PBO’s wooden kit project boat undergoes her deck fit-out with the charity Oarsome Chance. Jake Kavanagh reports
The Secret 20 is a beautifully designed classic sailing yacht that can be built from a kit, one of which was delivered to PBO in 2016. Regular readers may well have followed her gradual transformation from a collection of pre-cut timber to a shapely hull form.
Transported to the premises of the charity Oarsome Chance in Gosport, Hampshire, the plywood hull was epoxy sheathed and faired before being rolled upright, ready to receive its upperworks.
Time is now pressing as the boat needs to be finished for display at the Southampton Boat Show in September. This will mean that everything has to be ready for sea trials in August. But then there’s nothing like a deadline to get a project finished!
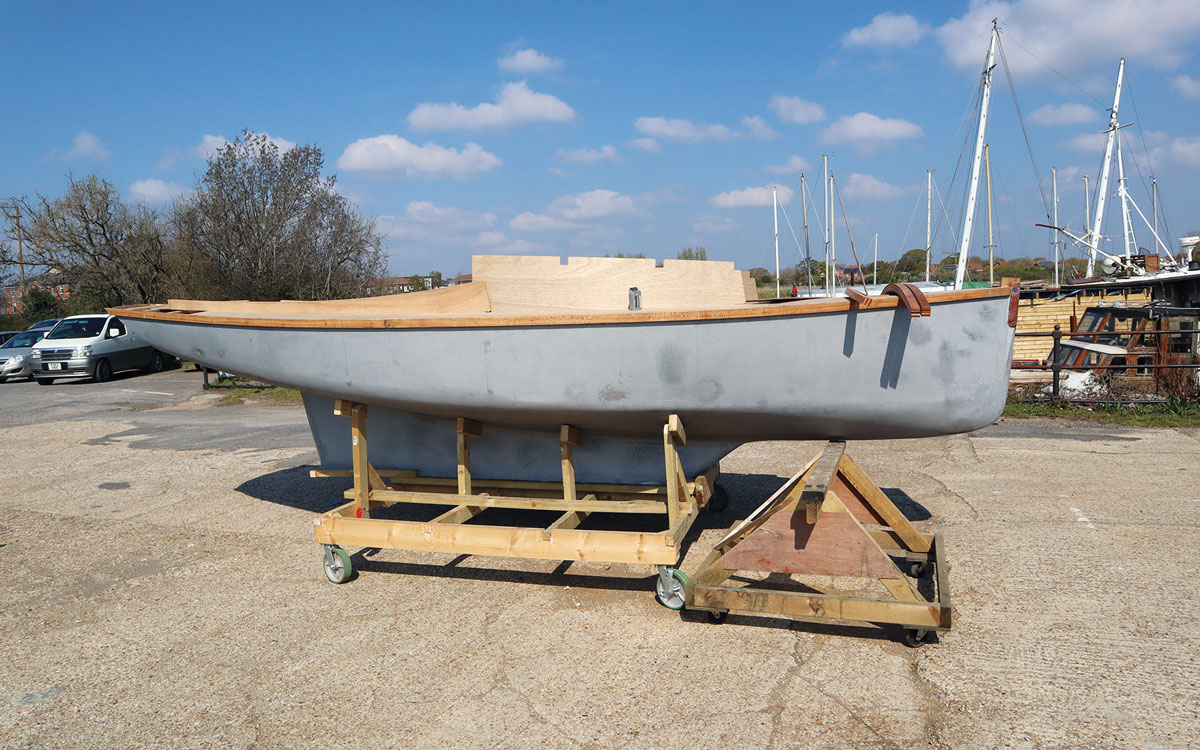
The hull has been returned to its upright position, and now the decks and cabin sides are being added. Note the laminated cross beams, which can be seen lying on the foredeck prior to dry fitting, and the slots they will locate into along the top edge
Oarsome Chance proved the ideal recipient of the kit boat when PBO relocated to Farnborough from Poole, as the charity is equipped with covered workshops and a team of boatbuilders plus volunteers to see the project through.
In addition, the charity teaches school-age children at risk of exclusion from mainstream education to work with their hands, which also includes working on Harvey, the Secret 20, under close supervision. The practical skills training is designed to get the students back into mainstream education.
Cabin options
Knee surgery meant the project’s mainstay, Jon Carver, was out for a six-week period so IBTC-trained boatbuilder Jesse Doyle stepped in to take over. Jon had left him a list of the most pressing jobs, which mainly entailed assembling and installing the cockpit sole and the sides of the cabin, which on the PBO boat is the larger, ‘standard’ cabin.
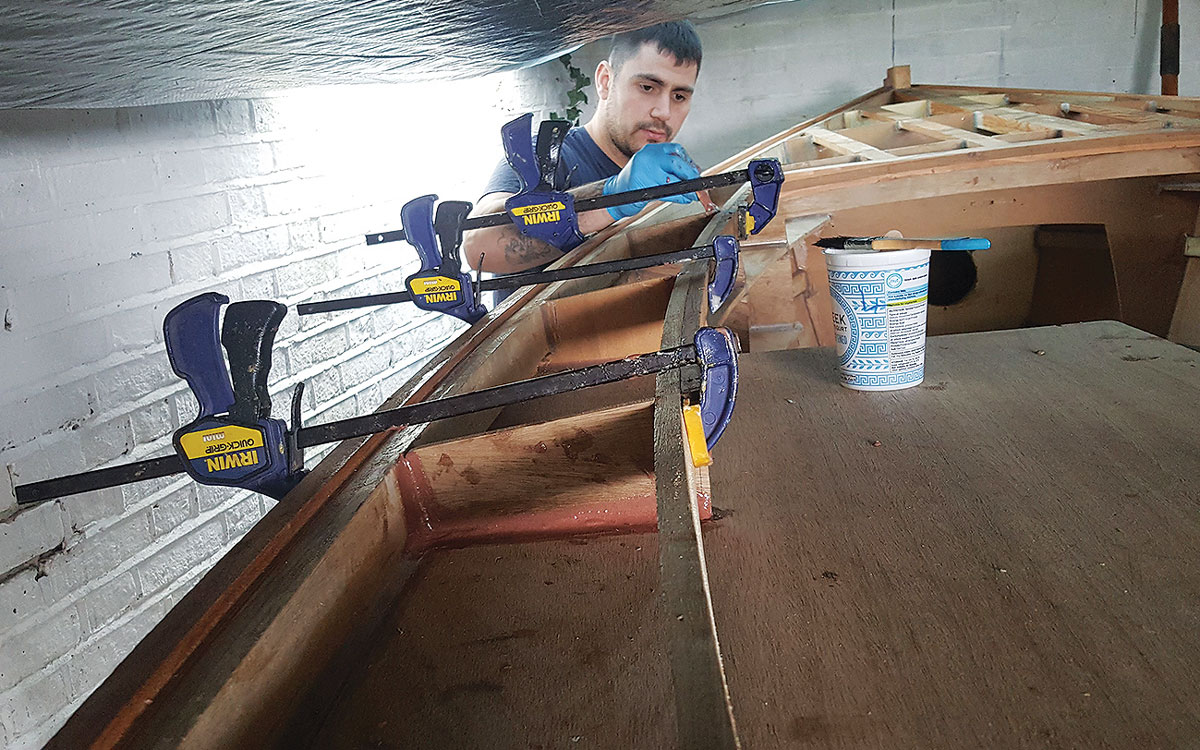
Boatbuilder Jesse Doyle secures the detached timber with adjustable clamps to pull the two pieces together
The Secret 20 is available in two main options, depending on how the owner plans to use her. In the brochure, Australian-based designer Derek Ellard explains the choice of cabin layout: ‘Intended primarily as a day sailer with good weekend accommodation facilities, the emphasis is on cockpit comfort and space rather than a cavernous cabin with all mod cons,’ he writes.
‘The (standard) boat will sleep two down below and two in the cockpit under canvas. Ample space is provided for a portable toilet, sink, stove and ice-box.’
Ellard describes the sailing characteristics as ‘beautifully balanced and satisfyingly fast’ but for those who require even more performance an ‘R’ type cabin version is available. ‘This offers a larger cockpit and a smaller cabin with a lower roofline,’ he says.
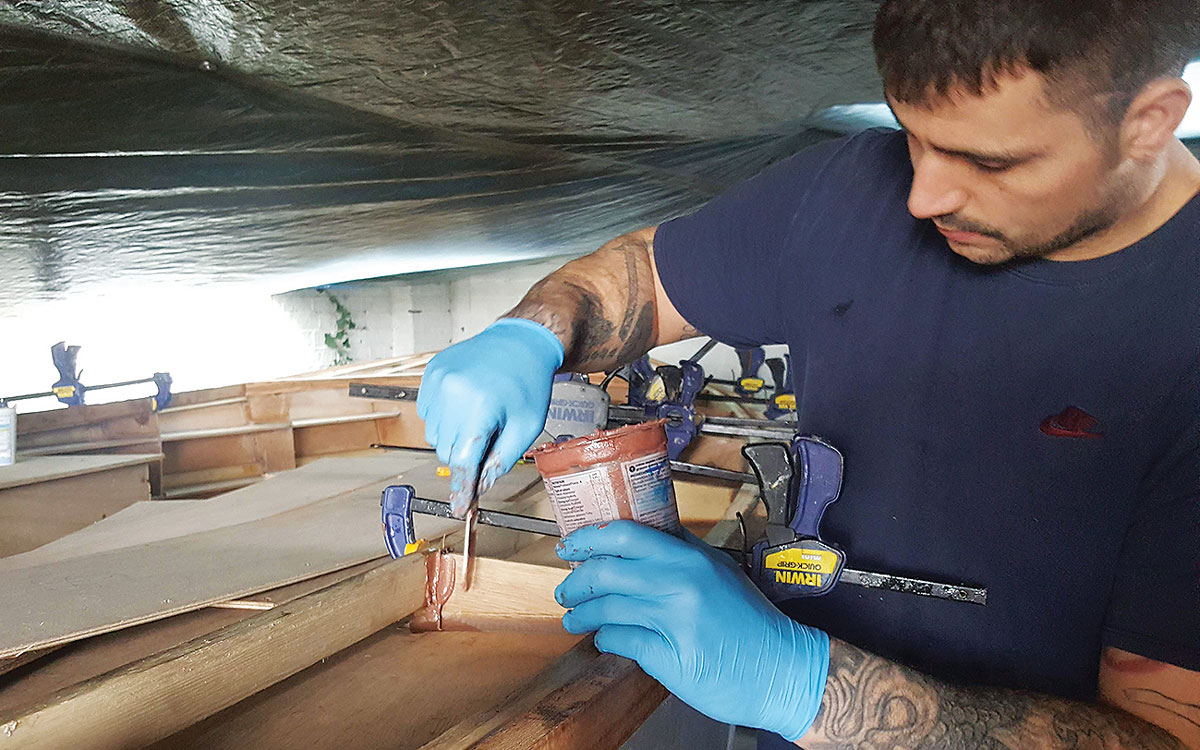
A mix of thickened West System epoxy is then applied in fillets along each join
‘The two bunks will remain for basic accommodation but there’s no space for a stove or sink in the cabin, although a portable toilet will sit snugly under the cockpit sole. However, four people can sit side by side in the R-type cockpit, and the boat will be very competitive in mixed handicap fleets.’
For the next stage of the fit-out, Harvey’s cabin would be shaped from sheets of 6mm marine ply overlaid with decorative veneers. The veneers themselves are sawn from Australian Silky Oak and are 10mm thick. This makes them structural as well as attractive. The roof rests on laminated beams giving a distinctive curve.
‘The Secret 20 is built around the time-honoured slot system marine ply framework,’ Ellard explains. ‘The bulkheads, floors, seat bunks and lockers are all an integral part of the structure.’
The cabin would be forming part of this ‘light, strong box section framework’ and would be fitted with stylish classic portholes and a curved sliding hatch.
Article continues below…
And the winner of the PBO Project Boat is…
A knock on the head while surfing convinced 29-year-old Anna Millington that she was dreaming when she was later notified…
PBO project boat – the Secret 20 kit – is back in build
Like many boat projects Harvey, the PBO Secret 20, has been the victim of circumstance. This unique, classic-style performance weekender…
Repairing broken fillets
Unfortunately, some minor damage was done when the boat was rolled upright, and this required repair before the rest of the project could continue. Having to fix problems during a build is time-consuming and can be costly, which is why production boatbuilders go to great lengths to protect each boat as it is fitted out.
Teams of cleaners also go aboard at every key stage to sweep up any metal swarf and collect dropped screws, tacks and other sharp objects, as they can be trodden onto freshly laid decks or new gelcoat. This is good practice on any boatbuilding project, large or small, but sometimes accidents just happen.
With Harvey, it was some wooden trim on the gunwale that needed new fillets. With the damaged section re-clamped, Jesse made up some new filleting material using West System epoxy, provided by Wessex Resins International.
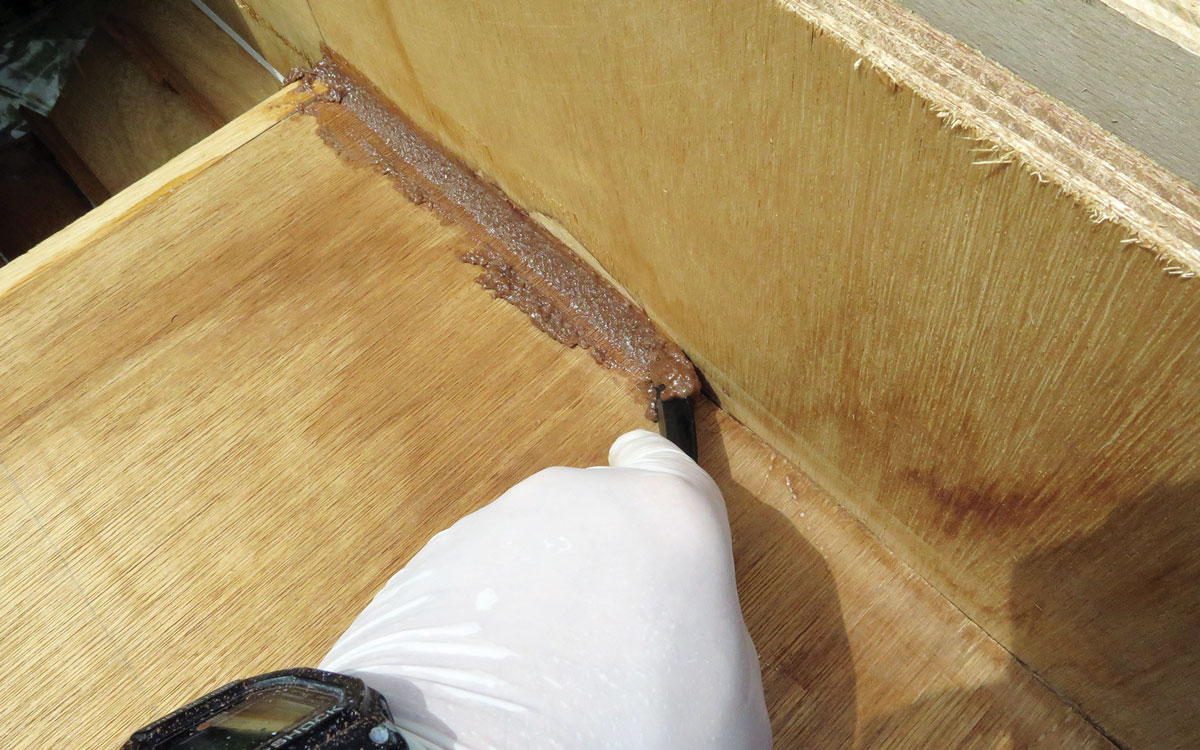
Filleting involves running a bead of thickened epoxy along the join line between two pieces of timber. West System 405 Filleting Blend gives the epoxy its brown colour and assists in creating a strong bond
Epoxy filleting is the process of running a seam of thickened epoxy along a join and shaping it with a semi-circular spatula. Once the epoxy has cured, its powerful adhesive properties ‘weld’ the surfaces together. To make this process easier, West System has developed a special additive made of colloidal silica and wood pulp and called it 405 Filleting Blend.
By mixing this additive into a mix of epoxy resin and hardener, Jesse achieved a brown-coloured paste the consistency of peanut butter which he was then able to smooth along the new wood in a shaped bead.
Veneering the transom
Although the plywood transom could be completely sheathed and faired along with the rest of the hull, the kit provides the optional extra of some Queensland Silky Oak trim. This is applied as a 10mm veneer and subsequently varnished, giving the boat an attractive classic-looking stern. Varnished timber compliments virtually every finished hull colour too.
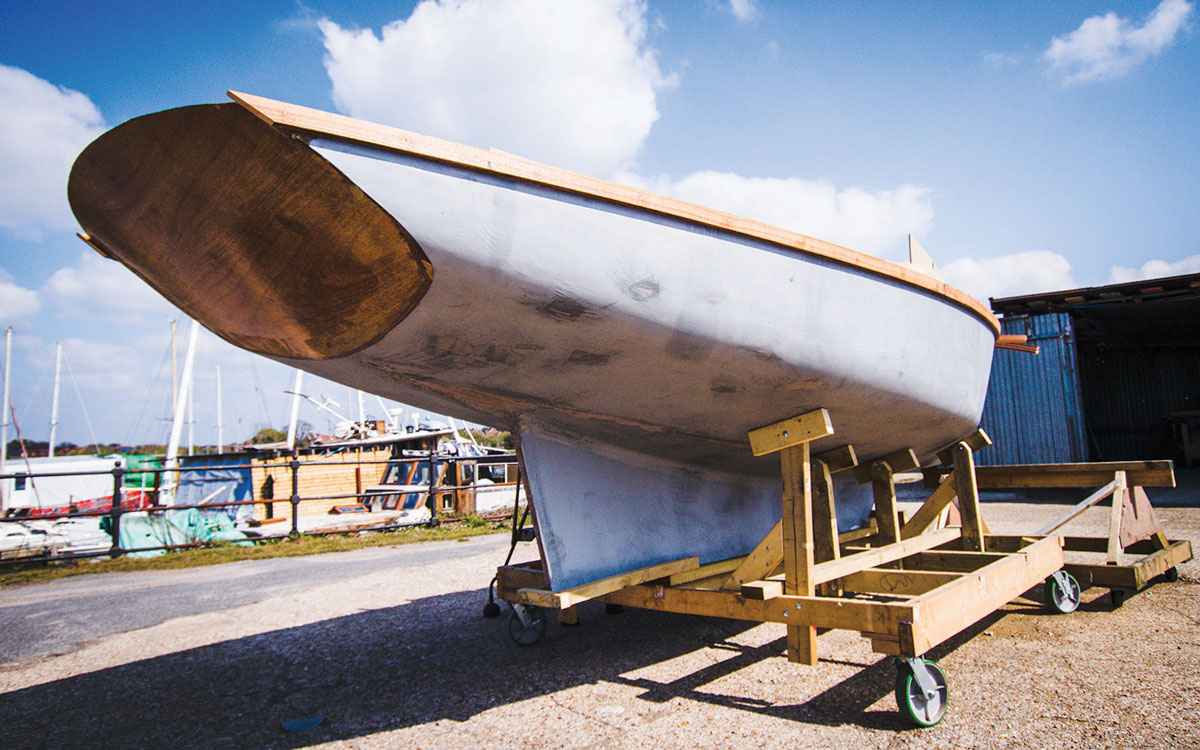
A striking design feature of the Secret 20 is her raked and curved transom – who said kit boats had to be slab-sided and boring – but this also presented some challenges. Photo: Jason Brodie-Browne
We were lucky. Scruffie Marine, the Queensland-based Australian suppliers of the kit, had included this optional piece of prized decorative timber free-of-charge as they were very keen to see it included on the transom.
“We’ll be sheathing with 135gsm cloth over the wood,” Jon explained. “We will use West System 207 Special Coatings Hardener to give the timber a really transparent gloss.”
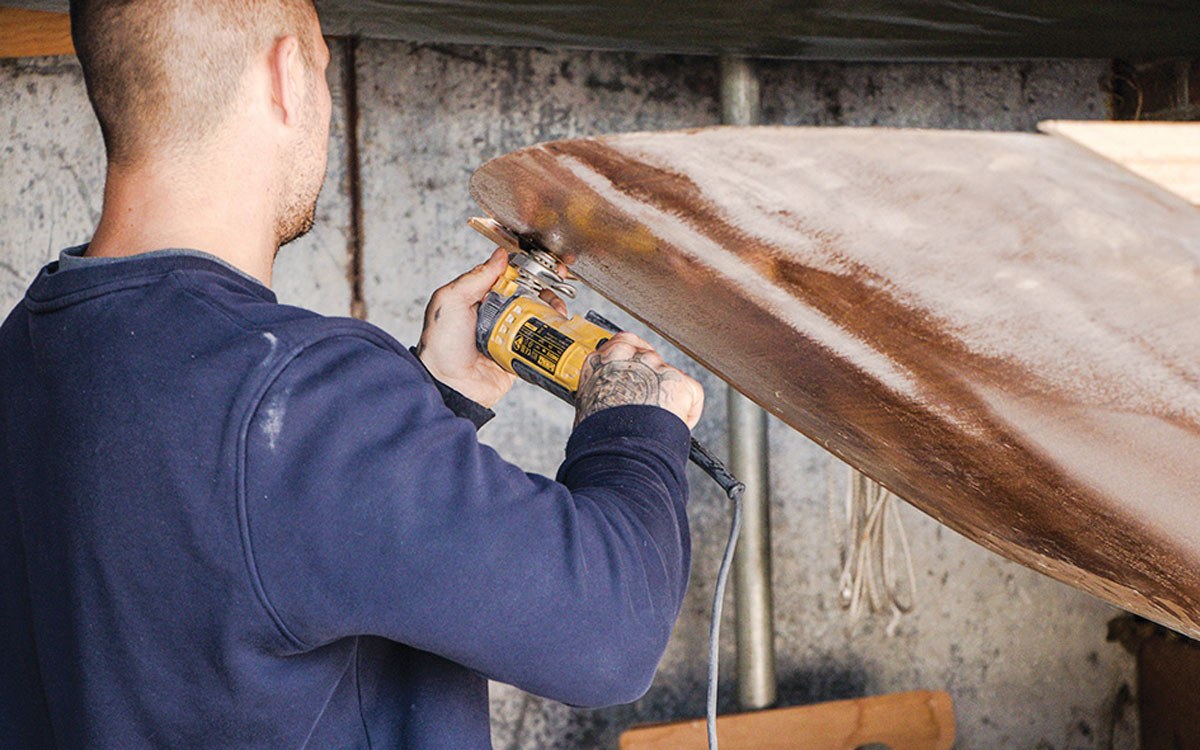
Jesse’s first job was to trim off the rubbing strakes which had been left deliberately over-long. Photo: Jason Brodie-Browne
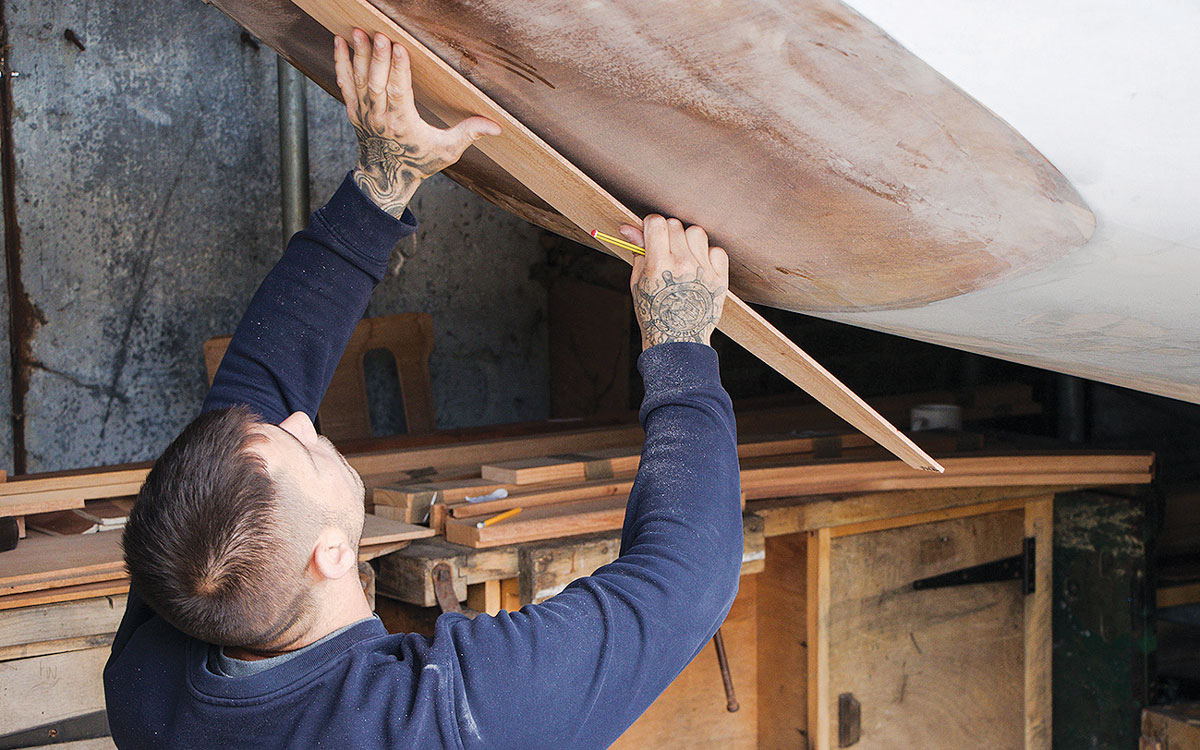
Measurements were then taken to identify the dead centre of the transom, top and bottom. Photo: Jason Brodie-Browne
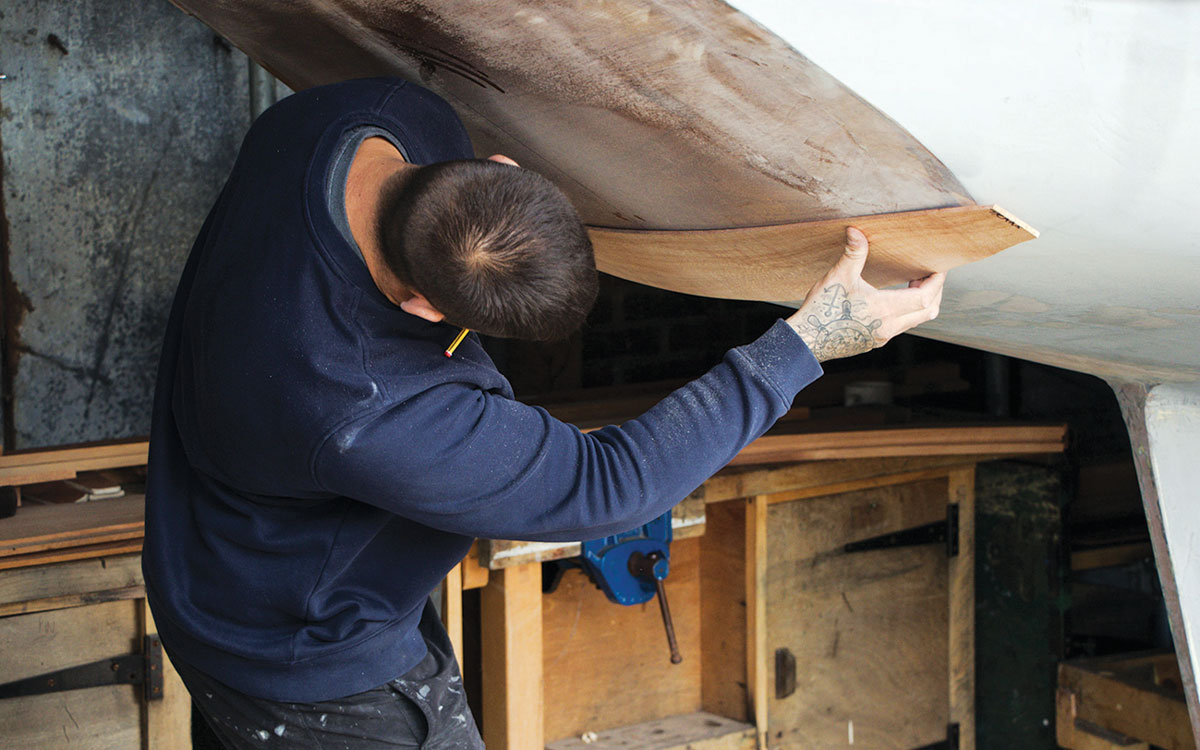
The lower piece of the Australian Silky Oak trim is offered up to the base of the transom… Photo: Jason Brodie-Browne
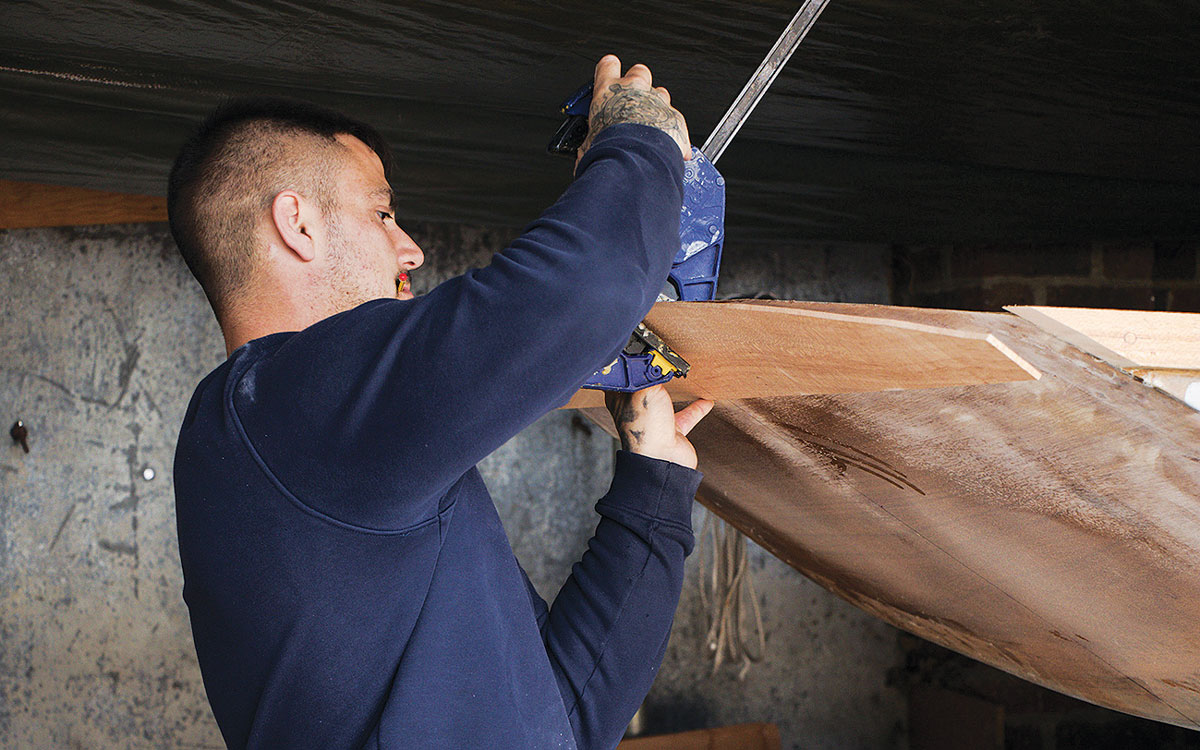
… followed by the top piece. It will be coated with West System epoxy with a special hardener for a rich, deep gloss. Photo: Jason Brodie-Browne
Building the cabin sides
The pre-cut cabin sides and coamings were assembled and dry fitted, and almost immediately the final profile of the yacht could be seen. The main beams, decks and rubbing strake had all been supplied with the kit, along with the pre-laminated beams.
“We’d have liked to have laminated the beams ourselves, as it gives the kids a great deal of experience with building up this type of structure,” Jon said.
Had that been the case they’d have bonded strips of timber together. The strips would be clamped over a curved former and would retain the curve when the epoxy had cured. Care has to be taken when using epoxy as a glue to ensure the piece being assembled doesn’t stick to the former (jig), so strategic pieces of polythene or parcel tape are used. Epoxy can’t adhere strongly to a shiny surface.
However, with the cabin sides temporarily screwed into place the Oarsome Chance team could simply drop the pre-formed beams into their slots and check for accuracy.
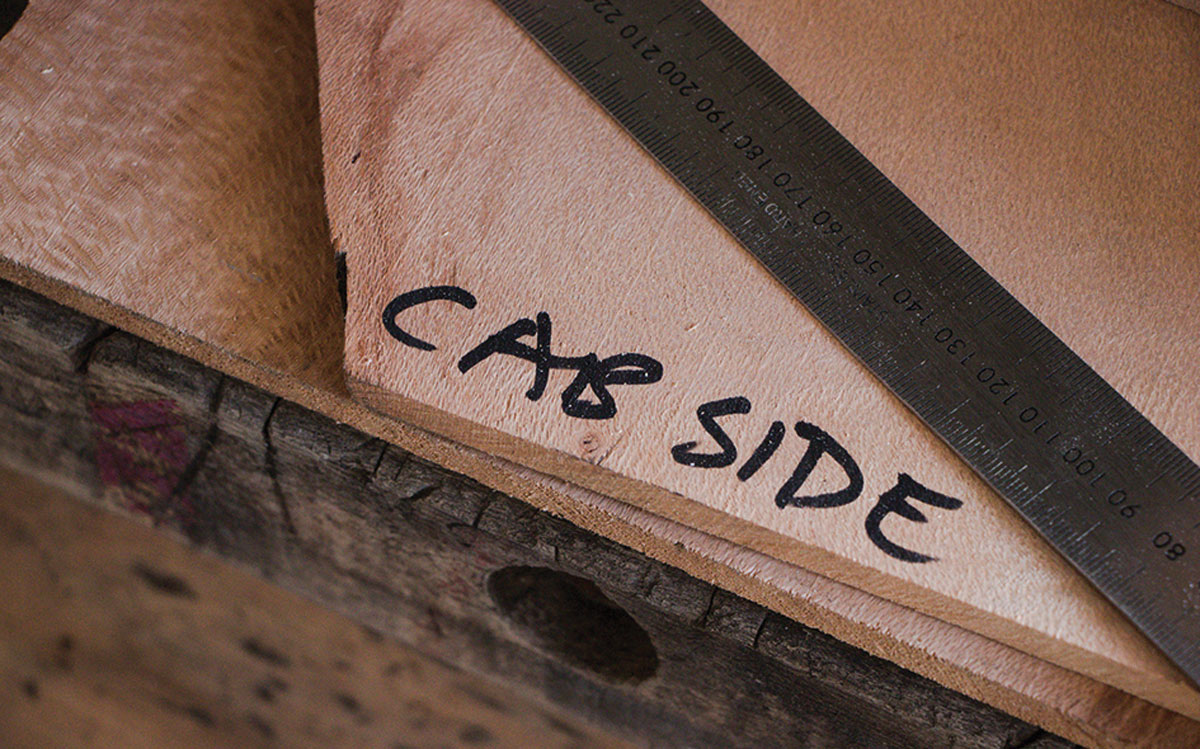
The 10mm external cabin veneer is cut from Australian Silky Oak and will be structural as well as decorative. Photo: Jason Brodie-Browne
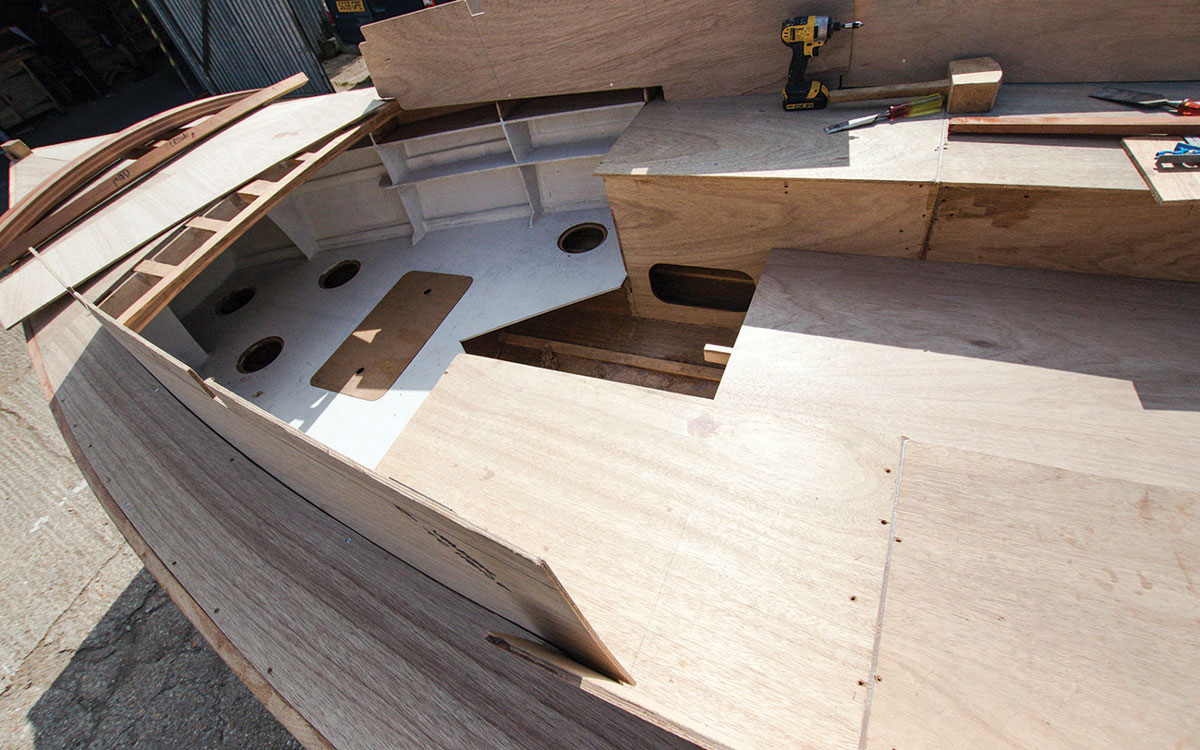
The cabin sides and coaming have here been temporarily screwed into place to check for alignment. Photo: Jason Brodie-Browne
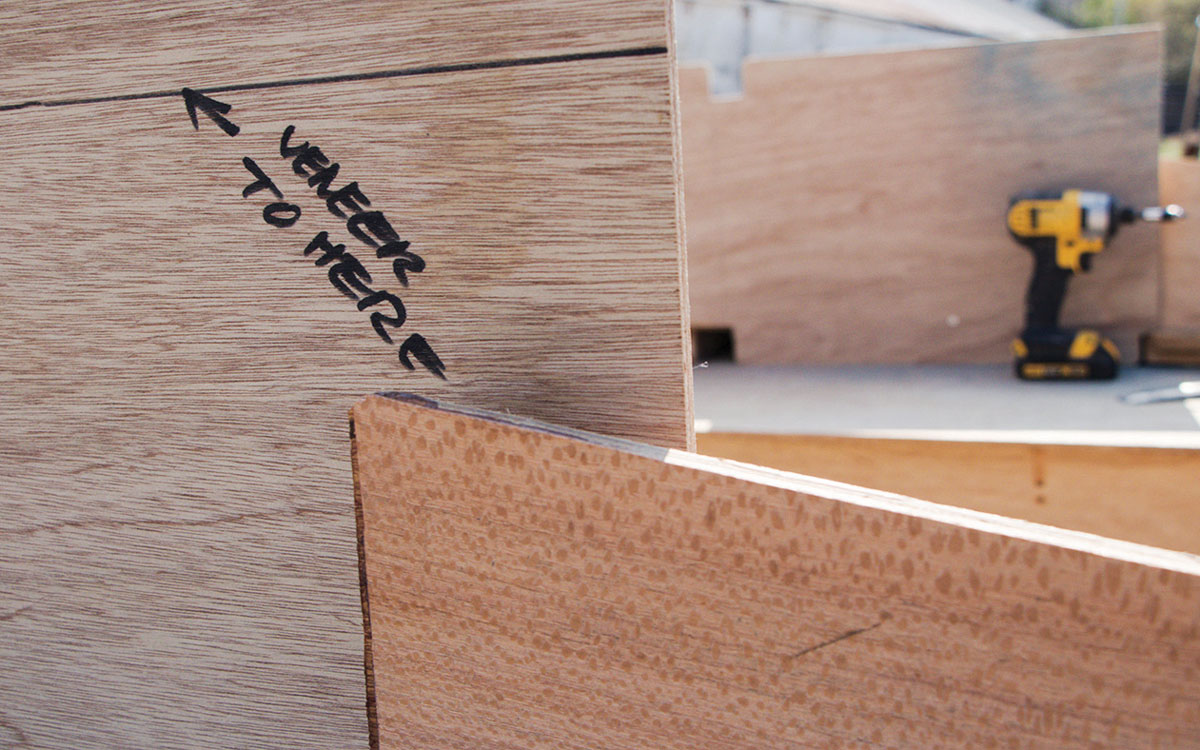
The coaming curves in to meet the cabin sides, with various options for making the join a decorative one. Photo: Jason Brodie-Browne
Cockpit sole
The Secret 20 is fitted with a self-draining cockpit, a major safety feature in any modern boat. Aft of the cockpit is a well to house an outboard motor, which frees up the space under the cockpit sole otherwise needed by an inboard. Harvey will be using the latest Torqeedo Travel 1103C electric outboard, kindly donated to Oarsome Chance by Torqeedo.
The frames for the cockpit sole which would take the longitudinal beams had already been made by the PBO team and the beams themselves were put into place. Unsupported plywood floorboards, even half an inch thick, would be prone to sagging over time.
“The decks were supplied as pre-cut pieces,” Jon said. “These are all 9mm marine ply and fitted relatively easily. They each had labels on them, but as they were moved around in storage and transport, some of the labels came adrift, so some detective work was required to find where each piece went!”
To check that Harvey is going together just as it should, the Oarsome Chance team intends to compare it with another Secret 20 already afloat.
“To help us see how various tasks have been completed, we are planning a trip up to Suffolk to see a Secret 20 that has been completed,” Jon said. “It’s always a good idea to look closely at a finished project, as you can see how things fit together, and where there may be potential pitfalls. You can also see some clever ideas or modifications that other owners have done and you can bring them in at the build stage.”
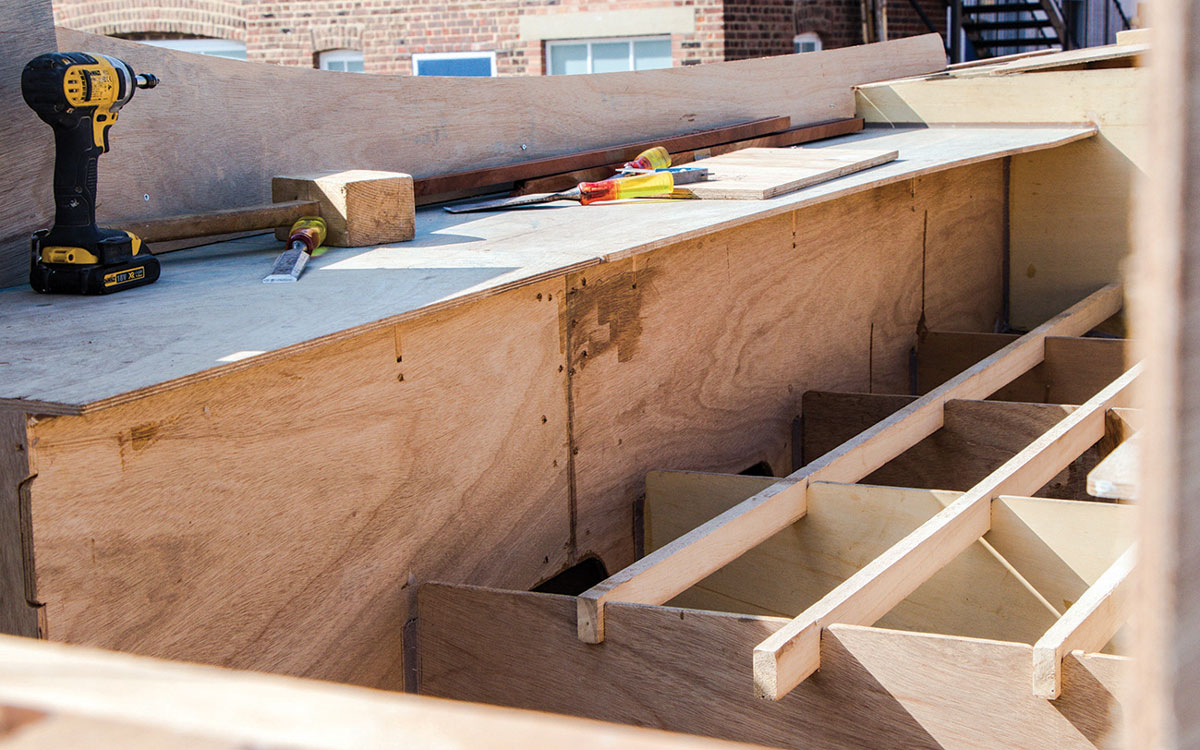
The support the weight of potentially four big sailors, the frames under the cockpit floor support several longitudinal beams. Photo: Jason Brodie-Browne
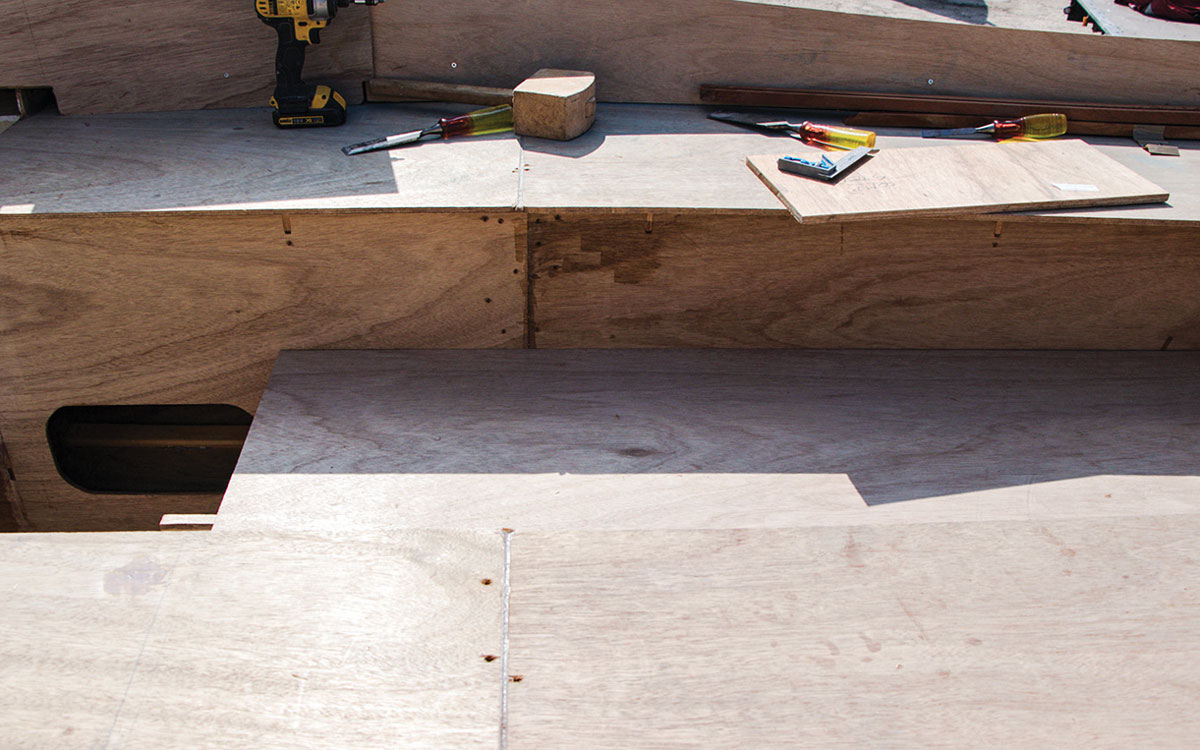
The beams are then covered with 12mm plywood. Once filleted into place, the cockpit sole will be self-draining. Photo: Jason Brodie-Browne
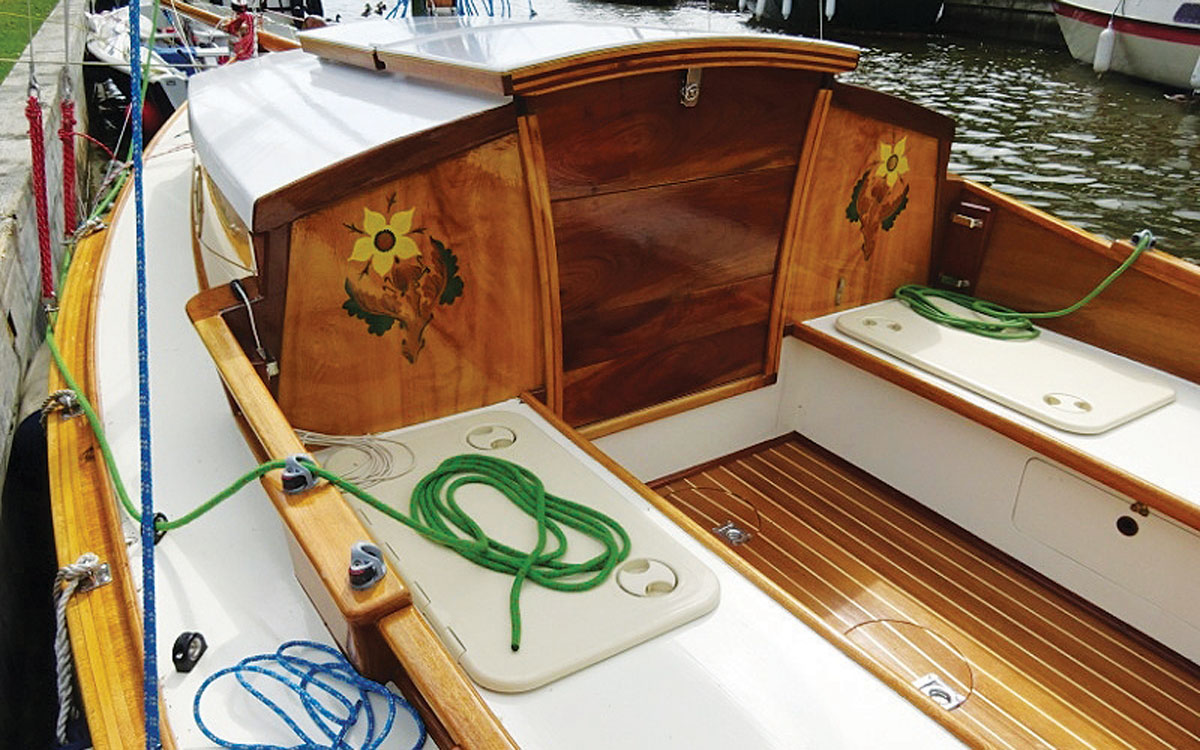
Looking at other build projects, such as this Secret 20 on the East Coast, shows just how some builders have added their own detail modifications to the design