Giles Fraser takes on the challenging but rewarding task of replacing the teak deck on his Swan 43 ketch Elisabeth with Flexiteek synthetic decking…
When we bought Elisabeth, our Nautor’s Swan 43ft ketch, in 2006 she was already nearly 30 years old. At the time we bought her the deck had just been repaired, sanded and oiled. It did not appear to be a problem as it looked beautiful.
The rest of the boat was immaculate, we were delighted with her and felt this was the boat for us. Elisabeth is a roomy family cruiser with classic Swan lines and a comfortable layout. A haul out to see her bottom, a perfect test sail around a couple of the Croatian Islands and we were asking where to sign.
The deck on Elisabeth is a feature of the boat; 22m2 of the finest Burmese teak running the full length of the boat. When it was in good repair the deck would turn heads. I have spent many evenings admiring it after a day spent tidying the teak up, touching up the caulking, sanding and replacing screws and plugs.
Article continues below…
How to restore teak decking: Varnish or oil? Ask the experts
“Can your paint expert help me identify the coating on my boat’s flybridge deck and stairs? “Is it likely to…
Teak alternatives: How to make your decks look as good as the real thing
However, according to a recent report by the Environment Investigation Agency, there are grave questions over the sustainability and sourcing…
Unfortunately the time spent admiring decreased over time, and the time spent on hands and knees trying not to tread in the sticky lines of caulking increased a lot.
The beginning of the end came when we sailed Elisabeth up from the Med to the UK in 2011. We spent a couple of years around the south-west coast of the UK. This proved to be a disaster for the deck.
The wet weather and lower temperatures started to attack the deck, causing the now ancient polysulfide adhesive to lose its grip and the caulking to break up and perish. I started to lose ground against the elements as I lifted parts of the deck and stuck it down again.
When we returned to the Med after a couple of years the damage was done, many places had worn thin and kept coming unstuck. The deck was obviously on its last legs so it was time to think about sorting the problem out properly.
Ice breaker
Teak decks are an eternal source of debate in the yachting world. If you are with a group of yachties and the conversation slows up a bit, just mention that you are thinking about doing something with your deck and that’s what you will be talking about all evening.
Most people, even with new boats, have some experience and certainly some opinions about teak decks. There is a lot to know about maintaining them.
Investing in a new deck does not really increase the value of the boat. Buyers expect a deck that is in good repair on a boat. If it is not, they will move on to the next one or offer less money.
(Rigging is the same, if it is over 10 years old it becomes a hindrance to the sale of a yacht but if it is new you cannot expect more money for the boat.)
With a deck in poor condition questions may then be asked about the state of the core material of the deck, as if the deck screw holes leak then the core may have degraded due to water leaking in, which is a nightmare job to repair. A new deck will, however, make a boat much easier to sell, as will anything that makes a craft look smarter, tidier and less work.
Deck options
I soon realised there were quite a number of replacement deck options, ranging from the most expensive solution of taking the boat to a top yard and replacing the deck with 15mm certified Burmese teak, to the cheapest – having no teak at all and just replacing the deck with non-slip paint.
Following preliminary enquiries, we shortlisted a few options. Top of the ‘real teak’ list was an Italian yard on the Amalfi coast. I had seen a 46ft Swan on a brokerage site with a brand-new deck. It was breathtaking.
The images had been taken before she had even been out of the shed and she had acres of pristine honey-coloured teak that would make any yacht owner cry with delight every time they looked at it. It was truly a work of art.
I contacted the yard through the broker and got a quote. Unfortunately, the quote would also bring tears to your eyes, being more than half the value of the boat!
There were a lot of yards that would do a very similar job to this around the Med and I spoke to a number of them, mainly in Majorca and mainland Spain.
I looked at lots of quotes and photos of superb decks. Certainly, if you had a big budget there were plenty of yards prepared to do a first-class job.
Real teak had a number of other options too. There was a team of men that did a lot of work in the marina we wintered in in Spain, their technique was to stick the teak strips to plywood which was cut in panels to suit the deck, then stick the panels to the deck.
This is quite a common way of doing it, but I didn’t really like the idea as the teak itself was quite thin. Also it was not a lot cheaper.
Another real teak option was to head east. I’d met a few people who spoke very highly of the yards in Turkey and their ability to do a good looking job, so I put out some feelers and soon got some quotes, one of which looked particularly attractive, despite the yard being quite a distance from Cartagena in Spain.
One of the issues with travelling to the east is that it would take most of the sailing season to get there, and the work would not start until the following spring as you need around three months perfect weather to lift and replace a teak deck the size of ours.
Price reality
None of these options were cheap. Quality teak wood is a very scarce and a very expensive commodity. I learned that there is a lot of timber lost between offcuts, machining and faults in the planks.
I also learned that not all ‘first quality Burmese teak’ is as described. The quality varies a great deal even to the point of not being teak at all. If quality timber is not used the deck can start to fall apart surprisingly quickly.
I saw a deck repair being done on a yacht that had only been completely re-decked only two years previously. There were knots in the timber which had cracked and started to let water in to the adhesive layer, requiring a timely repair.
I started to worry that the cheaper quotes might not be the good value they at first appeared. It is very difficult to check on previous jobs done when a yard is 2,000 miles away, and most of the work that they had done was sailing around the Med in a random way.
One yard proudly sent us photos of a job they had under way, unfortunately we could see some fairly damning faults in what they were showing us with uneven caulking gaps and some parts not symmetric. It would not fill you with confidence.
One very simple way of dealing with the deck falling apart was to remove it completely, clean up the surface and coat it with non-slip deck paint.
I have seen jobs where the non-slip was masked in areas with white detail in between which looked very good. In particular there was an Oyster ketch that we saw that had a very nice job done.
The cost was low, being only the preparation and the paint. The problem with that solution being the teak deck was a part of Elisabeth and without it she would not retain the classic look that was part of the reason we bought her. Julia, my wife, was particularly resistant to this solution so it was back to the drawing board.
The solution: Flexiteek
During the time that I’d been looking at different options for replacing the deck I was aware of the range of artificial teak decking materials that were on the market, and had looked at various samples, some of which looked pretty good and some of which did not.
I made some enquiries and got some quotes and could see that if a suitable material was available then the project could be completed at a reasonable cost. Unfortunately, most, if not all of the materials we saw looked a bit artificial.
Also, we’d seen enough shoddy jobs done in ‘fake’ teak to worry about getting a decent job don – I’d seen people doing it themselves and it was very tricky to get it put down right.
After a couple of years, we were really no further along having done a lot of research, spending hours on phone calls and internet searches.
Plying people with drink to elicit information was also starting to get expensive. A friend who is a trawler skipper once told me that the best way to sort out a problem on a boat is to throw money at it until it goes away.
It looked like we would have to bite the bullet and try and find lots more money, then follow this strategy. But sometimes answers to difficult problems just appear out of nowhere.
We were heading down to the ritual Sunday barbecue in Yacht Port Cartagena laden with Tupperware boxes and bottles of wine when we saw a big Lagoon Cat with a brand-new deck in a material called Flexiteek.
We stopped to appraise the job, by now considering ourselves experts on decking. We explained our situation to the owner, who invited us on board to have a closer look.
When I enquired what he thought of the job he said “I think it’s perfect, and I am very fussy. That’s a natural part of being German!”
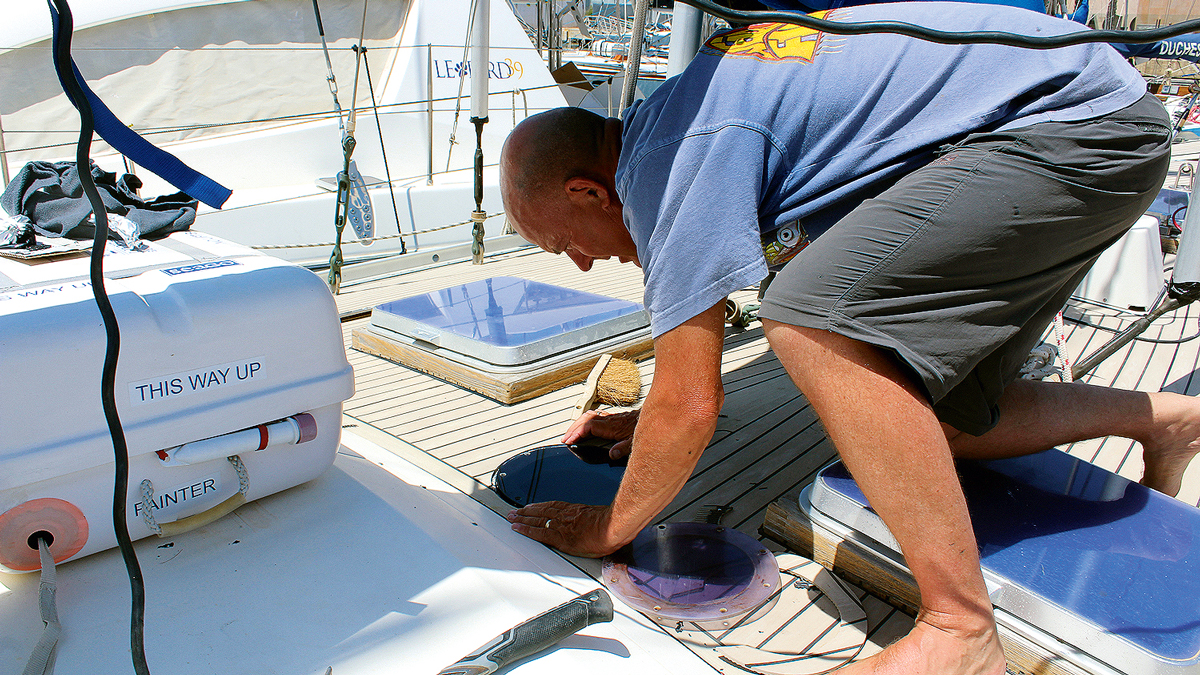
We had new Perspex for all the decklights. The holes were in the wrong place on this one hence the annoyed look.
Julia and I agreed that Flexiteek was the first artificial teak that we had seen where the colour looked natural and the fitting and finishing was perfect. We continued on to the barbecue with contact details in a back pocket and plenty of food for thought.
Phone calls were made and it turned out that the company, Yacht-Tek Ltd, had a base nearby in Torrevieja, as well as the UK.
We arranged for the company owner, Simon Clarke, to come and look at Elisabeth and give us some Flexiteek samples and information, plus some idea of what was involved, the job cost and the timescale.
We spent a full day with him going over the deck and all its fittings, taking photos and a lot of measurements. By the end of the day the plan for the Flexiteek project became clear, tasks were outlined, dates pencilled in and hands shaken.
After a couple of days a full quote was sent and we soon had an agreement. The work that had been outlined first required the deck to be templated, and patterns of the teak areas taken and sent to the workshop in the UK to be made up in panels.
The deck itself then had to be removed and the surface prepared for the new Flexiteek to be laid. When this was done the deck would be laid and caulked, with the larger sections heat-welded in situ.
DIY Flexiteek decking
We decided to remove the old deck ourselves. It sounds like it’s an easy enough job to take the deck off a yacht, but it is not. It is bloody hard work. Once you have started you can’t go back!
There are pitfalls, tricky bits, the odd nasty surprise and lots of work. We both have a good deal experience at this type of job so were aware of what we were letting ourselves in for.
First of all it has to be agreed which fittings are to stay in place, which needed removing (most of them!). Then you buy a set of knee pads, some wide chisels and some eye protection and get to work.
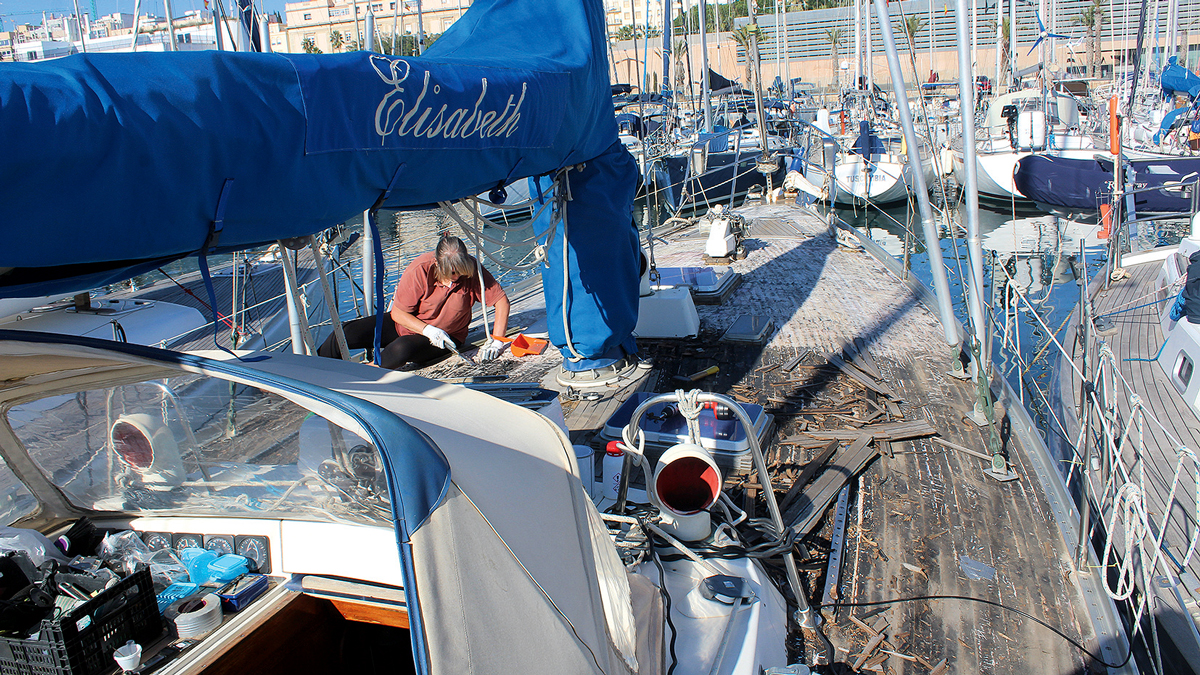
Julia working diligently to remove the old teak decking; some areas came away easily, others took time and patience to get off
We used chisels for the most part and a multitool to cut around the fittings that were staying. There is no easy or quick way.
Fittings that were taken up were methodically labelled and bagged, and hatches were masked to avoid damage.
Elisabeth was built in 1977, when they used plenty of adhesive and plenty of screws. That leaves a lot of scraping after the wood has been taken up to get the glue off. Then there are about 2,500 screws to be unscrewed and their holes filled with epoxy filler.
You need to have a bit of stamina for this work. It is demanding. We were flat out for six weeks. Some areas came really easily, but many parts were like brand new and took time and patience to get off.
When the filling has been done the whole deck has to be sanded and keyed in. At this stage it must be spotless, a perfect surface for the new adhesive is essential.
Simon left us in no doubt as to the finish he required. He would normally strip the deck himself because if the deck is not done correctly faults may appear in the deck later.
The templates are checked with the deck removed and sent to be compared with the new deck in the factory. When everything is done the decks are packed in the Flexiteek factory and sent to the boat, where they turned up a few days later.
As we had wangled an alongside berth it made it quite easy to organise the workspace, which needed minimum footfall as any contamination or small stones finding their way onto the deck cause problems.
Everything had to be laid flat and get a bit of sun to warm the Flexiteek. This ‘relaxes’ it and takes any distortion out.
The actual laying of Flexiteek is magic. Big sheets of decking are brought on board, trimmed and then rolled down on top of adhesive.
All of a sudden there is a perfect piece of deck where a few minutes before all you could see was grey and scratched gelcoat. Within a few days the bulk of the Flexiteek was down, but once the big bits are in place there are smaller and trickier bits to fit.
Finally all the caulking has to be done and hatches, deck-lights, blocks and fittings have to be refitted. It is a very skilled job to relocate the holes where the bolts for granny bars and suchlike had to go back.
The whole Flexiteek deck then gets a sanding to bring up the finish. I had decided to get the dull grey plates around the rigging chain-plates and the deck-lights remade in stainless steel, and this proved to be a great decision as they glinted in the sun and set the deck off really nicely.
Finally the day came where more tools started going back into the truck than out, the last bits of sanding were done, the last fittings found and screwed down and we all stood on the pontoon admiring the finished job.
The cost of the whole deck was 17,000 euros, all in. I cant really break that down as it was an all in quote for 22 square metres.
It was like we had bought a new boat. The new Flexiteek made an unbelievable difference, lifting the appearance of the boat, making her look enviably smart. It was a job that I would find myself staring at with a feeling of pride.
Our verdict on Flexiteek
Six months and 3,500 miles later the Flexiteek deck is as good as the day it was put down. I am very happy with it. Maintenance is easy, it is very much easier to wash, and the power washer is no longer out of bounds.
The old deck used to leach brown stains down the side of the boat which no longer happens. Because the deck surface is perfect, shoes that have been ashore leave footprints, but these are easily cleaned off.
Yes, Flexiteek does get hot in the sun, but then the teak did too, and unlike real teak red wine just wipes off without marking. Any reservations I had about artificial teak are now gone. Elisabeth looks extremely well and I think we chose the correct route.
I am pretty sure that this type of material will become standard on replacements and newbuilds, Leaving the teak trees back to the orangutans.
How to fit Flexiteek: Step-by-step guide
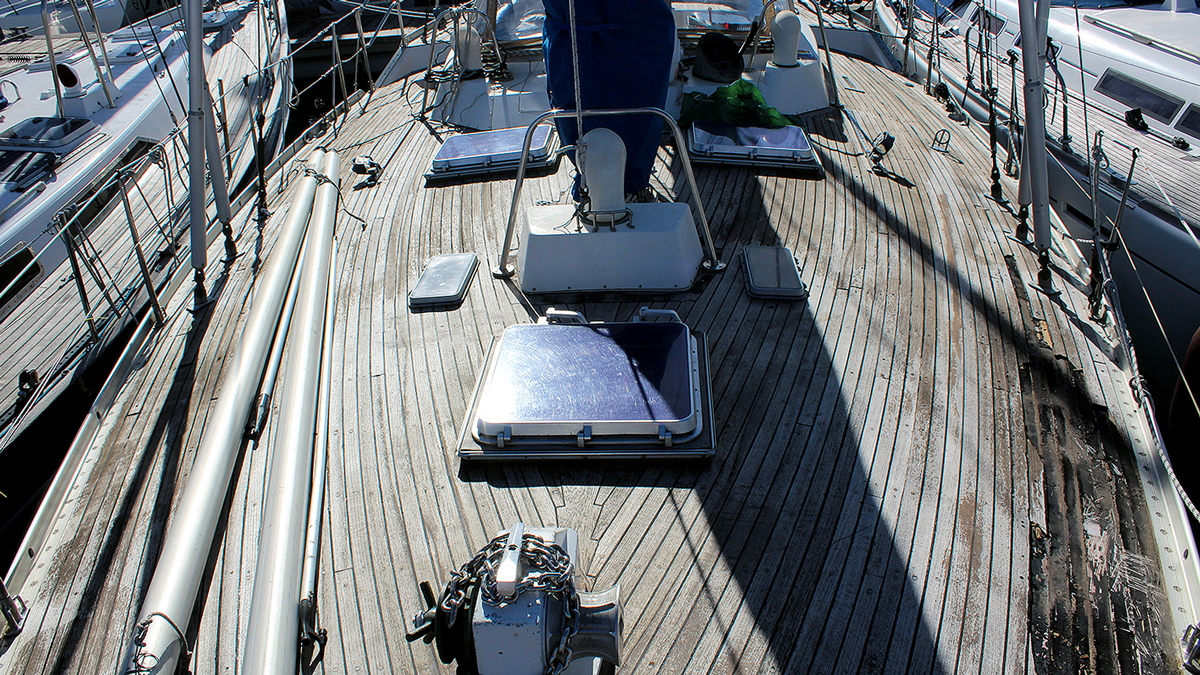
Elisabeth’s original teak decking on its last legs; after two years of wet British weather, the ancient polysulfide adhesive was losing its grip and the caulking was perishing and breaking up.
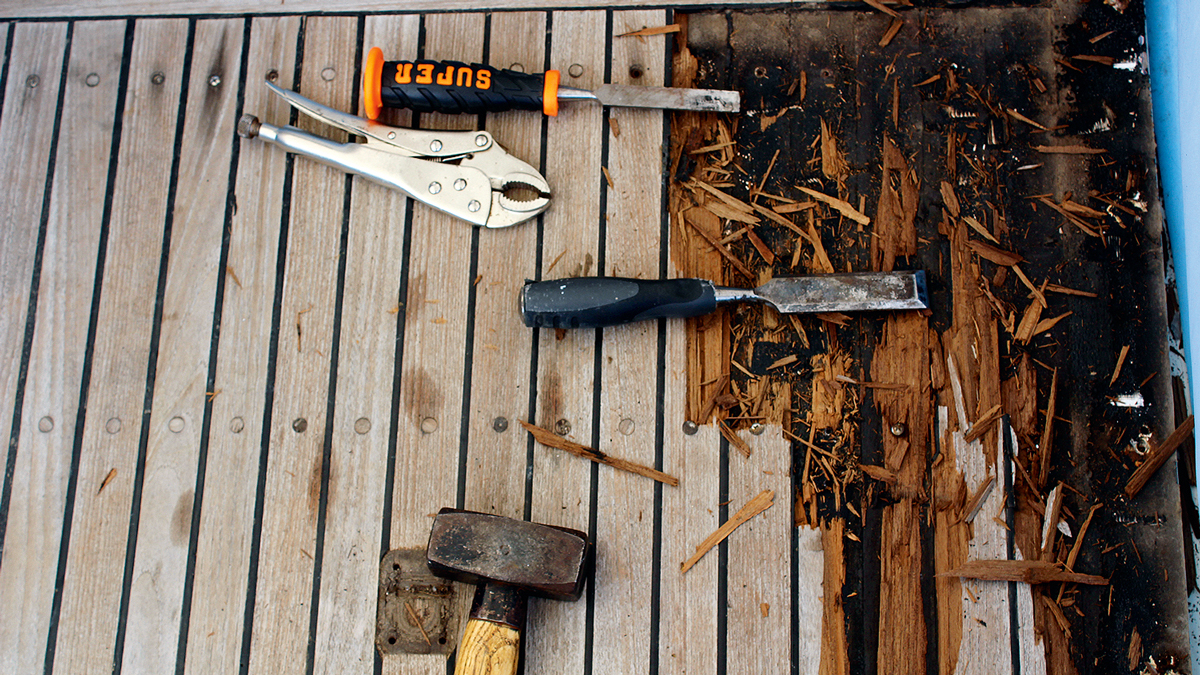
Removing the old deck is hard work. First, agree which fittings are to stay, most will need removing. We used chisels mostly and a multitool to cut around the fittings that were staying.
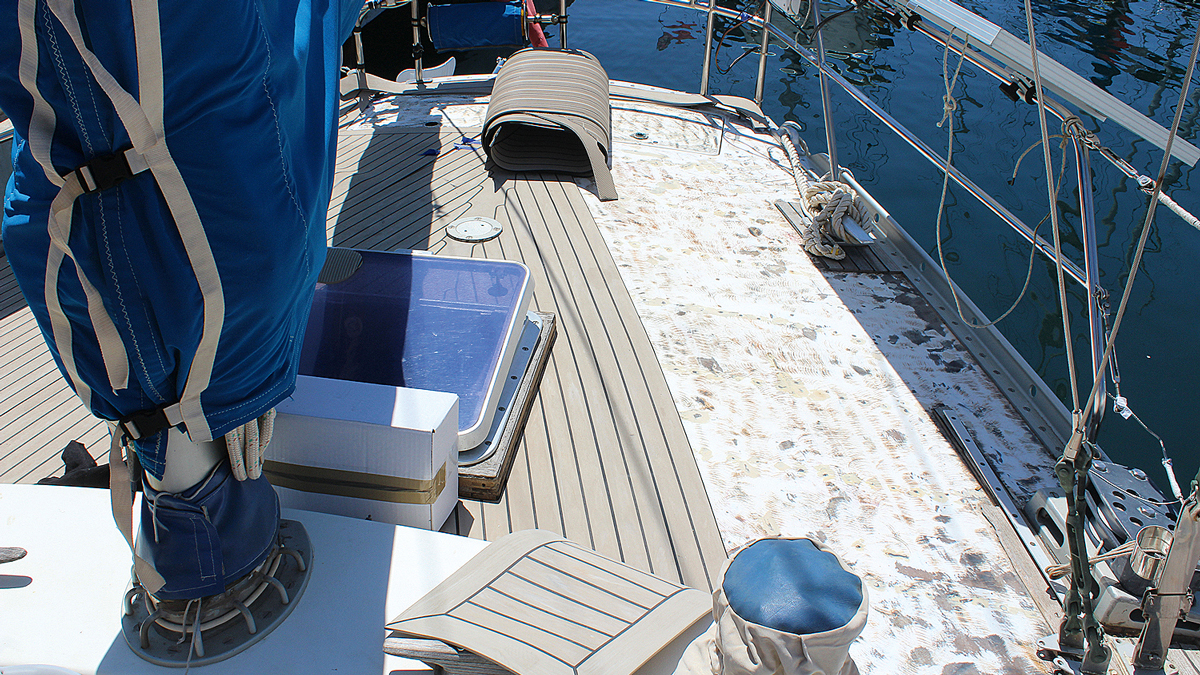
When the filling has been done the whole deck has to be sanded and keyed in. At this stage it must be spotless, a perfect surface for the new adhesive is essential.
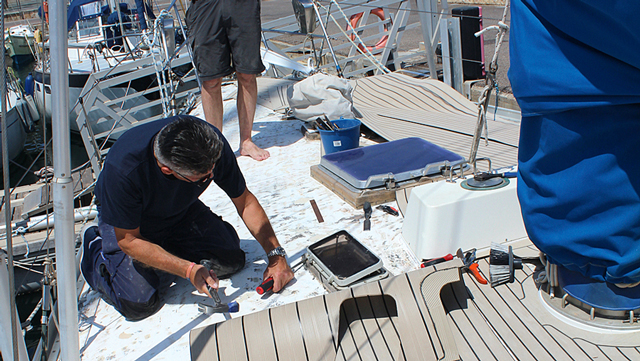
The templates are checked with the deck, removed and sent to be compared with the new deck in the factory. The decks are packed in the factory then delivered to the boat.
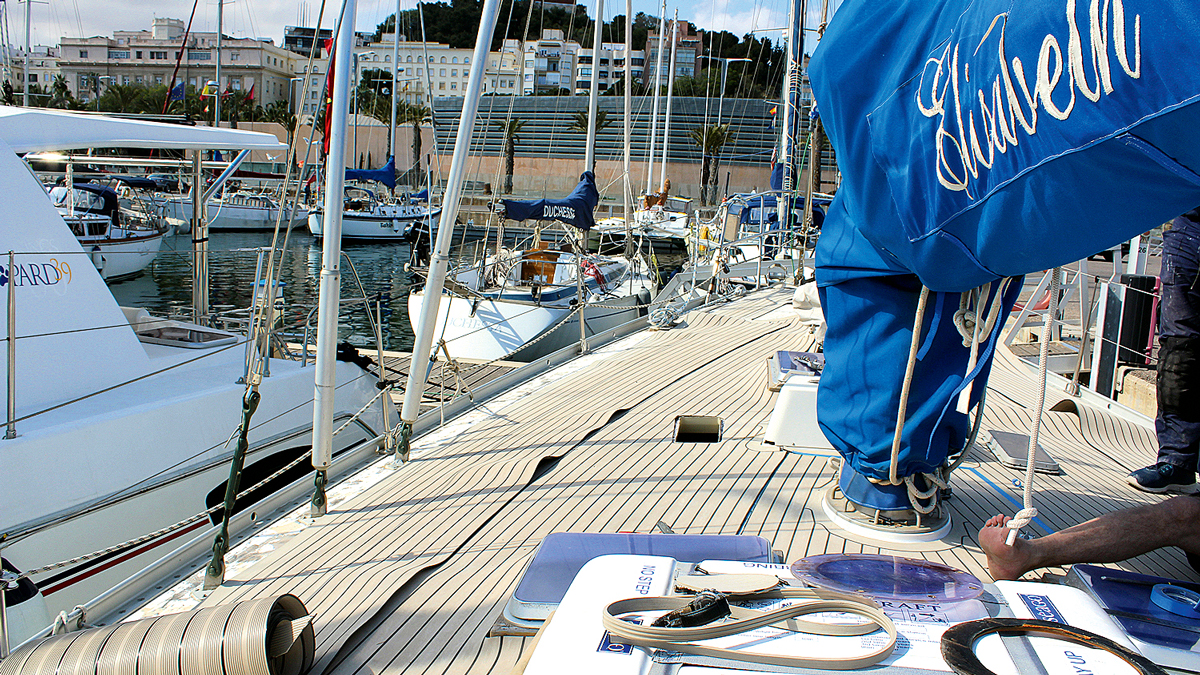
Everything is laid flat in the sun to warm the material. This ‘relaxes’ it and takes any distortion out. Minimise footfall as any contamination or small stones on the deck cause problems.
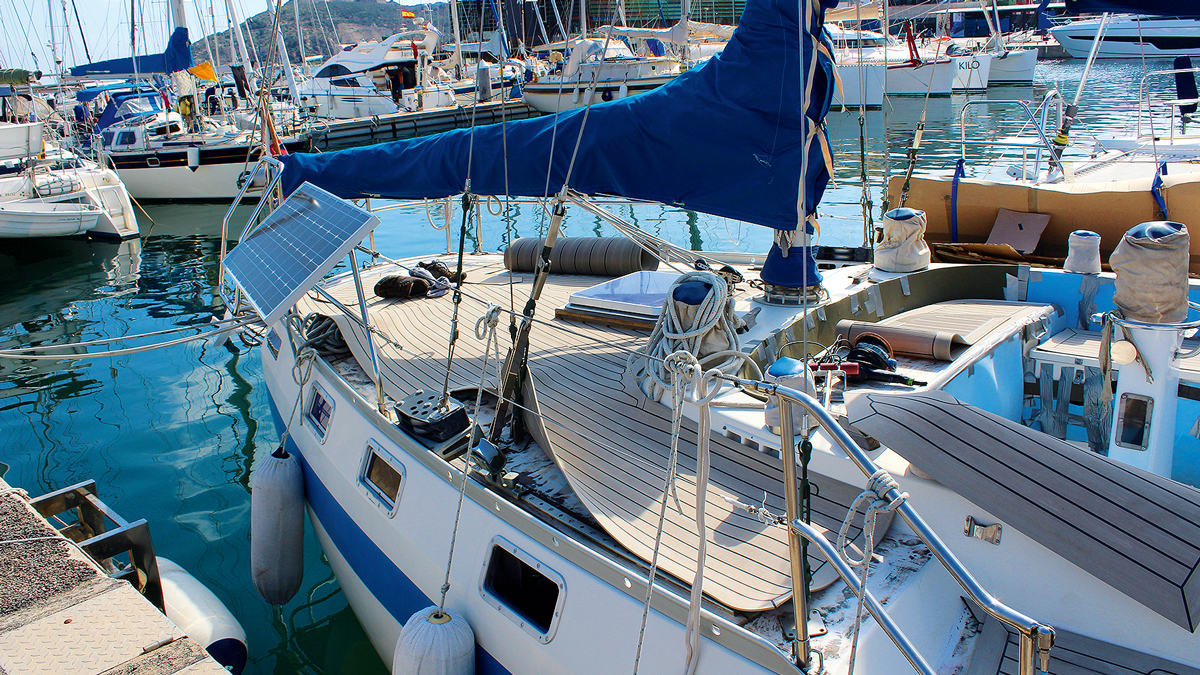
Big sheets of decking are brought on board, trimmed and rolled down on top of adhesive. All of a sudden there is a perfect piece of deck instead of a grey and scratched gelcoat.
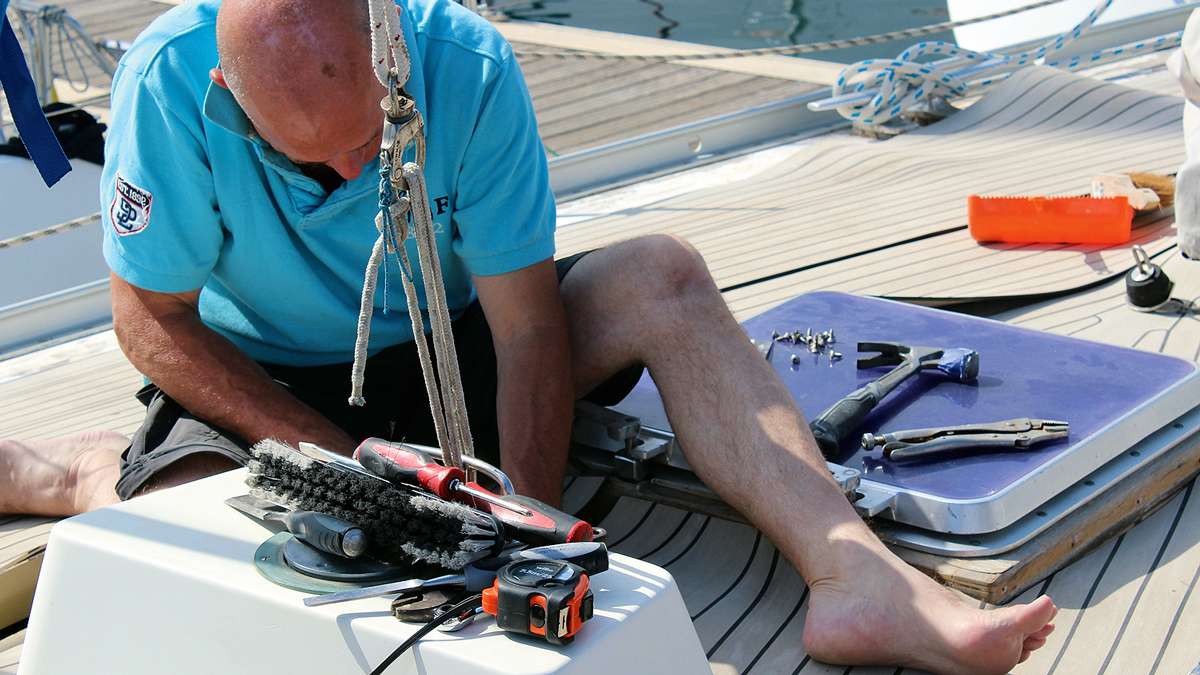
Within a few days the bulk of the deck was down, but once the big bits are in place there are smaller and trickier bits to fit.
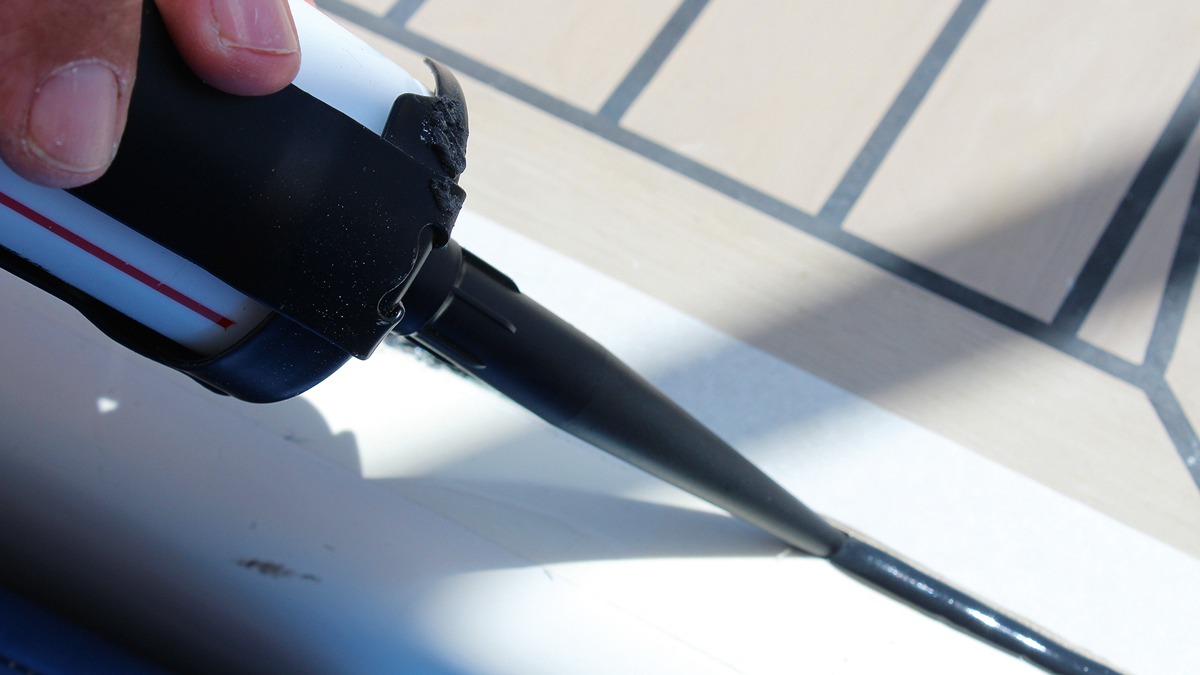
Finally all the caulking has to be done and hatches, deck-lights, blocks and fittings have to be refitted.
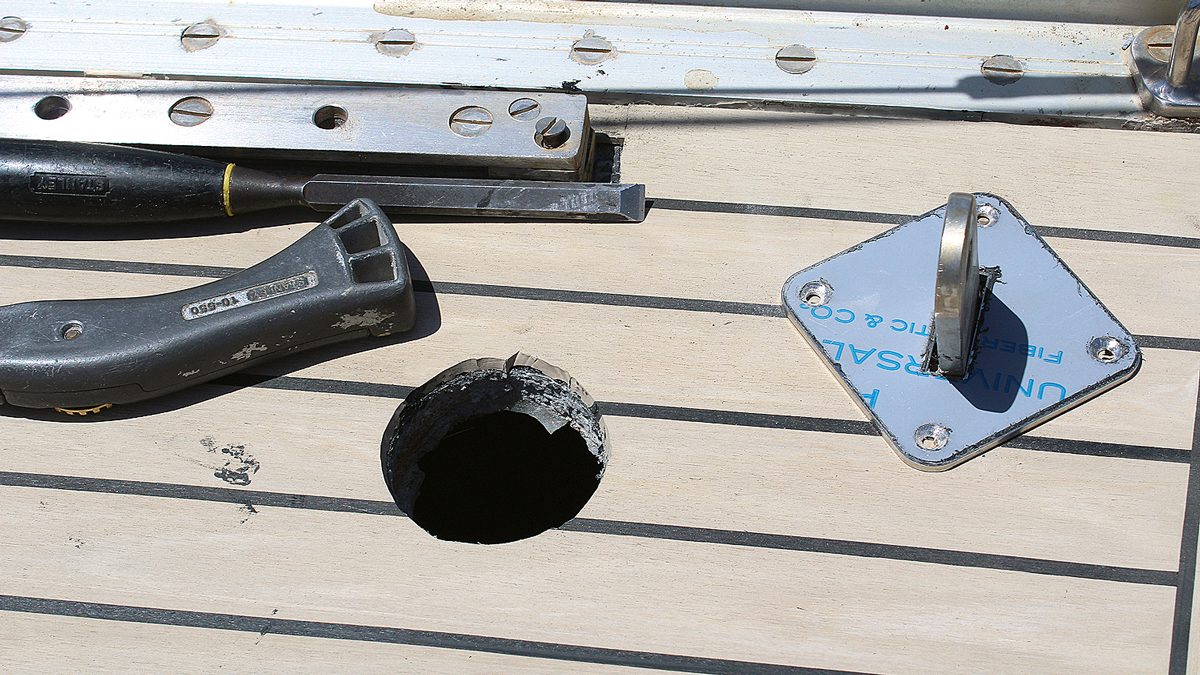
It’s a very skilled job to relocate the holes where the bolts for granny bars and suchlike have to go back.
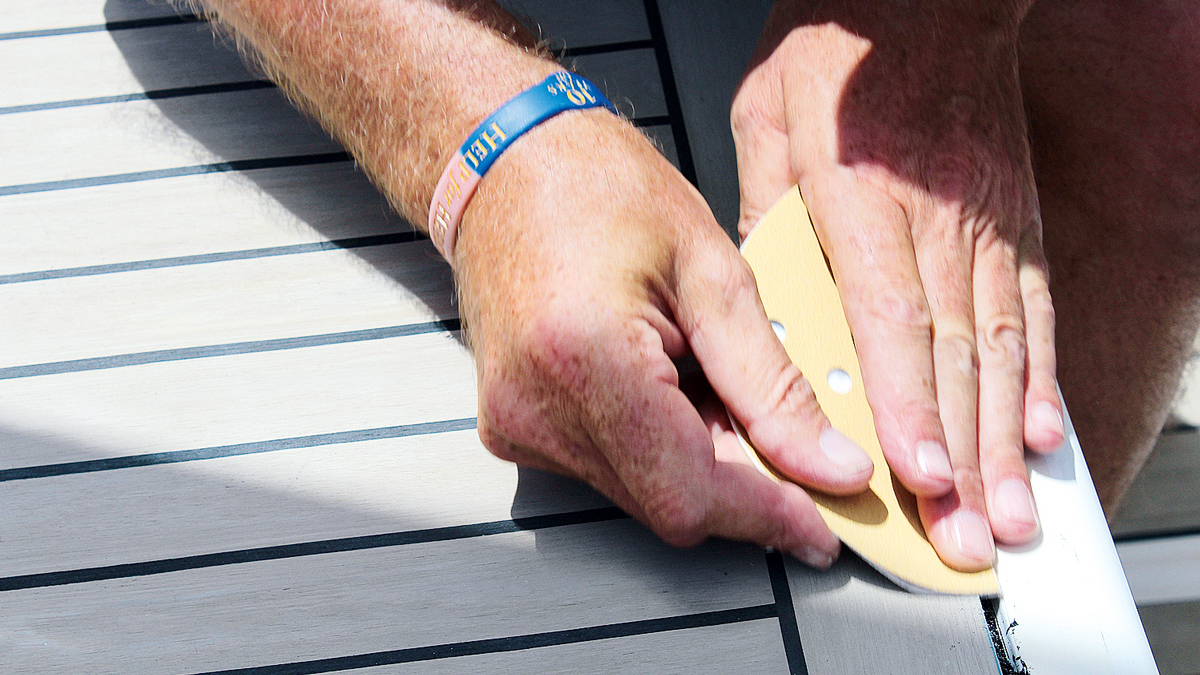
The whole deck then gets a sanding to bring up the finish. I had the dull grey plates around rigging chain-plates and deck-lights remade in stainless steel, which set the deck off really nicely.
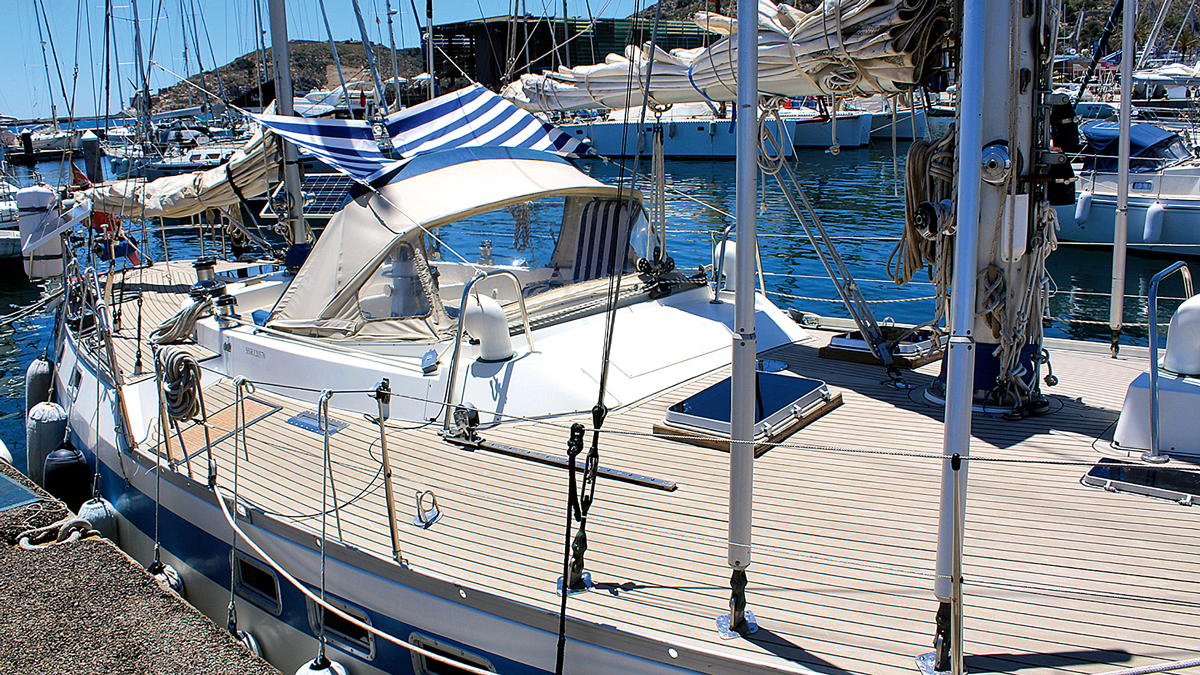
Finally, with the last fittings found and screwed down, the new deck made an unbelievable difference.
Why not subscribe today?
This feature appeared in the March 2022 edition of Practical Boat Owner. For more articles like this, including DIY, money-saving advice, great boat projects, expert tips and ways to improve your boat’s performance, take out a magazine subscription to Britain’s best-selling boating magazine.
Subscribe, or make a gift for someone else, and you’ll always save at least 30% compared to newsstand prices.
See the latest PBO subscription deals on magazinesdirect.com