Genevieve Leaper and Aleko Stephan remove the old teak deck on their Nicholson 32 and renovate the original GRP with a new coating
Attractive to look at and a nice feel underfoot, a teak deck is a lovely thing. But even a well-made and well-cared-for deck won’t last forever.
Repairs and re-caulking may extend its life but eventually, the only choices are to remove the teak or replace it.
Aleko had already decided that Beduin’s teak deck must go.
Beduin is a Nicholson 32 built in 1964 which he’s been sailing for nearly 40 years. Aleko fitted the teak deck himself about 20 years ago, and it has weathered many years of Mediterranean sun plus a voyage to South America.
Unfortunately, the polyurethane caulking has been breaking up, letting water in under the teak which causes it to swell and buckle up.
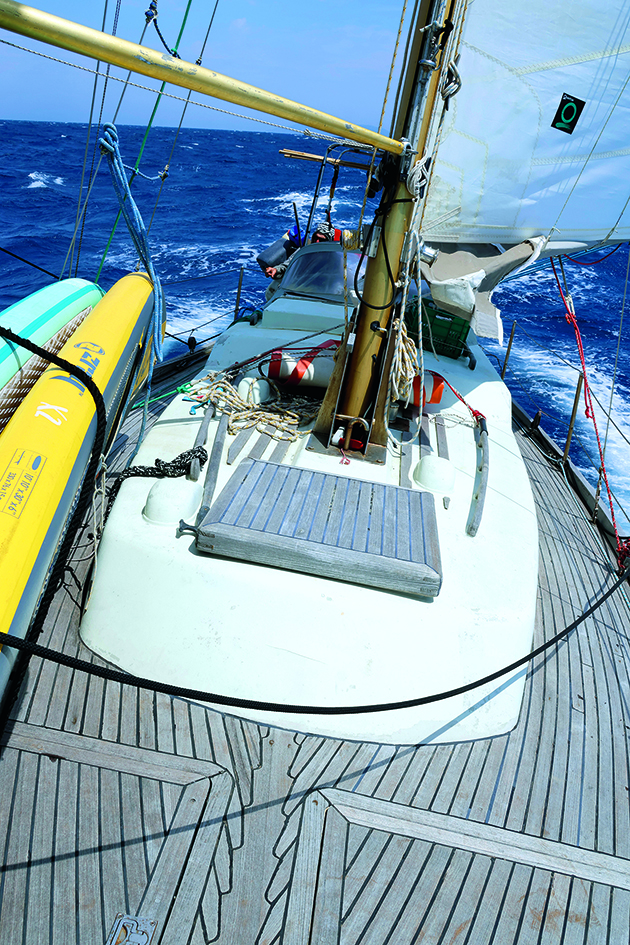
The teak decks on the Nicholson 32, Beduin lasted 20 years before leaks began
The water then finds its way through old screw holes (from an earlier deck) where the polyester filler has come out.
In other words, the deck was leaking; naturally in the most inconvenient places – through the foredeck, shorting out the windlass electrics and from the side deck into the galley lockers.
A short-term fix was no longer working, and the leaks were inaccessible under the planking.
Why we went for SoftSand coating
Coincidentally, Aleko’s friend, Sokratis, needed to replace a teak deck on his Najad 320, Peran.
The Najad is a newer boat and, unlike the Nicholson 32, was built with a teak deck. Sokratis’s problem was not leaks but that the teak had worn away.
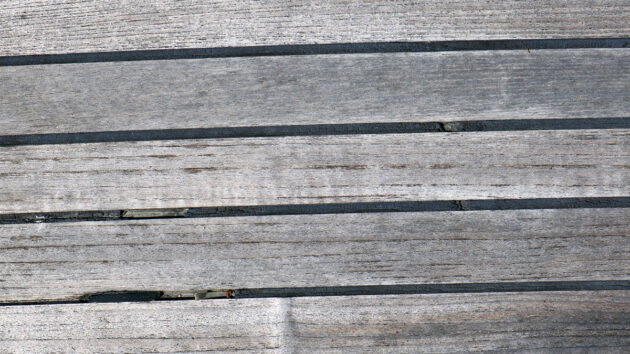
Water ingress through caulking led to the teak swelling and buckling
Having agreed to supply and cut the teak for Peran, Aleko briefly considered replacing Beduin’s teak deck while they could work on the two boats together.
But it would still be quicker and easier to return to a GRP deck painted with SoftSand coating, just retaining the teak planking in the cockpit.
Two boats, different problems and different solutions, but both benefited by working together -– sharing expertise and tools (and the odd beer at the end of the day!), buying epoxy in bulk and an extra pair of hands for some jobs.
I didn’t expect to be much involved, beyond watching the experts at work, but it turned out there were plenty of jobs for the unskilled labour; sanding, masking, painting and, of course, cleaning up.
Both skippers have plenty of practical experience.
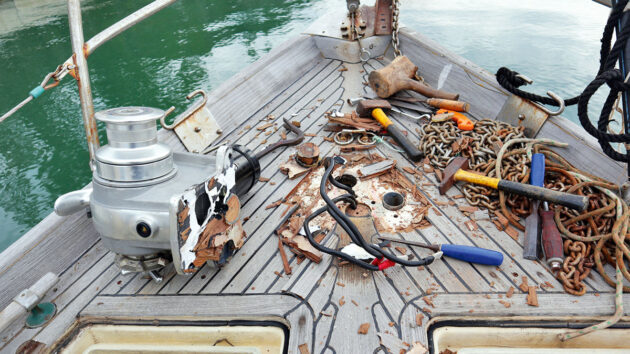
All of the deck gear needed to be removed, including the windlass
Aleko has fitted teak decks on several boats as well as his own. The work was carried out with the boats afloat in Milina harbour in the Aegean, saving the cost of lifting them out at the boatyard.
In the UK, such a project would be unrealistic with the boat uncovered and, even in Greece, spring was the only time to do it, winter being too wet and summer too hot.
Aleko started work on Beduin in the middle of March so we wouldn’t lose too many weeks of cruising time. Peran arrived from Athens about three weeks later.
Removing the old deck
First, everything attached to the deck had to come off, including the windlass, sheet tracks, mooring cleats and spinnaker sheet pulleys.
In Beduin’s case, even the shrouds had to be detached, one at a time.
Accessing the bolts for the sheet tracks involved dismantling part of the galley and the instrument panel.
Working alone, Aleko undid the track bolts by wedging the mole-grips holding the nut with a screwdriver while turning the bolt on deck.
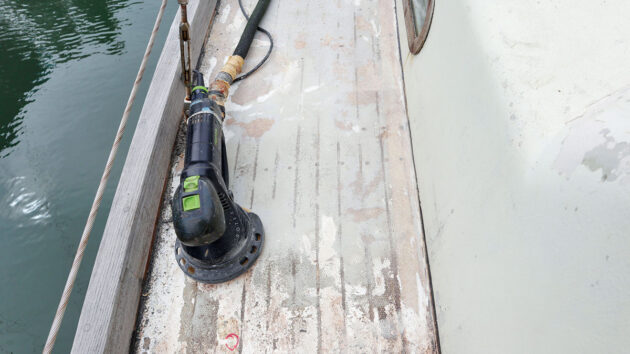
After removing the teak planks, the deck needed sanding
When it came to removing the deck, he started carefully, trying not to damage the planks, but while some came off easily, others planks were stuck down well and had to be broken.
It was hard work with a chisel and, of course, the first of many hours on his knees. Knee pads are pretty essential!
In places with heavy use, such as the foredeck, the teak planks had worn down from 12mm to 6mm, but around 60m was reclaimed, enough for the cockpit seats and some short planks on the other boat.
Preparing and glassing the exposed deck surface
The boat was built with aluminium reinforcing plates beneath sheet tracks and cleats. As aluminium swells, it corrodes and can break glassfibre.
Although the largest plates were removed 20 years ago, Aleko now found some small plates from the original mainsheet attachment and old foredeck cleats.
After removing these with the angle-grinder, there were about two days of work sanding the deck with P40-grade paper on a powerful eccentric sander.
Dust extraction on the sander is beneficial for environmental as well as health reasons.
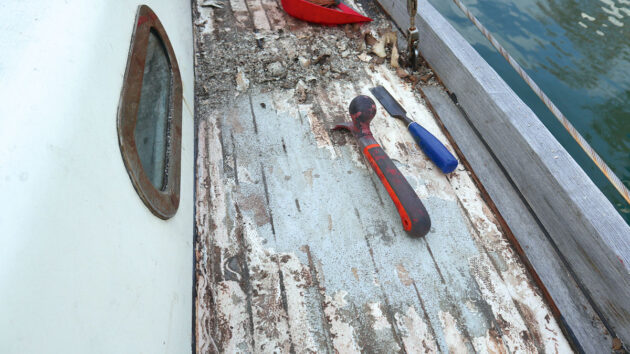
Scraping and sanding the deck was also hard on the knees
There was an awful lot of mess at all stages, and the most used power tool was probably the vacuum cleaner.
Next came the filling and fairing, using epoxy mixed with silica (cheaper than microballoons and strong, but harder to sand – so a mixture would be preferable).
The various holes in the deck for the water tank filler, track bolts etc. would be glassed over, so they needed to be marked for drilling again later.
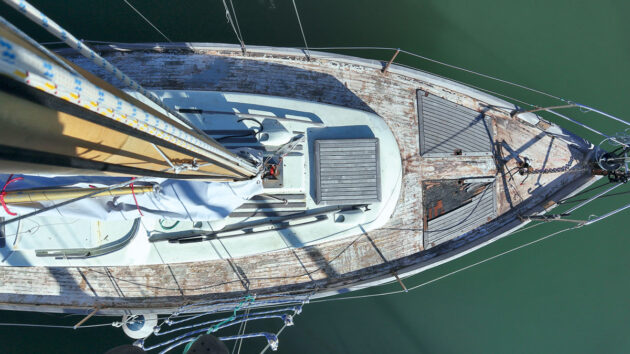
The deck after the removal of teak planks
A red marker pen shows clearly through the glassfibre.
For glassing the deck, Aleko was glad to have a friend to help, especially as Stepke has a pair of electric scissors for cutting the glass mat.
They set up a makeshift table on the quayside for cutting, working in approximately one-metre sections, slightly oversized for trimming later.
The routine was to roll on a layer of epoxy, lay the pre-cut 600gsm glass mat, wet it out and roll again.
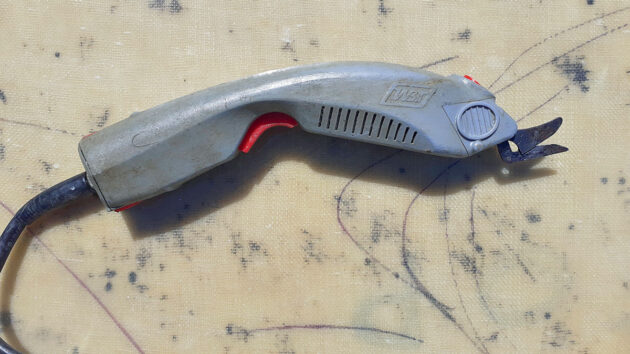
Electric scissors made short work of cutting glass mat
The next morning, Aleko went to check if the epoxy was dry enough to sand. Disaster! The foredeck had not cured at all.
Distracted by a friend coming by to chat while he was mixing that batch, he’d forgotten to add the hardener.
So the whole foredeck section had to be removed and cleaned off; a very messy job.
In any project, there always seems to be one part that takes a disproportionate amount of time.
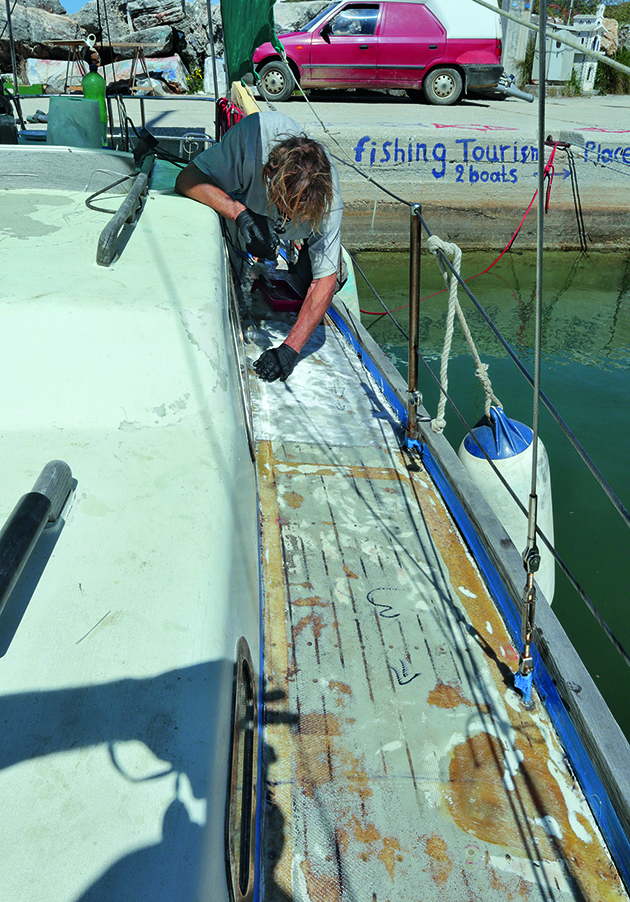
It’s important to ensure you mix the epoxy thoroughly ahead of laying the glass mat
On Beduin, it was the foredeck locker hatches, which had been fitted at the same time as the teak deck.
With the teak covering removed, the edges of the hatches had to be built up for a flush fit with the deck, as well as some filling on the upper surface and refitting of hinges and catches.
Preparation for SoftSand coating
I arrived in Greece in early April, just in time for the next round of sanding.
While we took out the worst lumps and roughness with the big sander it was not, the skipper informed me, a professional job.
It would have taken a lot more work to prepare for a new teak deck – which the boat was not designed for – as this requires a very smooth, flat surface with no undulations.
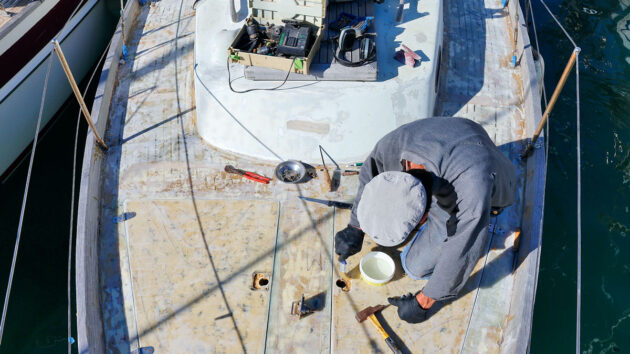
Refitting the foredeck locker catches before applying the SoftSand coating
The last step was drilling the bolt holes for tracks and cleats while the marks were still visible.
While we were painting the decks, it made sense to do the coachroof.
The sides were just fiddly, using a smaller sander around the windows, while the old non-slip on the cabin top was harder work and wore out a lot of sandpaper.
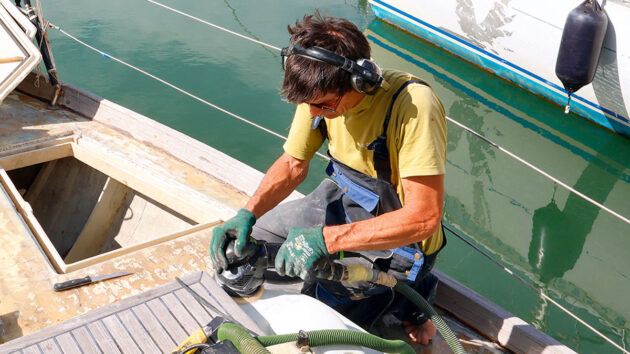
As well as replacing the deck, Aleko also sanded the coachroof – a long job
The cockpit was even worse – it had previously been painted with single-pack paint, so absolutely all the paint had to come off.
After sanding, all surfaces were thoroughly hoovered and cleaned with acetone, before masking off.
SoftSand coating
SoftSand is a non-slip additive of rubber particles which can be used with paint or epoxy.
We used epoxy as it is cheaper than paint, and we wanted to use medium-grain granules. It can be mixed in, but sprinkling over the wet surface is recommended as the best way to achieve a uniform texture.
The idea is to use plenty and then hoover up the excess once the paint or epoxy has dried.
This can be re-used so a domestic vacuum cleaner was cleaned out for the purpose.
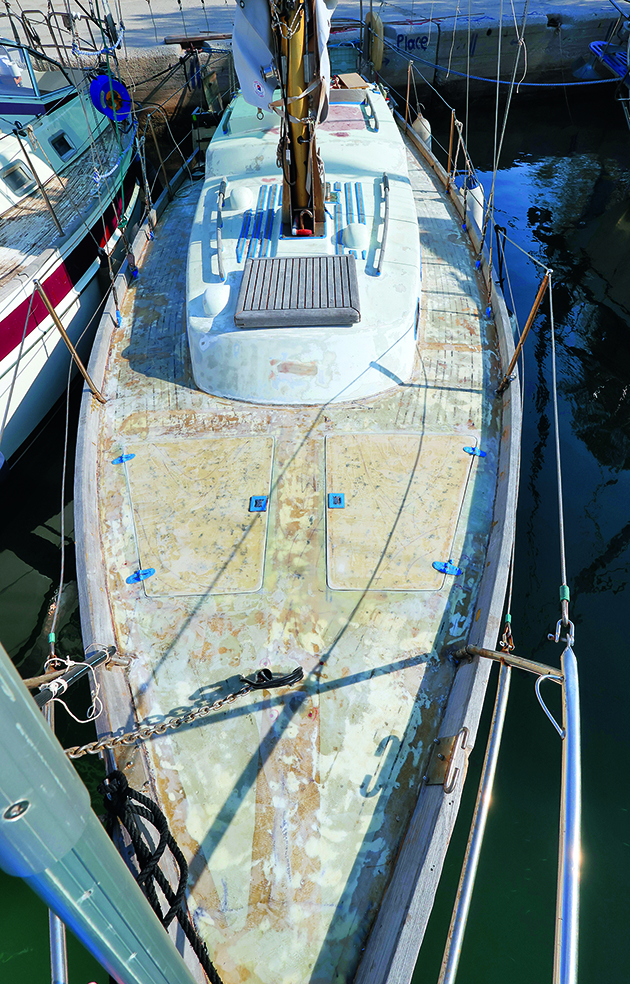
The deck ready for SoftSand coating
It was a hot day, and the epoxy was going off quite quickly, so we mixed only small batches.
The 4lt of SoftSand should have been more than enough (theoretical coverage of 16m2), but it was all gone by the time we stopped for lunch, and the main deck was still not finished.
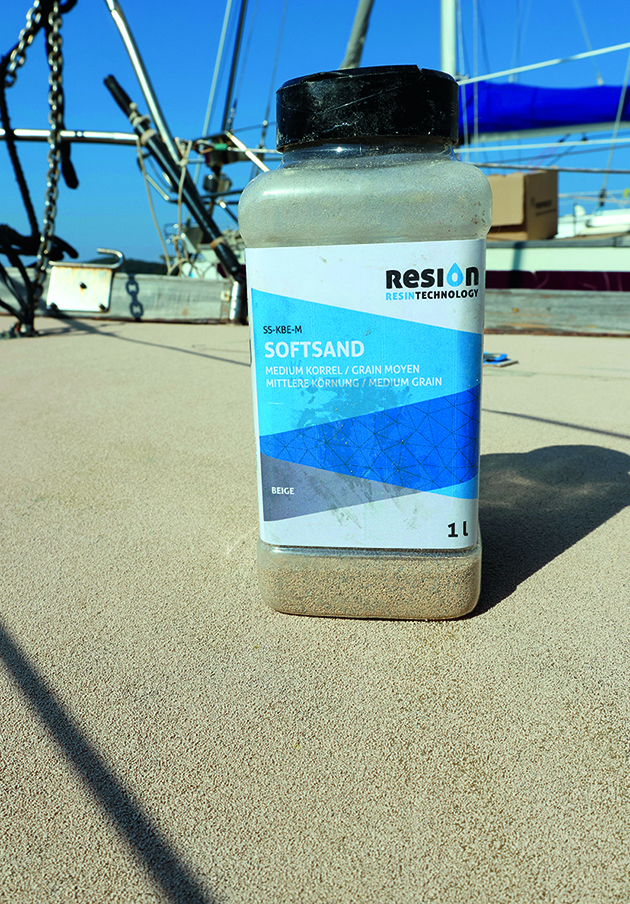
The SoftSand coating was easy to apply and worked well with epoxy, giving a decent finish
We did recover about 30% as expected but had to broadcast it very thinly over the cabin top, leaving out any non-essential areas.
We suspect that epoxy holds more of the particles than paint, resulting in a good thick coat, but perhaps one should allow for a larger quantity.
The other problem was only apparent on hoovering up the loose particles of SoftSand coating when a few bald patches were revealed.
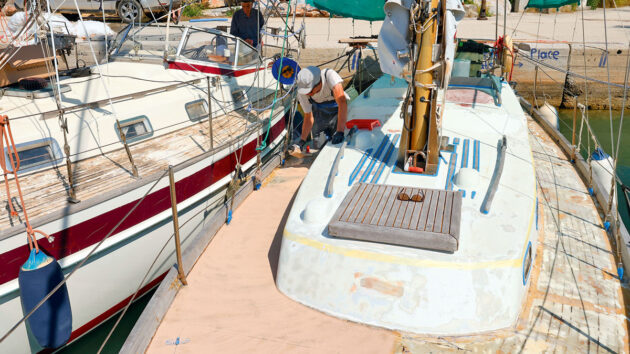
Epoxy soaked up more SoftSand coating than anticipated
Although we thought we’d been thorough with the epoxy, a few slight depressions must have been missed by the roller; this would have been easier to see with paint or a little colour in the epoxy.
It wasn’t difficult to patch up the bits of SoftSand coating we’d missed, but it does show.
Painting
There was the usual preparation; cleaning again and masking, before applying two coats of two-pack paint by roller.
Again, despite careful calculations and allowing extra time, we found ourselves running out of paint with not quite enough for two coats all over.
The SoftSand non-skid definitely takes a lot to cover. Also, even after all the hoovering, some grains come off on the roller.
We discovered the hard way not to use the same roller for the cabin sides.

Painting the SoftSand anti-skid. Beduin’s teak-free deck is now closer to original specification
In a hot climate, a light colour is desirable for the decks and it made practical and economic sense to use the same off-white paint all over.
But when we finished, I found the decks too white and we decided a different colour from the coachroof would look better.
Luckily, the wonderful village hardware shop lived up to its sign proclaiming ‘All Kind Store’ with a stock of marine paints.
A 1.5kg pot of cheaper paint in ‘sandstone’ solved our aesthetic problem with another coat on the deck.
Replacing fittings
Of course, all the fittings taken off the deck had to be replaced. The new deck had a lovely spacious look, it seemed almost a shame to clutter it up with toe-stubbing tracks and cleats!
Unfortunately, it wasn’t just a question of putting things back as they were.
With the thickness of the teak removed, the bolts for the sheet tracks were now too long to access with a socket spanner, so some had to be cut down.
The anchor windlass needed a new teak support plate.
One little mistake caused us a lot of trouble. We had temporarily taped over the bolt holes for the genoa sheet tracks, but the tape didn’t stick well on the SoftSand anti-skid.
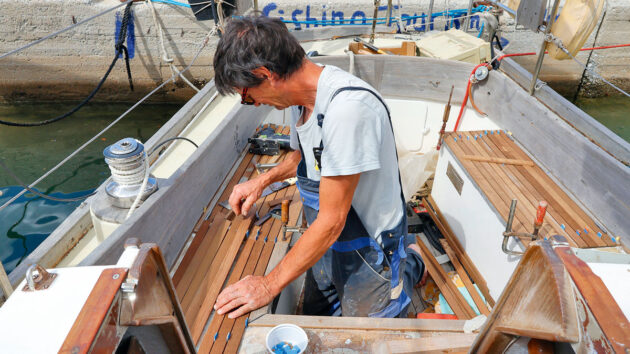
Using offcuts from the old deck, Aleko made new teak cockpit seats
Although heavy rain was forecast overnight, the skipper was confident no water would get in.
Unfortunately, although only one bolt hole leaked it was in the worst possible place.
The next morning, the chart table was awash, with all the boat papers, pilot books, charts and instruction manuals in a soggy lump.
I spent two grumpy days peeling papers apart and drying books page by page, trying not to make comments of the ‘I told you so’ variety, while the skipper continued with more technical operations.
We made sure to get the tracks back on – a two-person job – before the next rain, using plenty of sealant around the bolts.
Quite apart from that little mishap, it took several days of work to get everything back in place.
Cockpit seats
The one place we really wanted to keep the teak was the cockpit.
Only short lengths were required which could easily be salvaged from the old deck planks.
While Aleko was cutting teak for Sokratis, he ran the old planks through the workshop machines (planer, circular saw, band-saw), before cutting the lengths and fitting them back on the boat.
The corners by the cabin were not flat, so a mix of epoxy with microballoons filler was applied to level the surface.
To glue the planks, both surfaces were coated with a thick paste of epoxy plus microfibres, using a tiling spatula.
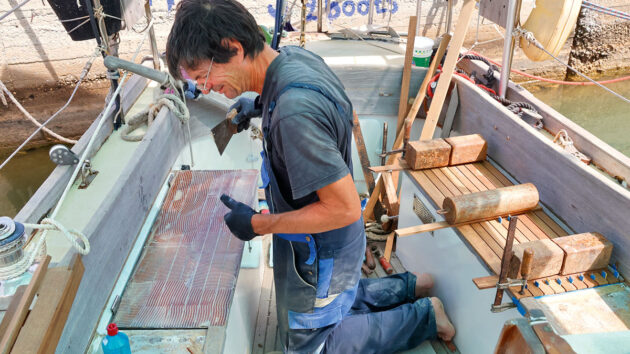
The planks were glued down using epoxy and microfibres before being weighted down
The planks were laid with spacers in between and weighed down until set.
You can’t have too many weights – as well as several 5kg iron weights, lead diving weights and bricks also came in handy.
After masking all the seams in the cockpit I have to confess I was glad we didn’t have a whole deck to do.
After one day of laying the planks, the caulking took another half day, and then, when that was cured (two days in Greece, more likely three in the UK) it could all be sanded.
From the appearance, you wouldn’t know the teak had already been on the deck for 20 years.
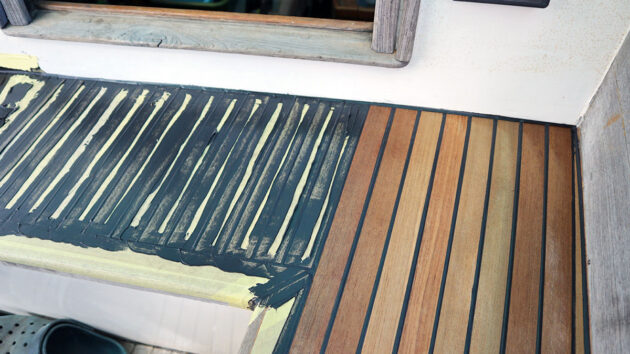
Caulking applied to the cockpit seats; it took two days to fully cure
There was to be no more polyurethane-based caulking, which had been the start of our deck problems.
Although supposed to be UV resistant, it does deteriorate in the Mediterranean climate, sometimes going sticky like tar in the sun, or brittle and crumbling.
Sokratis had chosen a silane polymer after some research, and Aleko was happy to use the same.
The teak forehatch was still in good condition, it just needed recaulking.
We’d already scraped out the old caulking so it could be done at the same time as the cockpit, along with sealing around the cockpit coaming.
With her low freeboard, Beduin takes a lot of water on deck, which tends to ooze under the coaming onto the cockpit seats.
A minor detail compared to leaking decks, but who wants a wet backside when otherwise comfortably dry under the sprayhood?
The finished result
After six weeks, the SoftSand deck was finished, and it was time for the skipper to tidy his tools away before a major clean-up.
Absolutely everything inside the cabin, as well as in the deck lockers, was covered with an unhealthy mix of epoxy and teak dust on top of the usual winter grime.
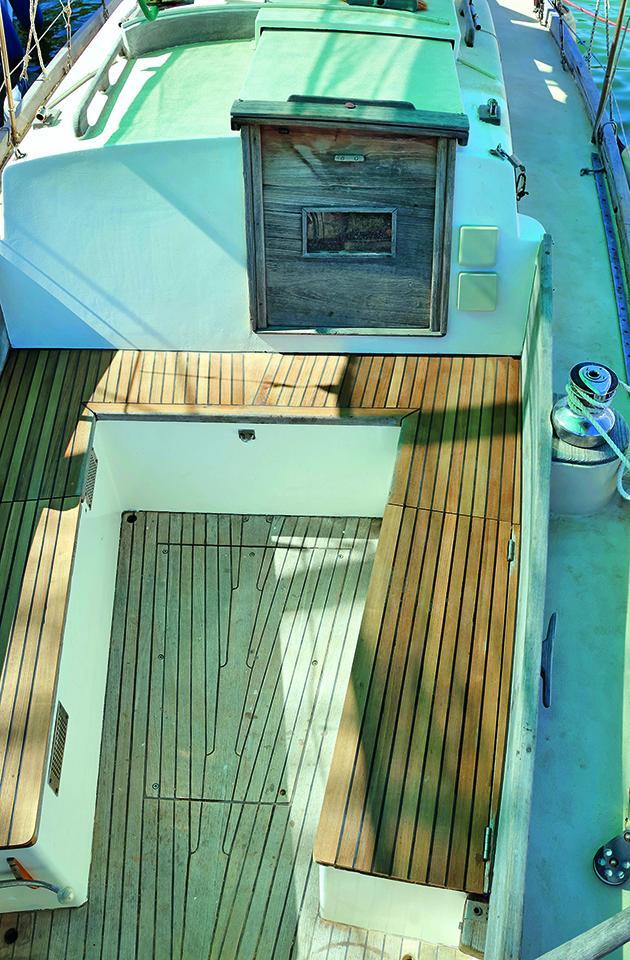
The finished cockpit seating
On deck, the recent rain coming from the south had also left a coating of orange Sahara dust on our new paintwork.
Finally, we were ready to go cruising and put the new deck to the test, leaving Sokratis to enjoy his planking.
While I loved the teak, we have very quickly got used to Beduin’s new look.
The SoftSand coating is effective non-slip and kind to bare feet.
It’s not quite so nice for kneeling or sitting on so I’m glad we kept the teak in the cockpit.
Best of all, we have a dry boat with no leaks. There is still the cockpit floor to be done, and she’ll have to come out of the water at some point for work on the hull – but now is for sailing.
What is the best way to stick down teak planking?
PBO reader Les Broughton is struggling to glue his teak planking to the fibreglass in his cockpit. Boat builder Lyndon…
How to re-caulk teak decks: Vagabond 47 owners explain how they did it
First, they removed the old caulking between the planks using a Bosch Palm Router and pinned a guide into the…
How to lay EVA foam decking on your boat
With the eye-watering cost of teak, Andy Pag decides to lay bargain EVA foam decking in the cockpit of his…
10 low-cost solutions for non-slip decks on boats
Anti-slip decks are vital for safe sailing, with a wide range of attractive, long-lived, and sustainable coverings available. Jake Kavanagh…
Want to read more practical articles like How to coat a GRP deck with SoftSand non-skid?
A subscription to Practical Boat Owner magazine costs around 40% less than the cover price.
Print and digital editions are available through Magazines Direct – where you can also find the latest deals.
PBO is packed with information to help you get the most from boat ownership – whether sail or power.
-
-
-
- Take your DIY skills to the next level with trusted advice on boat maintenance and repairs
- Impartial in-depth gear reviews
- Practical cruising tips for making the most of your time afloat
-
-
Follow us on Facebook, Instagram, TikTok and Twitter