend taking some inspiration from the working boat scene.
Douglas fir or larch are easy to machine and suitable for glueing to a subdeck.
They meet nearly all of the three golden rules, and age to a lovely even-weather grey colour, much like untreated teak.
Both are also soft underfoot for those barefoot sailors among us.
But they do have one disadvantage: neither last as well as teak, with maybe a 10- to 15-year lifespan depending on how well the wood has been cared for.
Keeping boat wood healthy
On a well-kept and regularly sailed vessel, it’s unusual to find fungal issues on deck timbers and fittings – a regular dousing of salt water tends to keep this problem at bay.
Deck fixtures, however, tend to suffer from wearing out or damage and occasionally UV-related issues.
The less saturated and inaccessible sections of our boats can play host to fungi; even wonderfully oiled teak and varnished mahogany can be no match for a lack of ventilation.
Mast foots, cockpit lockers, cabin soles and interior joinery all suffer.
Mostly it’s cost-effective to replace like for like.
Most vessels have been fitted out with hardwood-trimmed plywood panels bonded together and then bonded to the vessel.
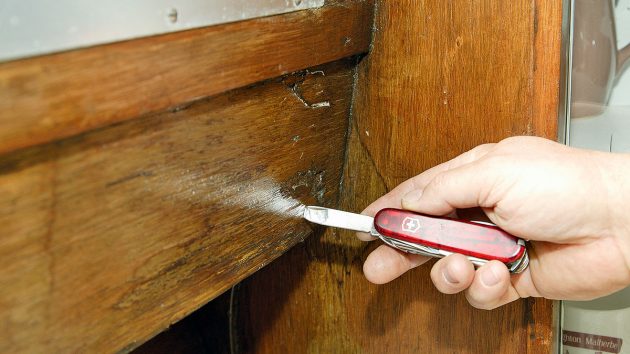
In areas of little ventilation, wood can rot. It is usually best to replace like for like
This is still a great approach, as plywood is simple to bond and use, as well as providing structural integrity, movement and durability.
It also means that huge amounts of extra internal weight are not being added down below; important for a well-balanced boat.
We shouldn’t just limit ourselves to painted white plywood with hardwood trim.
The replacement of interior joinery gives us a chance to amplify the space, and there are lots of kits and tutorials on how to add a veneer or carbon wrap to your plywood.
No matter how large or small the repair is, you should consider ventilation in the area where the wood is being replaced.
Look at coating the edges of the plywood and investing in marine-grade quality plywood.
Continues below…
Best boat varnish: 7 top options for gleaming woodwork
Few things are as quintessential to the archetypal sailboat as gleaming, iridescent woodwork that is indicative of a recent coat…
Replacing a rotten companionway step
James Wood gets to grips with epoxy when repairing a rotten step support on Maximus's companionway
Teak alternatives: How to make your decks look as good as the real thing
However, according to a recent report by the Environment Investigation Agency, there are grave questions over the sustainability and sourcing…
How to build a boat: Essential guide to building your first kit boat
You don’t have to be a boatbuilder to learn how to build a boat, argue Roger Nadin and Polly Robinson.…
While replacing the interior joinery, it’s worth thinking about how to reinvigorate the cabin and cockpit sole.
Of course, there’s nothing wrong with using a faced plywood subsole, but there might be an opportunity here to add a much harder and better-wearing cabin sole that is more appropriate for the rigours of life at sea.
Soles are often thinly veneered and satin vanished, which never seem to last past the first week of the season.
A more solid solution is beaded-edged Douglas fir or larch, which can look wonderful down below.
They can also be laid over a subfloor in your desired thickness and if you need it watertight, the beaded edge can be swapped for a caulked edge.
Allowing this to grey and develop a more natural look will not only reduce your maintenance but give you a harder-wearing, practical finish.
If you do end up dropping a bottle of red wine all can be fixed with some sandpaper and the process of time.
Best wood for masts
There is a section of the vessel often overlooked. We winterise our engines, boat covers go on and the cushions come ashore, then we think about our mast; ashore in the shed or utilised as a ridge pole, then stuck in the mast step or tabernacle for the rest of the season.
Owners of aluminium mast can fear not, but for anyone sporting a shiny wooden one it’s hardly unsurprising we often find some softer spots around the ends.
There is a lot to be said for the proper coating of spars but what do you do if your gaff, boom, or bowsprit is beyond repair?
Mostly our spars are made from softwood; on very unusual occasions, you might find a hardwood bumkin or bowsprit, but these are unusual.
When selecting timber for spars, the durability and structural integrity of the wood must be considered, but the most important factor is movement.
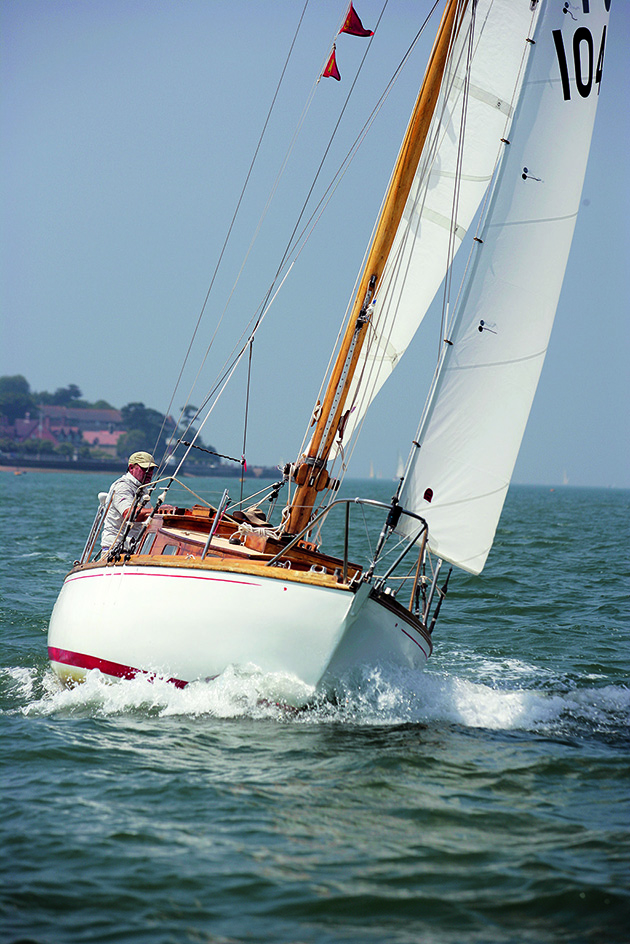
Wooden masts are generally made from softwoods, like larch, Douglas fir or sitka spruce. Credit Graham Snook/YM
Main masts, bowsprits and bumkins tend to require less twist and flex than gaffs, booms or the extremely endangered wooden spinnaker poles.
While I have seen smaller dinghies sporting oak, iroko and even ash for these spars, they’re not recommended unless you have a particular vessel requirement.
Larch is often used in larger working craft for these spars and if constructing a solid spar, this might actually turn out to be a good choice for a new home-crafted main mast.
As the availability of sitka spruce has dwindled and is now only available through very specialist suppliers such as Robbins Timber or Stones Boatyard, a discerning mast builder should look at Douglas fir, which gives movement, structural integrity and durability.
This solid wood is excellent for glued construction and is also easy to work with – important if this is your first foray into wooden mast building.
There is some lovely slow-grown, tight-grained timber on the market currently and it can be sourced in the UK.
Boat wood for strong steering
Fortunately or not, many boat owners will only have to varnish and care for their wooden tiller.
Again, there are plenty of options, but it is worth thinking about what you require – durability, integrity and movement – and also think about the aesthetics.
Iroko and oak are strong and durable and can stand the weather uncoated, whereas Douglas fir or mahogany tillers will need coating.

Ash is the preferred choice for a tiller – like on this Hallberg-Rassy 29 – as it’s strong and not too heavy
Unless you manage to find a grown shape in oak, all of the above will require laminating so the tiller doesn’t have lots of short grain which results in a weak construction.
Traditionally, tillers were always made of ash; this is a wonderful timber that is very strong but not too heavy, ideal for balancing transom-hung rudders.
However, ash is not readily available.
Whatever wood you use to build your tiller, it is a good idea to make a spare to store down below in case of an emergency.
Build solid
Timber selection isn’t just important for repairs and replacement, it also has huge implications for the construction of new wooden vessels.
As traditionally used timbers, such as grown oak and elm, have all but disappeared from the market, many traditional boatbuilders are now having to think far outside the box.
Centrelines were traditionally built in oak, but now iroko, opepe and even purple heart are all being used in its place.
These woods have proven longevity, having been used during the early restorations of classic boats which are still sailing regularly today.
For sawn and steamed timbers, oak is still the most popular.
Some builders are using the laminate construction of iroko or mahogany for building larger craft, but this tends to be for ring frame constructions and combines the deck beam into this process.
Carbon compatible
Companies such as Spirit Yachts have really pushed this a step further by combining carbon fibre alongside this timber construction; a great way to add strength to a boat.
Transoms, coamings and other brightwork still, for the time being, carry the trends seen over the centuries, with mahogany or teak being favoured, but this could change as the availability of timber changes.
Possibly, we will see more of a workboat look coming in, with these surfaces becoming painted and less exotic, but still durable.
The biggest challenge facing the modern boatbuilder is sourcing good quality timber for hull planking.
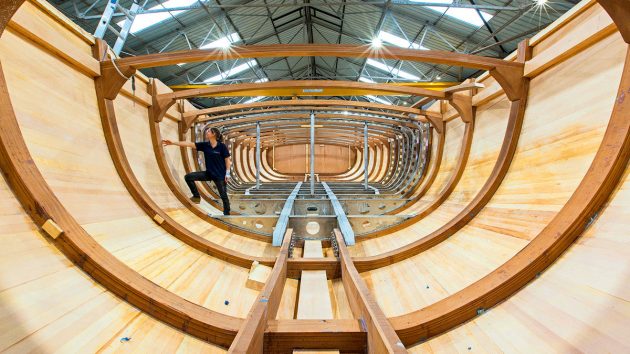
The centreline of the Spirit 111 was made using Douglas fir; a stainless steel space frame on the middle ring frames adds stiffness. Credit: Mike Bowden/Spirit Yachts
The wood needs to provide the length needed, without forcing lots of unnecessary scarfing planks and has to allow steaming and the twist of tricky underwater profiles.
The traditional boat scene soldiers on with oak and larch in this regard, and the vessels built at Working Sail in Cornwall show what can be achieved.
Other builders are using alternatives though.
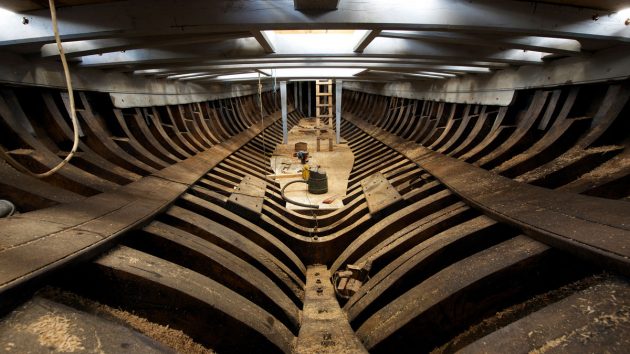
The Falmouth Pilot Cutter, Pellew, built by Working Sail, has oak frames and planking. Credit: James Stewart
Dan and Barry Tester rebuilt smack hulls from iroko, while Gerard Swift used Khaya mahogany to plank his skiff Mersea Native in 2000, which is still sailing today. If you can source larch, it’s a good middle ground between all of these options.
The reality of timber availability will soon catch up with us all, eventually limiting the options for amateurs and professionals alike.
In the meantime, however, if you remember the three golden rules and select a timber suited to your needs and requirements, you shouldn’t go too far wrong.
The best boat wood for the job
Centreline timbers
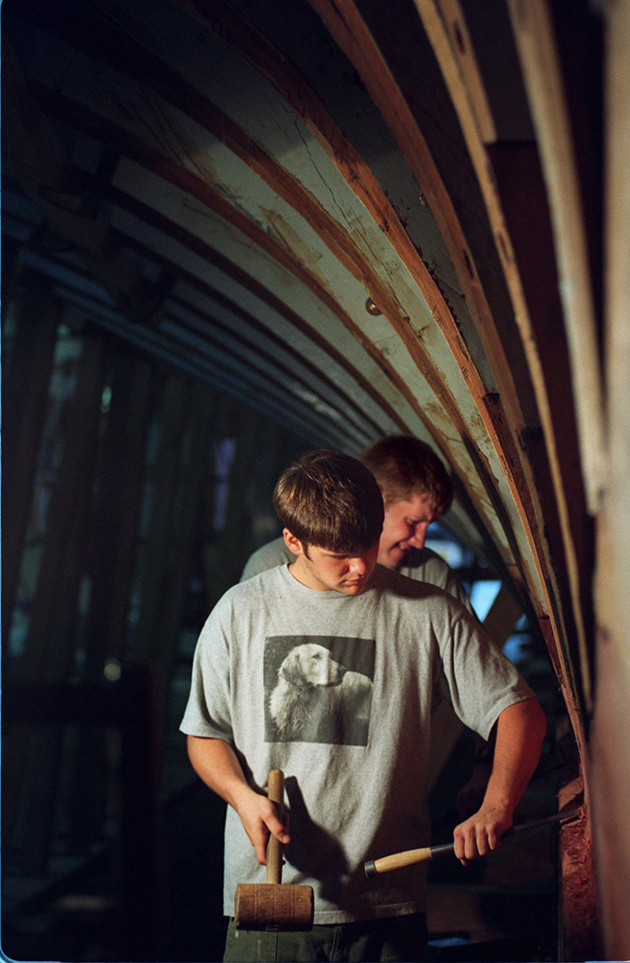
Purpleheart is durable, water-resistant and reacts well with changes in humidity, making it ideal for use in the centreline of a boat. Credit: Getty
The centreline of a vessel requires a timber that’s strong, durable and long lasting.
Oak
- Pros: strong traditional choice, often allowing the option of grown pieces with stem construction.
- Cons: lengths of long, clear timber are hard to find. Green timber is prone to movement as it seasons. Expensive.
Iroko
- Pros: stable timber available in long lengths, often able to provide wide boards which is important when looking at constructing hogs. Represents relative value for money. Works well for lamination when creating curved stems or stern posts.
- Cons: often hit and miss in terms of quality.
Opepe
- Pros: stable timber available in long lengths. Reasonably priced, heavy timber.
- Cons: can check heavily in sunshine; if working outside keep it covered or apply a priming coat. Can occasionally reject coatings and sealants, so it is worth researching which coatings are successful.
Purpleheart
- Pros: durable, insect and water-resistant. Purpleheart also reacts well to constant temperature and humidity changes.
- Cons: harder timber can be unkind to tools and tricky to work with.
Douglas fir
- Pros: long lengths of large, clear timber available, can provide great options when looking for sustainable-sourced timber. Much kinder on tools.
- Cons: not as durable as hardwood for a keel but not a bad choice for internal keelsons and deadwoods.
Transoms

Most woods used for transoms – such as surian on this Balmain Bug, will need plenty of coats of varnish. Credit: Crosbie Lorimer
For those of us sporting neat canoe sterns or long sweeping counters, this isn’t much of a concern, but for others, transom timber choice is vital.
It’s also often required to take a coat or nine of varnish.
Teak
- Pros: beautiful varnished finish. Responds well to steaming and lamination. Long lasting and rot resistant.
- Cons: expensive and scarce.
Iroko
- Pros: nice varnished finish. Responds well to steaming and lamination. Long lasting, wide-boards available.
- Cons: hit and miss in terms of quality. Often hard to purchase large quantities of colour matched boards.
Mahogany
- Pros: beautiful varnished finish. Responds well to steaming and lamination. Colour matched boards available.
- Cons: needs to be well cared for to ensure longevity.
Hardwood veneers
- Pros: various options for varnished finishes. Wide. Used with glues and hidden fastenings, it can provide stunning results.
- Cons: can be tricky to work with as easily damaged and requires thoughtful preparation before and during coatings. Needs to be placed on strong foundations.
Floors and frames
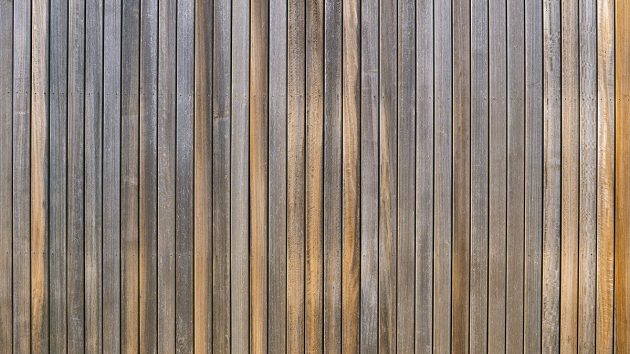
Iroko is ideal for lamination. Credit: Getty
An important structural element of any vessel, while many modern alternatives of carbon and laminate exist, the more traditional choices are limited.
It’s important to think about short grain when looking for curved pieces.
Oak
- Pros: the only single piece timber if you require any shape. Strong and reliable.
- Cons: expensive. Grown pieces are becoming harder to find.
Iroko
- Pros: strong, good for lamination and steams well.
- Cons: grain short for curves.
Opepe
- Pros: strong, good for lamination and steams well.
- Cons: grain short for curves.
Planking
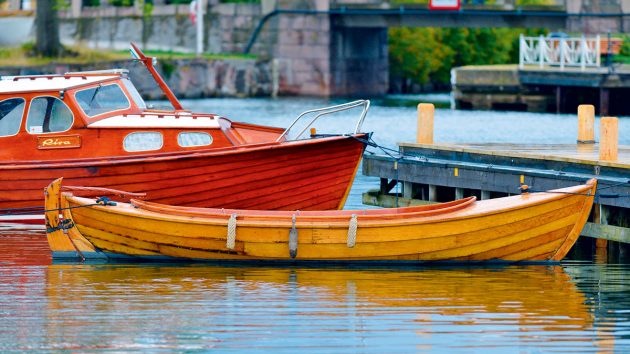
Oak bends and steams well, making it ideal for planking, although it is expensive to buy. Credit: Ilkka Ranta/Alamy Stock Photo
Choosing a suitable planking material is as important as it helps to determine the overall weight and strength of the vessel.
Consider what you want the planks to do: Are there tight curves? Lots of wear? Or is it all about grams of weight and dry sailing?
Larch
- Pros: a traditionalist’s choice when paired with oak. Available in long lengths. Strong and long lasting. Steams and bends well.
- Cons: wider boards becoming trickier to find. Beware of knots and sap and imitation pines.
Iroko
- Pros: fantastic strong choice. Can be vanished as a topside finish. Steams and bends well. Wider boards available. Thicker boards can be cut to provide split planks and colour match for a varnished finish.
- Cons: prone to cracking or splitting when fitting or fixing. Check for rot and sap when purchasing wider boards.
Opepe
- Pros: wonderful strong timber. Durable and rot resistant.
- Cons: limited on width of boards. Doesn’t bend or steam particularly easily, but can be done. Prone to checking and cracking under UV, even through coatings.
Greenheart
- Pros: strong and hard wearing. Steams well.
- Cons: can suffer becoming wet and dry, so needs one constant state – better being used below the water line. Hard to find outside of reclaimed stock.
Oak
- Pros: strong timber. Bends and steams well.
- Cons: can react to fastenings, and suffer UV damage.
Spruce
- Pros: lightweight and easy to work with.
- Cons: lightweight timber, expensive and doesn’t last as long as other choices of timber.
Elm
- Pros: bends and steams well, making it perfect for awkward shapes.
- Cons: expensive. Difficult to source wide and long boards. Prefers to be in a constant state of temperature and humidity, so it is better used below the waterline.
Mahogany
- Pros: varnishes well for topside finish. Bends and stems well. Doesn’t react with fastenings.
- Cons: doesn’t always have the longevity of other timber. Doesn’t stand up well to freshwater damage.
Decking
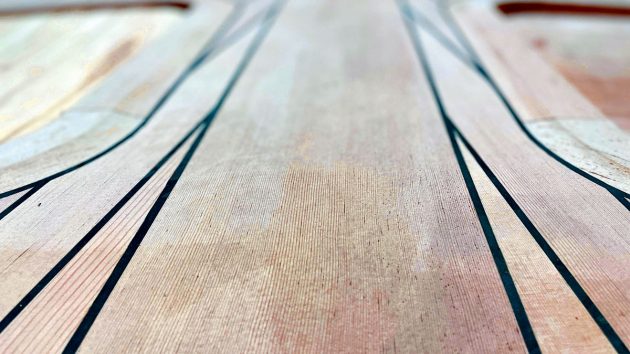
Boatbuilders, like Spirit Yachts, are now using Douglas fir for decking. Credit: Jessie Rogers
When choosing wood for decking, think not only about strength and waterproofing, but the overall looks and aesthetics it’ll bring.
Teak
- Pros: wonderful traditional choice that both weathers well and lasts. Works well over a subdeck. Solid planks.
- Cons: don’t over-scrub and wash with a brush. Expensive and harder to find.
Iroko
- Pros: great alternative to teak. Works well over a subdeck. Solid planks. Wide boards are available.
- Cons: doesn’t last as long as teak. Not as soft under barefoot. When machining large amounts and creating dust, it is highly toxic.
Douglas fir
- Pros: cheaper alternative to hardwood. Weathers to a beautiful silver. Lays well over a subfloor and solid planks.
- Cons: soft and can be easily damaged.
Rubbing strakes and toe rails
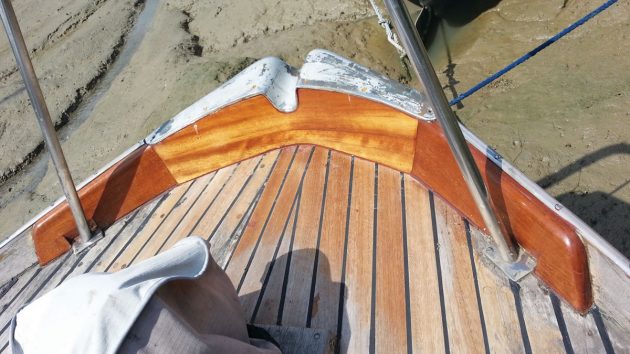
Hardwood, like teak, is best for toe rails. Credit: Mike Taylor
This is a high impact area, rarely varnished and undercoated. If you can, look for a hardwood option here.
Teak
- Pros: hard wearing and weathers well. Rot resistant.
- Cons: expensive, hard to find.
Iroko
- Pros: great alternative to teak. Wide boards available which is handy for tall toe rails.
- Cons: can be tricky to steam small section round bends. Highly toxic.
Mahogany
- Pros: varnishes well for topside finish. Bends and stems well. Doesn’t react with fastenings. Ages wonderfully under varnish layers.
- Cons: doesn’t stand up well to freshwater damage.
Oak
- Pros: strong timber. Bends and steams well. Looks better when scaled up in large sizes.
- Cons: can react to fastenings, and can suffer UV damage. Expensive choice. Can reject vanishes and expoxies.
Douglas fir
- Pros: cheaper alternative to hardwood. Weathers to a beautiful silver colour.
- Cons: soft and easily damaged. Can soak up the varnish coats.
Cockpit gratings
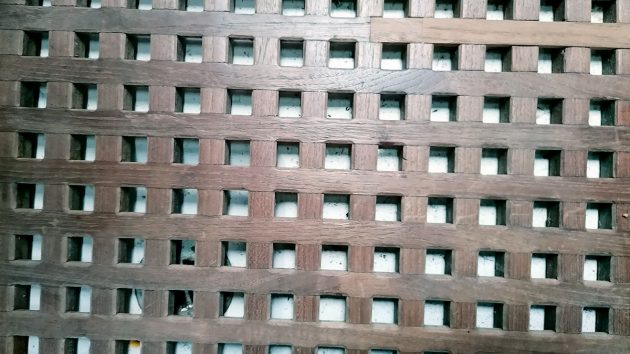
Teak is highly rot resistant, making it ideal for a cockpit grate. Credit: Katy Stickland
Teak
- Pros: hard wearing, and weathers well. Highly rot resistant.
- Cons: expensive, hard to find.
Iroko
- Pros: great alternative to teak.
- Cons: doesn’t last as long as teak. Not as soft under barefoot. Toxic when machining large amounts.
Tiller
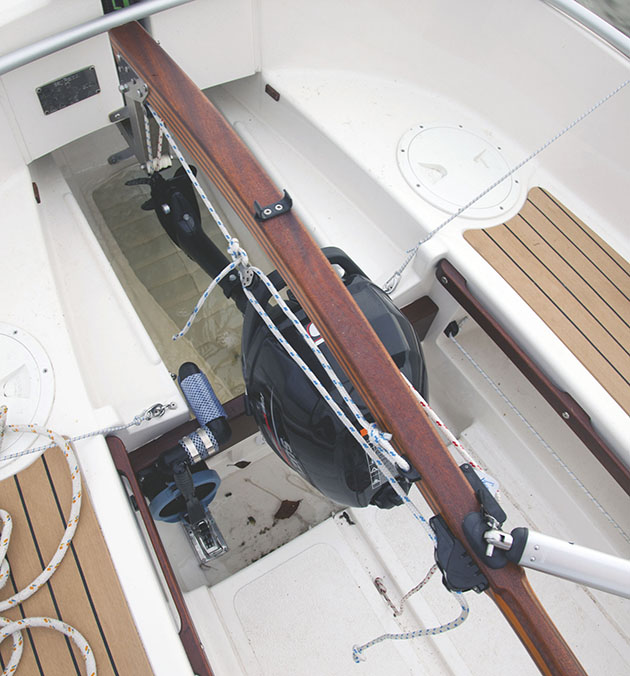
Douglas fir is lightweight. Here, it has been mixed with utile on the tiller of this BayRaider Expedition to give it added strength and to accommodate the curve over the head of the outboard engine. Credit: David Harding
Ash
- Pros: strong, curved pieces available to avoid short grain.
- Cons: goes black when uncoated. Not very rot resistant. Reacts to fastenings.
Iroko
- Pros: strong timber. Laminates and steams well.
- Cons: short grain for curved areas
Oak
- Pros: strong. Grown pieces so good for curves.
- Cons: costly. Avoid green wood.
Douglas fir
- Pros: lightweight timber. Laminates and steams well.
- Cons: Goes black when uncoated. Not very rot resistant.
Enjoyed reading Boat wood: a complete guide for yacht owners? 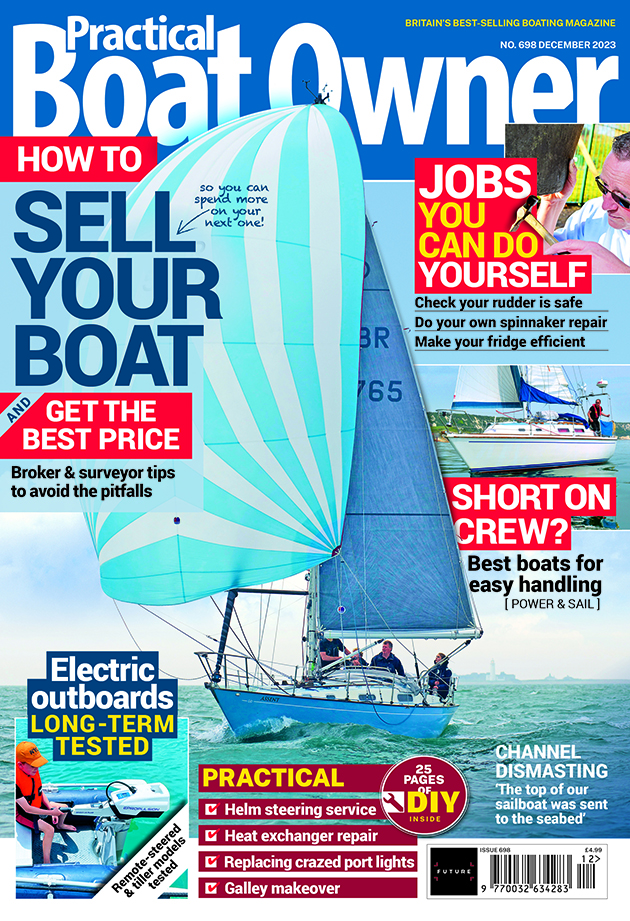
A subscription to Practical Boat Owner magazine costs around 40% less than the cover price.
Print and digital editions are available through Magazines Direct – where you can also find the latest deals.
PBO is packed with information to help you get the most from boat ownership – whether sail or power.
-
-
-
- Take your DIY skills to the next level with trusted advice on boat maintenance and repairs
- Impartial in-depth gear reviews
- Practical cruising tips for making the most of your time afloat
-
-