Phil Symonds tackles the problem of aged bonding on the front windows of his 2008-model yacht to maintain value and usage
Like many owners of Jeanneau Sun Odyssey 42 DS yachts with bonded windows manufactured from 2005 onwards, I began to experience leaks, writes Phil Symonds.
Exposure to ultraviolet (UV) light over time, and adhesive nearing the end of life, led to the window bonding coming undone aboard my yacht Lemon and Lime.
The two front windows were the first to show signs of degrading, starting with a small leak.
After four months more cruising around the Mediterranean the leaks increased to the point where when it rained we had three to four washing-up bowls of water coming into the boat. It was unsustainable.
I spent months researching the available solutions. While re-bonding is an option, you need to get the windows out in one piece to do so. Jeanneau stopped production of spares and while some window types are available, not all, so removal is risky, especially because Plexiglass with UV damage has an increased chance of breakage.
For a boat priced upwards of £150,000 – or for the 64 DS just short of £ 1 million – that’s a dreadful situation.
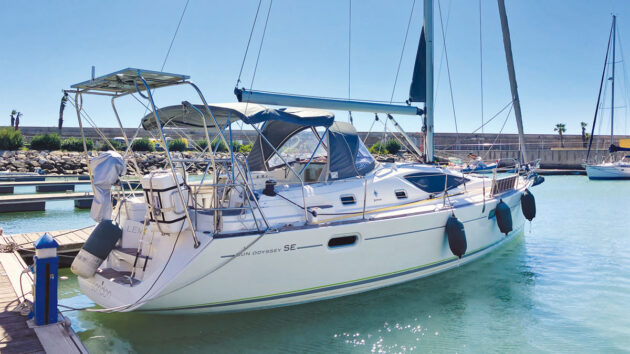
Phil’s Jeanneau Sun Odyssey 42 DS Lemon and Lime. Credit: Phil Symonds
This is so serious that if there isn’t an alternative supply of windows these boats will become unsaleable.
The challenge for owners is to find manufacturers who can replace the window sets.
This means using the old windows as patterns, so owners need to pay for mould tools as well as the windows.
I found a few UK Plexiglass companies that were prepared to do this but it would mean the boat would be without windows for up to four weeks and weatherproofing the boat in the meantime would be difficult.
The UK companies’ tooling will only make one boat set before having to be destroyed.
The windows of new Jeanneau Sun Odyssey 42 DS boats are often now the bonded Plexiglass type, cut to shape, fitted into a slot on the hull, and bonded. Some are large and the Sun Odyssey has six of these.
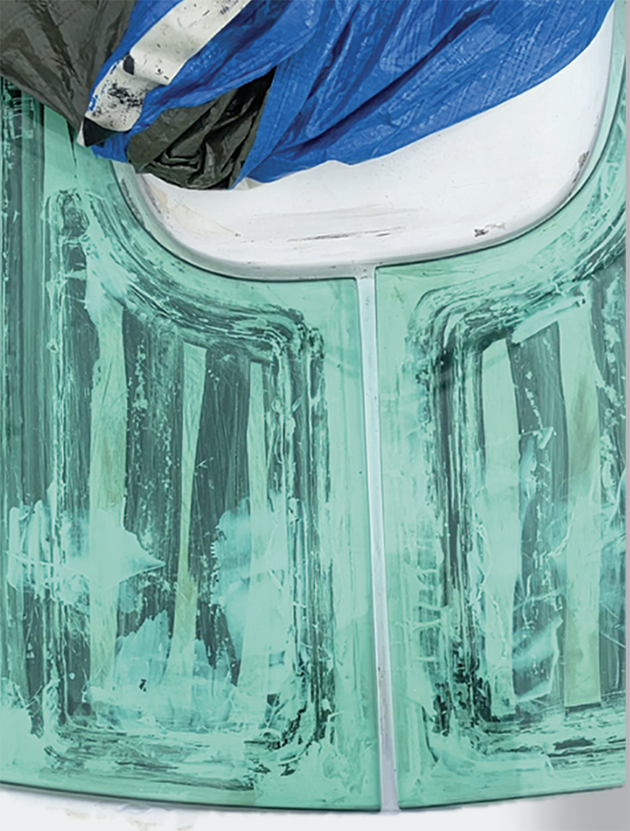
The windows were dry fitted first. Credit: Phil Symonds
The problem is that on older boats – mine’s a 2008 model – the bonding is beginning to degrade and they are leaking – you cannot get all the replacement types from Jeanneau and the ones it does supply are prohibitively expensive.
Three Jeanneau agents quoted me between £1,400 and £2,500 per window, plus the fixing fee.
I was determined to find a sustainable solution. I am a manufacturing engineer based in the Algarve, so I found a Portuguese company that makes multi-use moulds, which was willing to use the old windows to create two mould tools.
The quote confirmed was €3,000 (£2,600) for a complete set of six windows, and €2,000 (£1,733) for a second set. This is expected to fall to €1,500 (£1,300) for subsequent sets.
Originally it was thought the mould tools would be made from GRP.
The proposal was to cover the surface of the old windows in gelcoat, then fibreglass laid over to form the shape.
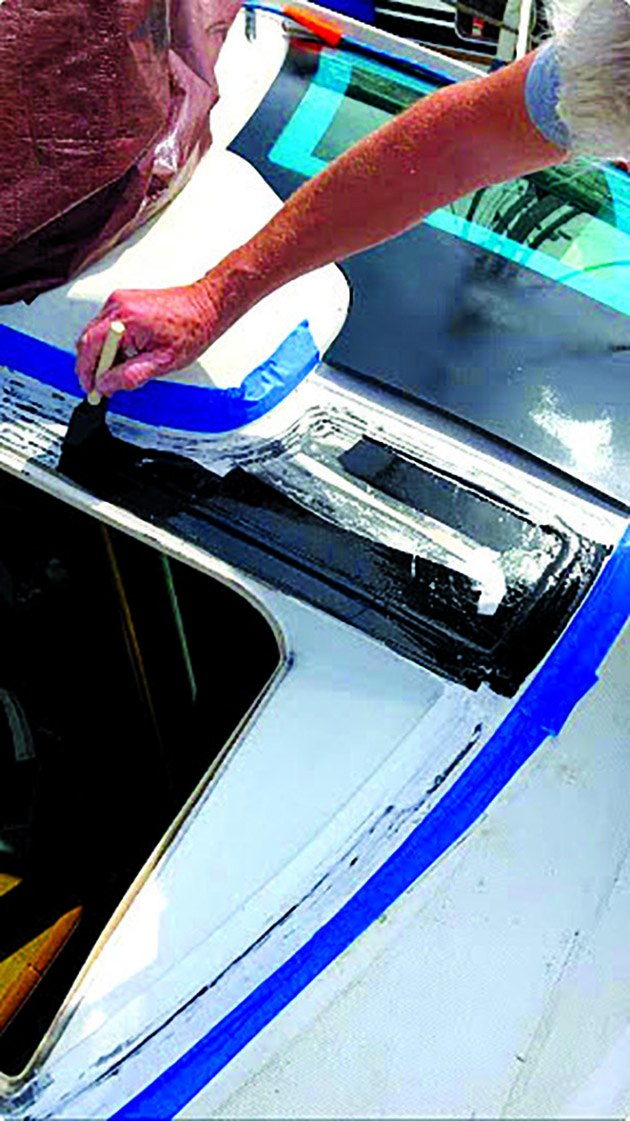
Applying the Sikaflex bead to the primed surface around the window. Credit: Phil Symonds
The manufacturer later decided to use plywood as the moulding process needed to provide an overbend so that as the Plexiglass cooled it would settle back to the correct form.
After some difficulty, the manufacturer achieved a near-perfect solution, and now has the tools for further units if needed.
The old window extraction took two days and it was clear that the port window had little bonding holding the window in.
It seems that the original bonding had only adhered to the boat and not to the window at all, possibly due to a primer issue.
Consequently, the port window virtually fell out. However, the starboard window was a different proposition, and various power tools were needed to separate the bond between the window and the boat.
Once the windows were removed and cleaned, they went for moulding. This took 15 days.
During this time the cleaning and preparation required was a pretty physical process.
The original bonding material (probably Sikaflex) is a tough substance. Sharp blades are essential and several different types of tools are needed. To remove the residue acetone is used.
The cleanliness of the GRP frame is essential, and no amount of shortcut is advisable.
In the case of Lemon and Lime, there were also light stress cracks present both under the window and at the four corners of the window frames.
I do not believe these to be structural but as the area was being prepared I used a Dremel to clean out the cracks, cleaned with a vacuum cleaner, acetoned and filled again with gelcoat, and then gave a light sanding to finish off the visible aspects.
Jeanneau provides windows with frits – the black, dotty edge that automotive and boatbuilders use to make the eye less prone to a hard edge.
I could not reproduce the dots so instead I planned to have a solid band around each window.
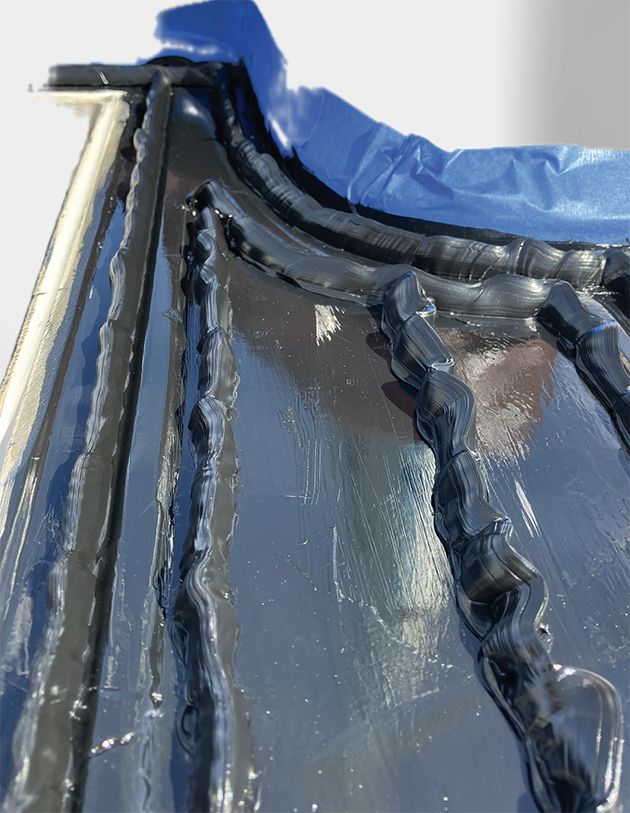
Applying the Sikaflex 295UV in a V-shape profile. Credit: Phil Symonds
Once the windows were received, I set about preparing them for fitting.
Firstly the windows were masked up using the old windows laid underneath as patterns. Then each edge to be painted was lightly abraded and then cleaned using Sika 205 Activator.
This is a wipe on-wipe off process with a 10 minute drying time before applying acrylic black paint.
The fitting process was tricky but with a methodical approach and the right conditions it should be within the ability of most boat owners.
For the Sikaflex 295 UV to work, the temperature should be between 15-23º and it needs to be dry.
The inner area and the boat frame were masked up and the inner surface of both window and boat frame were lightly abraded using 200-grit paper.
The surfaces were vacuum cleaned and then the Sika 205 Activator was applied as before.
Ten minutes later Sika 205 G+P Primer – a black primer to help the Sikaflex 295 UV to bond – is applied to the GRP boat frame.
The primer dried surprisingly quickly. On the plexiglass window, a different primer was used because the G+P primer might produce stress cracks in the plexiglass product.
The primer, Sika 209 N, again black, and fast drying was applied. Now for the fitting of the windows.
Black Sikaflex 295 UV is applied to the boat GRP frame, not the windows.
A single bead sits in the channels provided in the Jeanneau moulding process. These channels are shallow but they do act as a guide.
The shape of the bead is important, as is the cutting of the application nozzle.
The bead is around 20mm at the base and is a 30mm high pyramid shape.
It takes exactly two tubes for each window and would be a horror story if you ran out before finishing the job, as Sikaflex begins to crust in 20-30 minutes.
I used glass suction lifting cups to help position the windows in place. This is where the form of the windows becomes critical.
I was very pleased with the manufacturer’s work as they fitted really well.
Once dropped into position, wedges were used to provide a constant distance between the window and the boat frame.
The other critical issue was ensuring a constant weight was applied to hold the window down while the Sikaflex sets.
I used five 5kg soft sand gym weights, positioned around each window.
The drying process takes up to two days before the weights can be removed; it then takes a further four days before the bond is complete.
Sikaflex continues to cure, however, for several more days.
Lastly, a white Sikaflex 295 UV bead is applied around the edge of the windows: one tube for each window.
The masking should then be removed within 30 minutes as thereafter the masking is bonded in with the Sikaflex!
I am delighted with the results, as despite the dirty process and hard work it looks as professional as the original.
And it doesn’t leak – a fundamental requirement in a boat, right?
Email Phil, if needed, for more information at yachtlemonandlime@gmail.com
Jeanneau’s response to Jeanneau Sun Odyssey 42 DS window problems
Since 1995, the Jeanneau shipyard has belonged to Groupe Beneteau specialising in the construction of motor and sailboats and prefabricated homes.
A UK-based dealer, which specialises in Jeanneau sailing yachts, previously told PBO: “Unfortunately, Jeanneau are not always able to supply all spares for some of the older generation models and as a dealer, we can only source genuine replacements.
“As a main UK dealer, in these situations, we deal with our local UK contractors and we template the windows in place (in case of a breakage when removing) and then remove and template in order to produce replacements on a boat-by-boat basis.
“For boats abroad, we would recommend talking to the local Jeanneau dealer who should be able to implement similar solutions locally.”
PBO contacted Jeanneau but the company did not wish to respond.
Problems with ageing bonded boat windows on the Jeanneau Sun Odyssey 42 DS
The window bonding on some Jeanneau Sun Odyssey 42 DS yachts manufactured from 2005 onwards is coming undone, caused by…
Jeanneau Sun Odyssey 380: “excellent all-round sailing performance”
The 380 is one of the latest offerings in Jeanneau’s updated Sun Odyssey range. Peter Poland puts the boat through…
15 boat fixes at sea: sailors share how to deal with torn sails, rudder damage, chafe & more
Transatlantic sailors tell Ali Wood how they used their ingenuity – and sometimes bravery – to cope with emergencies on…
How to use sealants for fixing leaks – PBO Project Boat restoration
A downpour of rain shows that making PBO Project Boat Maximus watertight is a priority, so Ali Wood gets some…
Want to read more practical articles like Replacing Jeanneau Sun Odyssey 42 DS windows?
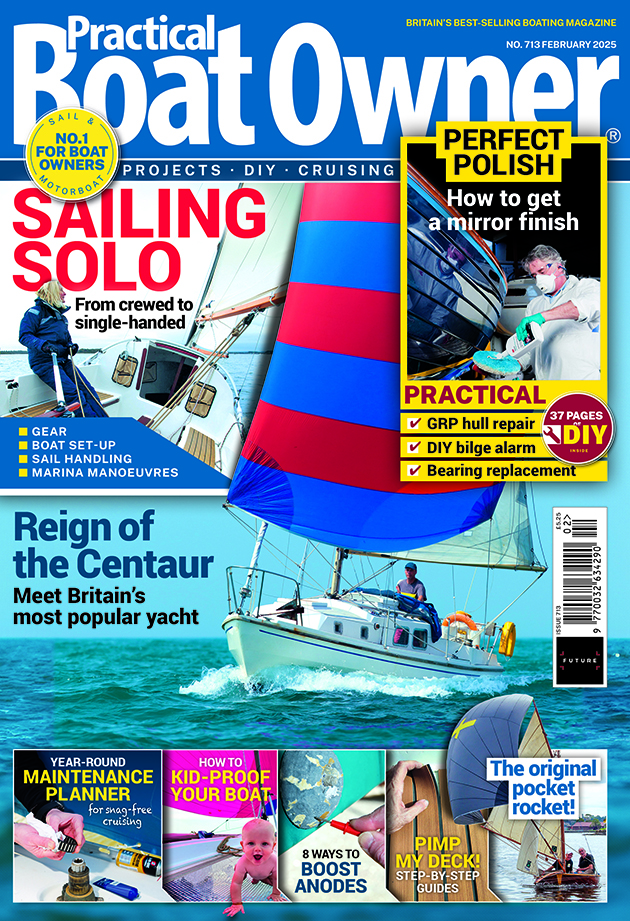
A subscription to Practical Boat Owner magazine costs around 40% less than the cover price.
Print and digital editions are available through Magazines Direct – where you can also find the latest deals.
PBO is packed with information to help you get the most from boat ownership – whether sail or power.
-
-
-
- Take your DIY skills to the next level with trusted advice on boat maintenance and repairs
- Impartial in-depth gear reviews
- Practical cruising tips for making the most of your time afloat
-
-
Follow us on Facebook, Instagram, TikTok and Twitter