Even the best marine ply is not totally moisture resistant and will eventually succumb to rot after extended periods of raised moisture levels. Supersede Marine Board is said to be the first true 1:1 replacement to marine-grade plywood.
Ever since its advent some 75 years ago, marine plywood has been a wonder material for boatbuilding.
As an inexpensive material, it was a key factor in bringing the prospect of sailing and boat ownership to a mass audience, yet it also has an excellent stiffness-to-weight ratio, with the result that it was also used for many fast offshore racing yachts and is still used extensively, even by the big production boatbuilding yards, for structural components such as bulkheads.
Today it also evokes a sense of timelessness, harking back to traditional craftsmanship and the unmistakable aroma of sawdust and wood shavings.
However, the notion of it being a safe and sustainable material doesn’t necessarily stand up to close scrutiny. In particular, the glues used to bond the plies together are noxious.
While this may not be a concern for boat owners, as emissions drop quickly after manufacture, it can be a different story for the staff of plywood manufacturers and boatbuilders.
This factor also makes disposal of plywood more of a challenge, whether that’s at the end of the boat’s life, or simply offcuts that are discarded during the build process.
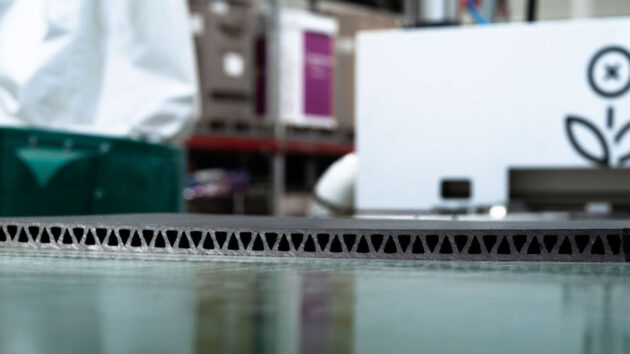
At the end of its life, Supersede board can be recycled into pellets and used again
Problematic ply
The use of plywood in a marine environment is also problematic in other respects.
For a start, even the best marine ply is not totally moisture resistant and will eventually succumb to rot after extended periods of raised moisture levels. These are among the factors that led Jordan Darling, Sean Petterson, and Shane Kenyon to search for an alternative solution.
The product they developed, Supersede Marine Board, won an IBEX Innovation Award for Boatbuilding Methods and Materials in Florida in October.
The material is an engineered extruded sheet crafted from plastic waste that’s 100% recyclable, waterproof, and rot-proof. It also will not splinter, split or warp.
We understand production can easily be scaled up and at the end of life the material can be returned to pellet form to be recycled into other products.
“Boat manufacturers and their insurers have more experience than almost anyone with the headaches of plywood – from the persistent challenges associated with inconsistent performance, warping and splinters, to extensive maintenance, high costs, and little peace of mind,” says Petterson.
“We have created the first modern breakthrough addressing these issues with the Supersede Marine Board, a true 1:1 replacement to marine-grade plywood.”
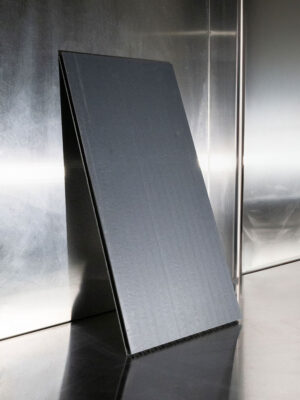
The increase in price of marine plywood means Supersede is now viable for boatbuilding
At the moment, it’s available in ½in (13mm) and ¾in (19mm) thicknesses that can be used as a direct replacement for marine ply.
It’s also available in any custom length over 4ft (1.2m), which has potential to save boatbuilders a considerable amount of wastage.
On the downside its density of 1,400kg per cubic metre is at least double that of most marine plywood.
While historically marine plywood was a cheap material, things have changed considerably, especially during the past five years, and it is now one third more expensive than in 2019.
This has clearly given Supersede headroom to develop a new product, which is priced at a similar level to the cost of marine plywood today.
Why plywood boats are making a comeback
A wonder material in the 1950s and 1960s, plywood is making a comeback. Rupert Holmes analyses what lies behind a…
Free boat plans – Build your own Nigel Irens 14ft rowing and sailing skiff
Fancy building your own Nigel Irens-designed 14ft rowing/sailing skiff? Nic Compton explains how to get the plans for free
First evidence of GRP boats’ “cancerous” impact on aquatic life
The ‘really worrying’ findings by University of Brighton researchers who undertook studies off the coast of Hampshire and West Sussex…