Opting for an eco-friendly approach, Ali Wood tries silicone antifoul on the PBO Project Boat – and is impressed with the results…
Does silicone antifouling work? It’s not flying off the shelves yet, according to suppliers, but the results from our Project Boat are promising. In fact, in the words of the boatyard that lifted Maximus out, “Brilliant. It’s fantastic. Everyone should use that!”
It’s not often we’re so effusive about a new product in PBO, so it’s worth recapping how we came to choose silicone antifouling, how we applied it over a sunny weekend and why a Poole boatyard, located in an internationally important nature reserve, was so impressed.
The story began in the summer of 2021, when we acquired Maximus, our 44-year-old Maxi 84 cruiser. She’d been in a Chichester boatyard for two years and needed some serious TLC. I was keen to test new products, as we restored her to her former glory, and the hull was the obvious place to start.
Marine growth impedes your boat’s performance, so choosing the right antifouling for your hull is essential. Although there are many tried and tested antifoul paints out there, I opted for the most environmentally friendly type.
Eco credentials matter, but our antifouling still needed to perform well; after three gruelling days of hand-scraping the hull to gelcoat, I didn’t want to apply a product that was either ineffective or short-lasting!
Article continues below…
Ultrasonic antifouling tested: 4 cutting edge options for keeping your hull clean
N.B. This article was first published in the January 2015 issue of PBO and some of the products below have…
Best antifouling paint: 8 leading options in head-to-head test
In June 2021 we coated the hull of a Hardy Commodore 42 with eight of the best antifouling paint products.…
Why silicone?
Copper is still the most widely used biocide in antifouling paints. This is released into the water as the coating wears away. Because of this, antifouling is regulated by the Biocidal Products Regulation (BPR) and manufacturers are subject to ever-tightening controls.
We looked at a few different antifouling products including Coppercoat, which is a durable epoxy resin rather than an ablative paint and has a leach rate at one tenth of that allowed in places with the toughest marine biocide restrictions such as Sweden and California.
However, silicone antifoul products don’t contain any biocides. They work in a different way altogether. Antifouls such as Seajet Bioclean and Hempel Silic One prevent fouling due to their super-smooth hydrophilic surface. In other words, the coating is simply too slippery for marine fouling to attach itself.
If your current antifouling is in good nick (i.e. not flaking or peeling) you can use a ‘tie coat’ then apply silicone antifoul on top. However, in our case we would be working from bare gelcoat, so needed to start with primer.
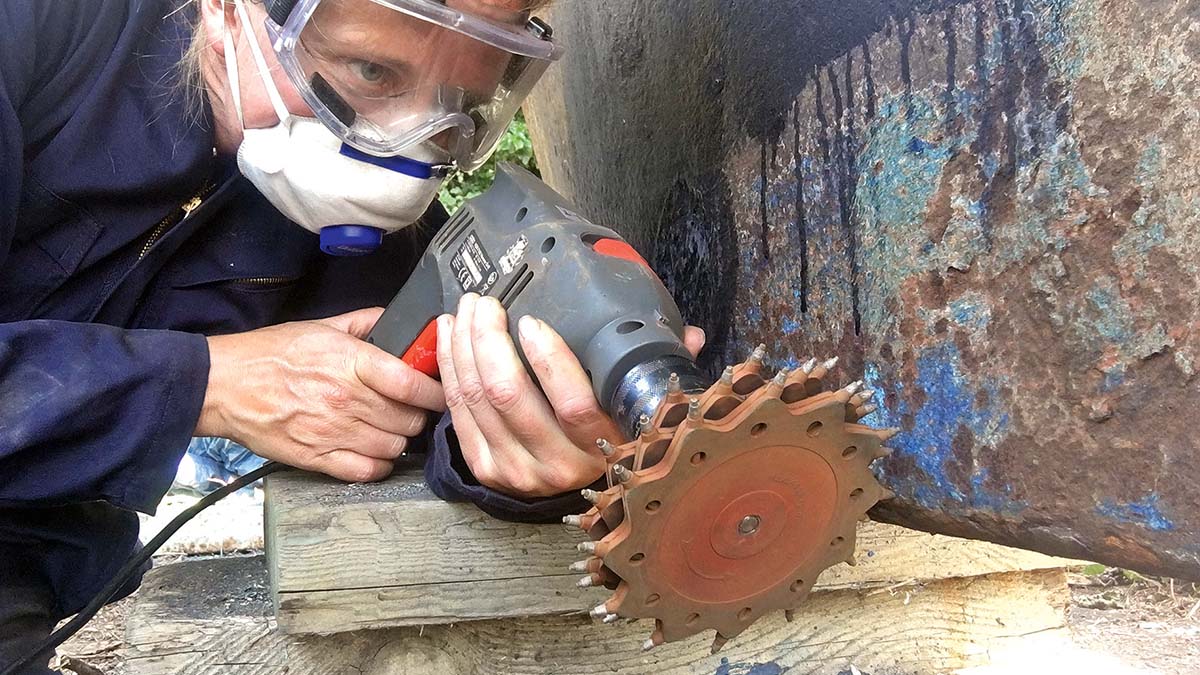
After hand-scraping the antifouling on the keel, Ali grinds away the rust
When to replace silicone antifouling
Seajet expects Bioclean to last for at least three years, after which point, another tie coat and top coats are likely to be needed, although as this was a new product the recommended routine wasn’t yet fully established.
Scraping to gelcoat
When we acquired Maximus she had a mix of incompatible antifoulings, and after several seasons’ applications, the paint was just too thick and needed to come off. Self-eroding antifouling should, as the name suggests, gently remove itself during the year but layers of hard antifouling, and even the eroding type, will eventually build up.
So my husband, James, and I spent the 2021 May bank holiday weekend in full PPE, hand-scraping the hull. It took three days. A shot-blast would have done the job quickly, but we wanted to save money. With hindsight, and especially with the effort required on the keel, I’d have chosen the latter!
After trying many scrapers, the Bahco 665 carbide-edged one turned out to be the best, though I did make a few gouges in the hull, which later had to be filled (top tip – blunt the edges of the scraper first!).
The keel required tougher treatment. After initial scraping I switched to a Tercoo rotary blaster, fitted onto the drill, to grind away the last stubborn bits of rust. I then used Fertan rust converter before applying primer.
Applying silicone antifoul
With the antifoul being so new to market, it was a few weeks before we obtained the samples of Seajet Bioclean. We headed for the boatyard, not realising just how involved the process would be! In total, we needed 3lt of Seajet 117 epoxy primer, 6lt of black Seajet Tie Coat and 5lt of Seajet Bioclean Eco, which altogether retail at around £650.
Getting the timing right was crucial. If applied too soon before entering the water, antifouling can break down prematurely, but on the other hand, if applied too close to launch it wouldn’t have time to dry.
Most antifouling coatings require a minimum of eight hours to dry, but that depends on temperature and humidity. Leaving it for a day is a safer bet.
Weather conditions also factor into the mix; if the surface of the hull is wet, or if it’s reaching dusk and you find yourself within 4° of the dew point, you risk unsuccessful application. At best this means patchy paint, at worst it means it doesn’t stick properly and starts to peel.
Unusually, we applied Maximus’s antifouling in the middle of a heat-wave. In 28°C the pot life was dramatically reduced, and we had to be quick with the application. However, it did mean quicker drying time between coats.
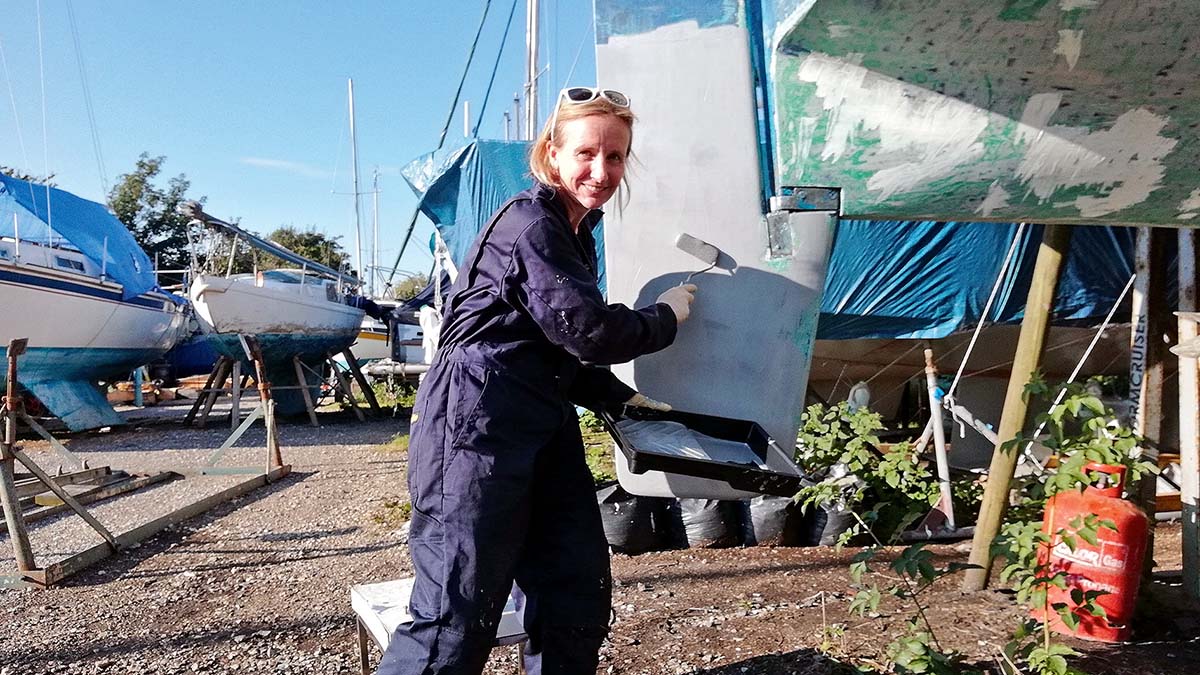
Priming the rudder. We had to work fast because the paint was curing quickly in the hot sun!
Applying primer first
Initially Seajet advised applying three to four coats of primer. However, with the thick covering provided by a 12in mohair roller, we found two coats was enough to achieve the desired 180 micron thickness. It took around 45 minutes to coat our 28ft hull, with two hours’ drying time required in the hot sun.
Next step: tie coat (x2)
We were given a black tie coat, which is an important detail as the Bioclean Eco antifouling is translucent. Whichever tie coat colour you choose will therefore be your final hull colour. There’s also a white, navy blue and red tie coat option depending on your preference.
Again, we used the 12in mohair roller, with a 1in brush for the tricky areas. The Seajet tie coat went on smoothly, and took around three hours to dry before we could apply the second coat. However, we needed to leave 12 hours before the final step, applying the silicone antifoul.
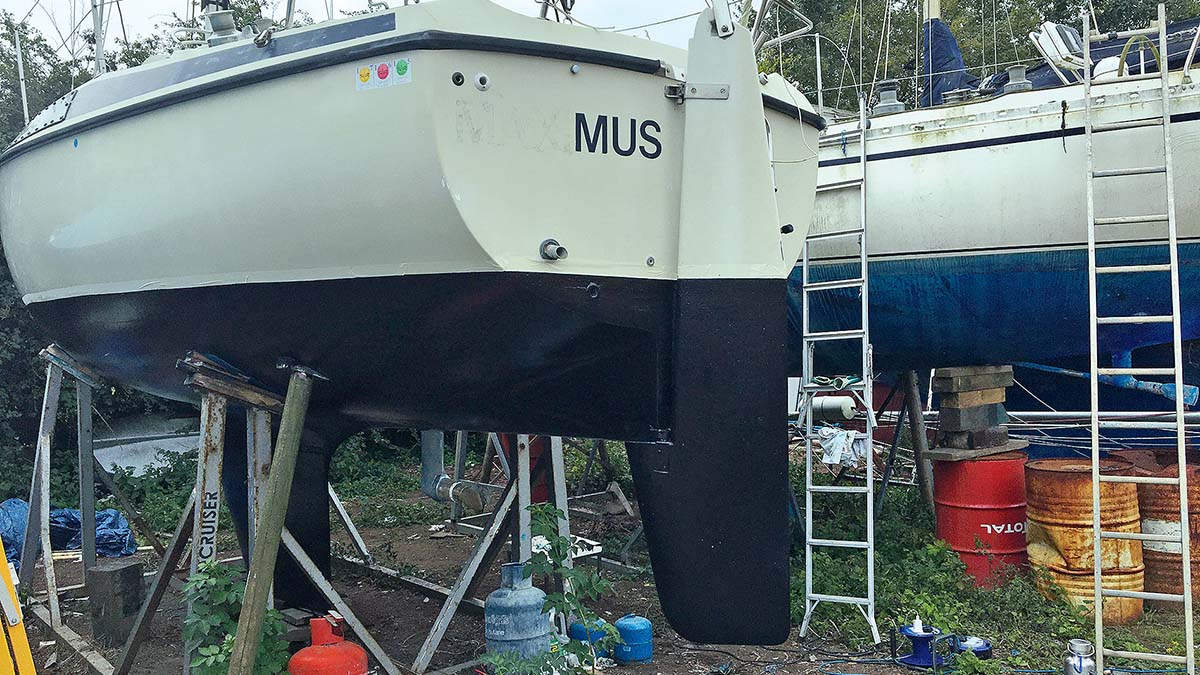
Maximus looked smart with the tie coat on
Antifouling coats (x2)
Being a thick, translucent paste, the Seajet Bioclean antifouling was quite different to how we imagined. It had a pleasant smell too. The texture made it easy to work out what had already been done, and application was straightforward (again with a mohair roller).
It took 45 minutes to apply each coat, with three hours’ drying time. We then required a further 24 hour drying time before launch.
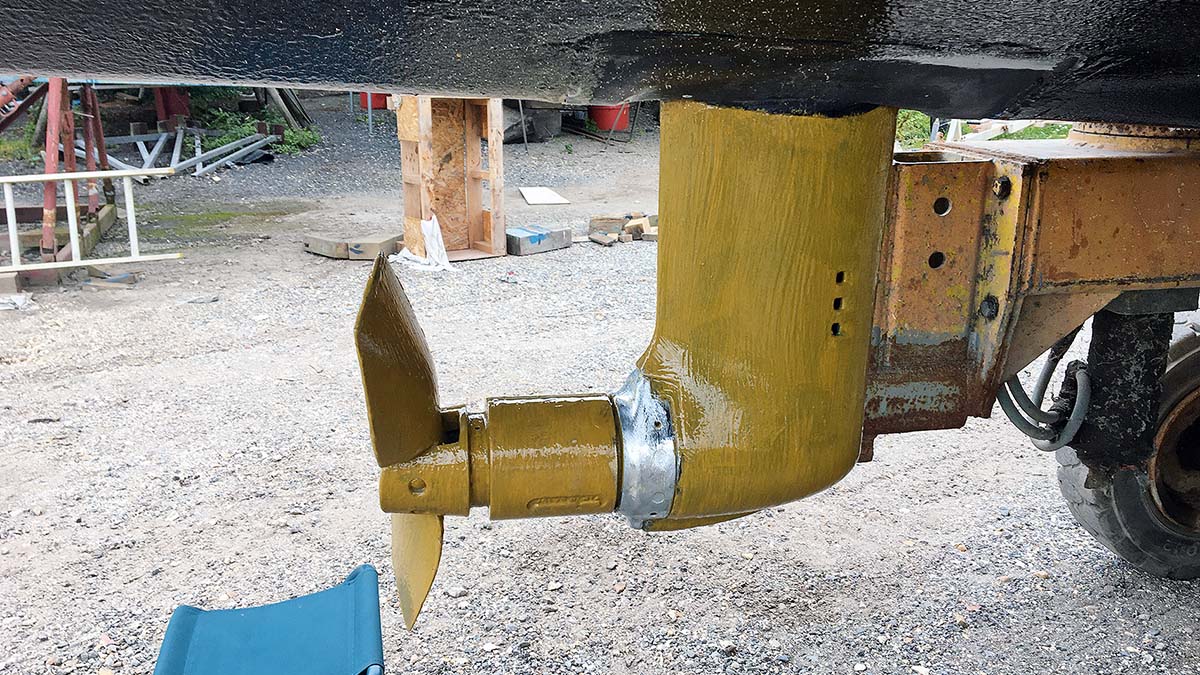
The gold Pellerclean is on and one of the two anodes
The metalwork
Maximus has a Volvo saildrive engine, and the saildrive has an aluminium leg and bronze propeller. We had to treat this differently to the rest of the hull, so Seajet supplied us with Pellerclean propeller antifoul for protecting the saildrive.
Pellerclean (£72 for 1m2 coverage) is the environmentally friendly alternative to Seajet’s Triple Pack self-polishing coating (£32 for 2.5m2 coverage). It has an epoxy primer base coat and silicone top coat, and protects shafts, rudders, struts, trim tabs and props against fouling in both fresh and salt water.
We sanded the saildrive back to gleaming aluminium, and used our Bahco scraper for hard-to-reach areas. The kit, which comprised a primer base, primer hardener and a Pellerclean topcoat, was straightforward.
However, just as with the antifouling, you need to leave sufficient time between the two coats of primer and three coats of Pellerclean topcoat; eight hours after the first application, you’re good to go. Tip – don’t paint over the anodes; that cost us another hour’s elbow-grease cleaning it off with wire wool!
Patching
If ever you want to test the efficacy of antifouling, take a look at the bits you didn’t do! As instructed, we left clear the rubber diaphragm on the saildrive leg. The purpose of the diaphragm is to protect the fastenings above (which attach the leg to the gearbox) so marine growth is expected here. However, the areas we’d have liked to have done were the square patches under the side supports from the fixed cradle.

Seaweed under the keel, which we couldn’t reach when antifouling
This was a bit of a dilemma, so Dell Quay boatyard kindly agreed to leave Maximus in launching straps the weekend before launch. This exposed the old patches, so we could get to work on them. When I told Seajet this, the firm warned there would be ‘no guarantees’ for the patches applied later. However, we were out of options.
With no time to scrape back to gelcoat, we hand-sanded the old antifouling, then applied just one coat of tie coat, followed by two coats of the Bioclean Eco silicone antifoul. This was the best we could do with 12 hours’ drying time.
How did the silicone antifoul fare?
Sixteen months after launch, it was time to lift Maximus out. She’d spent two winters in the water – one at Premier Marina, Chichester and the other at MDL Cobb’s Quay Marina in Poole. We were keen to find out how the antifouling had performed.
We had high hopes because Seajet Bioclean had worked well in our short group test of eight antifouls on Raymarine’s Hardy Commodore 42 Raymariner.
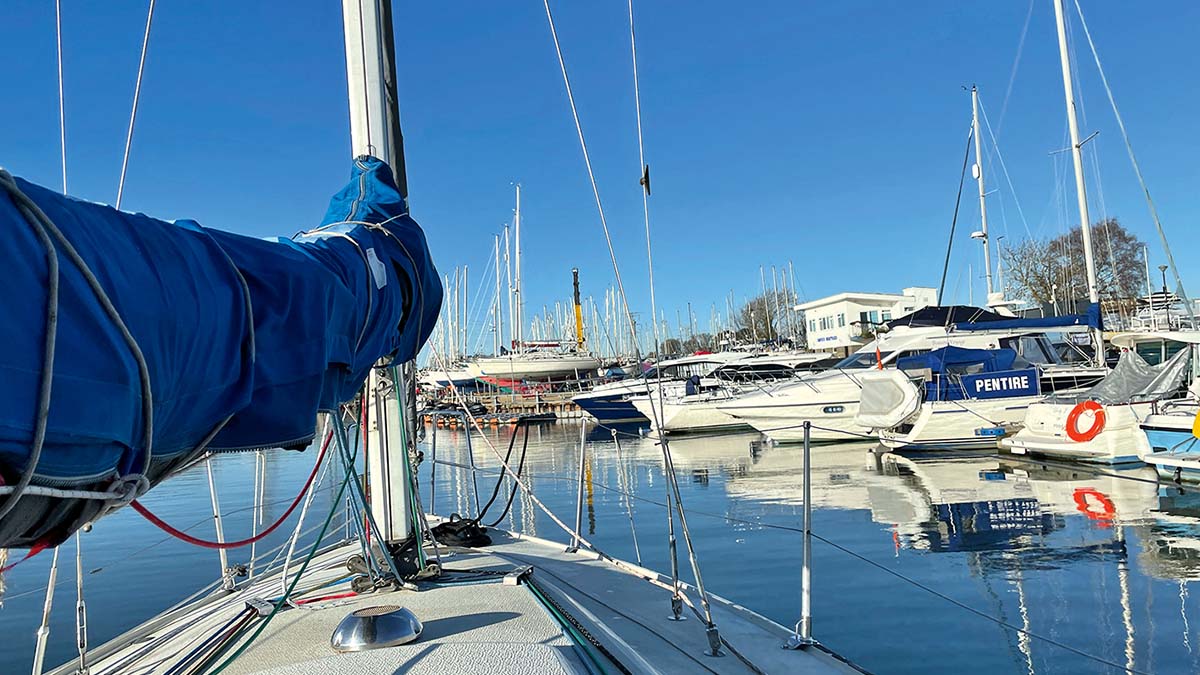
Motoring from Cobb’s Quay round the corner to Davis’s Yard
What to expect
After a chat with Seajet, we’d been warned to expect a degree of fouling simply because the boat had been static in the marina. A flow of seawater against the hull is crucial to detach fouling from any brand of antifouling, so inactive boats and those cruising below 5 knots would require a quick wash.
We’d also been warned that the hull would be slippery (which, of course, is the point of using silicone-based products). Seajet advised using grease-free paper or wet towels in between straps to prevent damage. Straps could be tied together so the boat doesn’t slip; there are tricks for every cradle.
Dell Quay Marine had experienced no problems launching our silicone-coated hull, and we hoped that the lift-out at Davis’s Yard in Poole would be equally trouble-free.
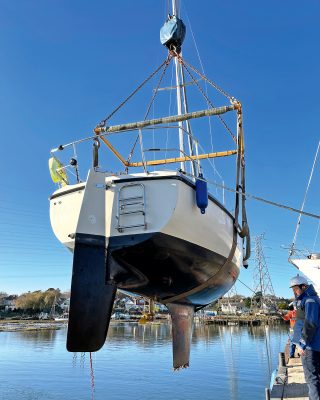
Maximus is lifted out on strops at Davis’s Yard in Poole
Excited, but a little nervous, James and I waved goodbye to our lovely pontoon of liveaboards. We slipped our lines at Cobb’s Quay under a crisp, cloudless winter sky, and reflected that we’d much rather be going sailing than lifting out, but alas, our marina berth had come to an end.
Four cormorants sunned themselves on a half-sunk dinghy as we motored around the fringe of Holes Bay nature reserve. It took barely five minutes at 3 knots. We’d otherwise been ‘static’ since September, so I expected to find at least a couple of months’ worth of fouling on the hull when we lifted out.
When we pulled up at Davis’s Yard, we got a warm welcome from Barry Murdoch and son Dean. They helped us to remove the backstay so it didn’t get caught during the lift.
Dean then checked the weight of the boat; anything under 4.5 tonnes can travel on the crane, anything over needs to be towed. Maximus weighed 3 tonnes, so well within crane limits.
We warned Dean that Maximus had silicone antifoul, and he said it shouldn’t be a problem. In fact, he was keen to see the results himself as he’d heard customers talking about it.
As we waited for the straps to go around Maximus’s hull, Dean told me all about the family-run yard, established by his grandfather Lloyd Davis in 1964.
“I remember sitting on his knee as he drove around in a steam roller levelling out the yard,” said Dean. “We used to get told off for throwing stones in the creek when they’d just spent god knows how much getting it dredged!”
Lloyd reclaimed the marshland and sheet-piled it in order to open his very first berth. With the money from that he built a second berth. Now Davis’s yard has 82 pontoon berths and dry storage for up to 250 vessels.
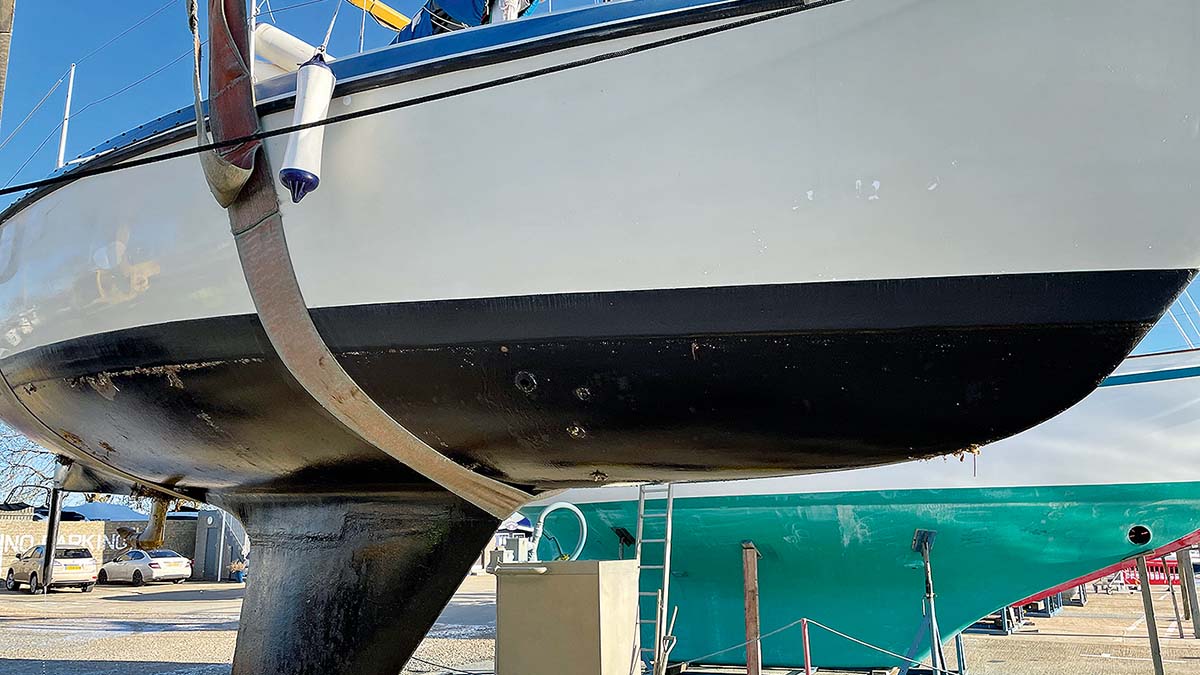
Maximus looking remarkably clean and ready for a mild pressure wash
Lift-out results
It was Maximus’s turn to be lifted. The Mobile 360 crane nosed forward and lowered a square yellow frame over the coachroof. Dean and first in command, Richard Walker, attached two wide straps to the crane hooks on the starboard side, then passed them under the hull and reattached them to port. Slowly, the crane lifted Maximus, and her shiny black hull emerged from the water.
“Look at that!” exclaimed my husband James. As water dripped from the sleek black hull, we realised there was barely any fouling. In fact, the silicone antifoul looked good as new, except for the patches where the side supports had been, the saildrive diaphragm and the bottom of the keel.
A steady trickle of water poured out of a hole at the bottom of the rudder, which would need filling with epoxy when dried. Maximus was perfectly secure as the crane reversed. Dean wiped his fingers over the tiny patches of fouling, and walked away nodding his head. “Comes off very easily,” he said. “In fact, we’ll do you a half-price jet wash.”
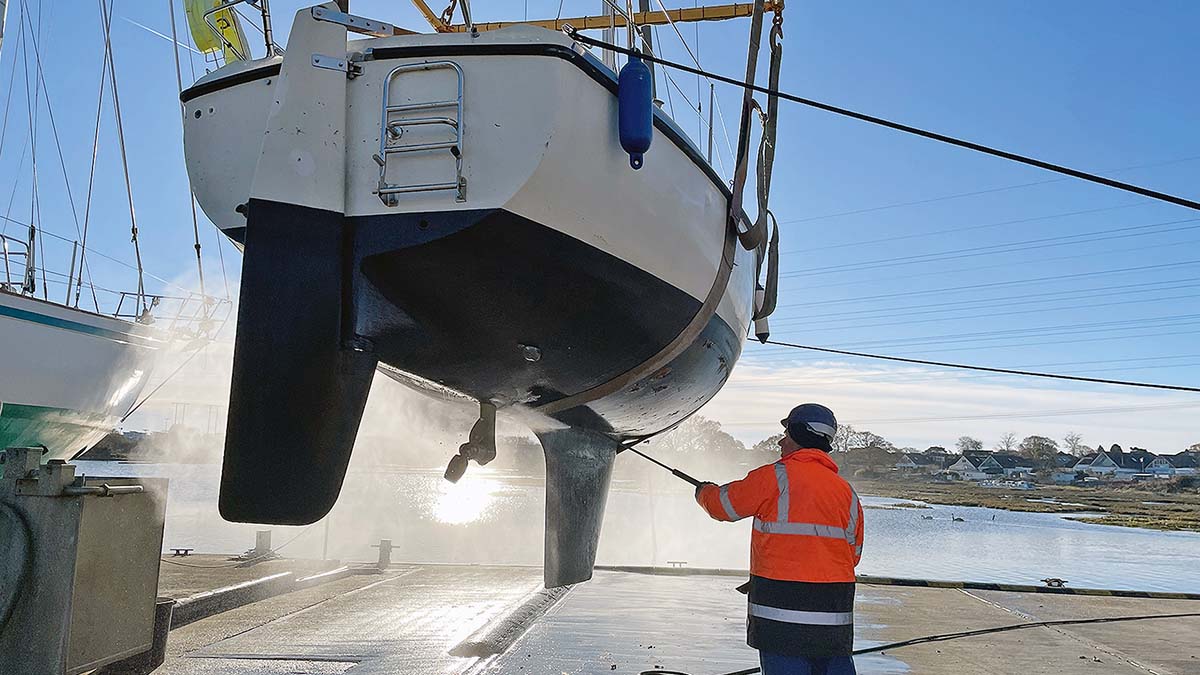
A quick jet wash loosens the tiny bits of fouling
Pressure wash
Davis’s Yard policy is that all boats have a high-pressure wash on being lifted. Poole Harbour is the largest microtidal estuary in Britain and Davis’s Yard is on a Site of Special Scientific Interest (SSSI).
Because of this, the high-pressure wash takes place in a loading bay where any loose paint gets pumped through a filtration system, coagulated and collected in filter bags. In order to maintain their dredging licence, the yard regularly has to provide mud samples.
Poole Harbour is one of the few SSSIs with an important sub-tidal habitat, and Holes Bay is home to dense forests of peacock worms. “I’ve never seen the worm myself, but apparently it doesn’t live anywhere else in the harbour,” says Dean. “We’ve got so much wildlife. We’ve had a clutch of cygnets born this year, which we’ve been watching develop.
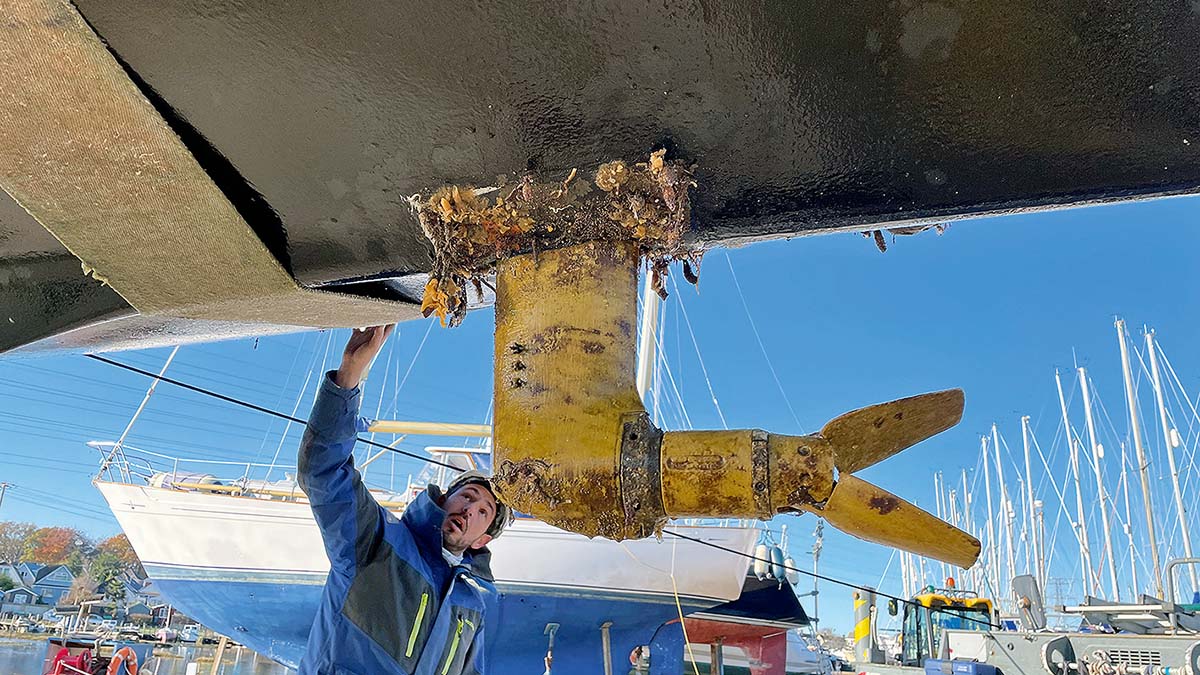
The Pellerclean did a good job on the saildrive leg. Note the fouling around the rubber diaphram
“We have cormorants, egrets, Canadian geese and starlings. Kingfishers are the best; you see a little flash of blue going up the creek. It’s only ever for a split second, but it’s brilliant when you catch them.”
Our conversation was drowned out by the noise of the pressure washer, as Richard got to work hosing down the hull. A rainbow shone through the fine mist, and just a few lonely strands of seaweed fell off the keel. Small blooms of algae came away easily from the patches . The tiny remnants could later be removed with a paint scraper.
The most heavily fouled part of the boat was the saildrive diaphragm. The forest clinging to it was more than enough proof that the antifouling had done its job elsewhere. I asked Richard how Maximus compared to the other boats he washed off. “It’s a lot cleaner,” he said. When I told him how long we’d been in the water he was astonished.
“It’s fantastic, everyone should use that!” In fact, he went as far as to suggest we should get rid of self-polishing antifouling altogether.
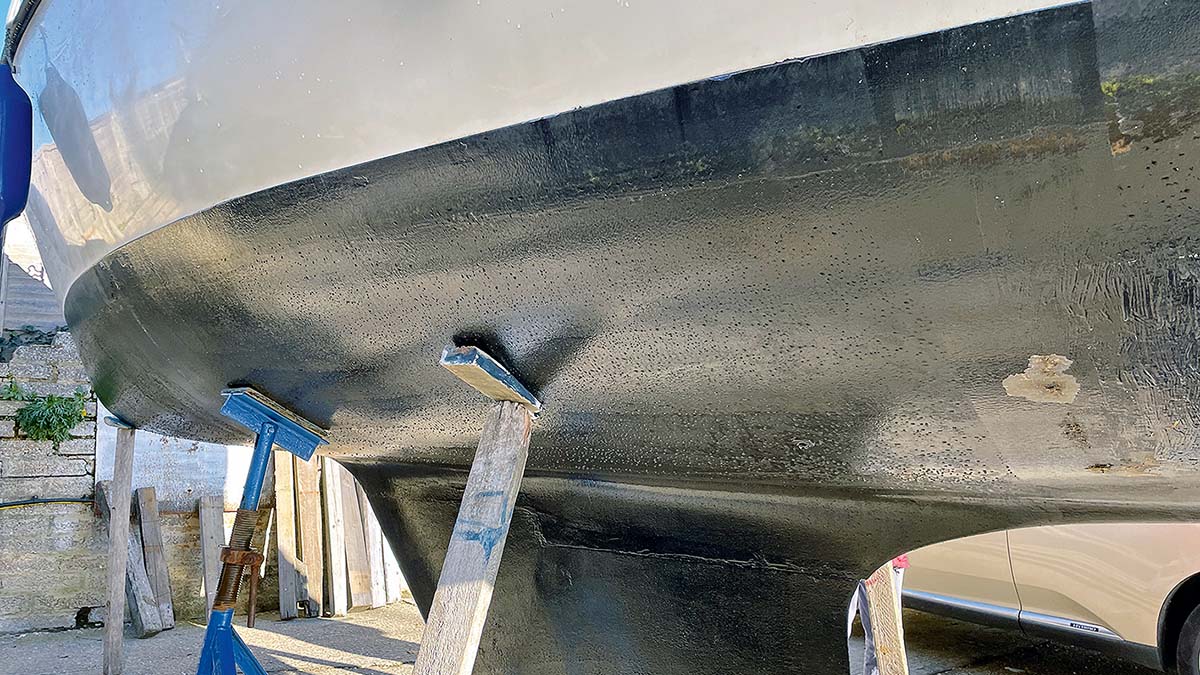
Maximus is snug for the winter with a shiny looking hull
Positioning Maximus
After the pressure wash, Maximus was transported by crane to her new home outside the office in Davis’s Yard. “This type of crane is very versatile,” explained Dean. “Not only do we use it for lifting boats, but for hauling out engines and re-stepping masts.”
He held onto the rudder as Maximus was lowered into position on the cradle. “We always use the position of the rudder to check the boat’s true,” he said. “Not the mast, as that can often be tensioned more on one side than the other.”
Most boats drain from the cockpit, so are tilted slightly aft, though occasionally they need to dip them forward. “If you’re not sure how it drains, throw a bucket of water in the cockpit,” said Dean.
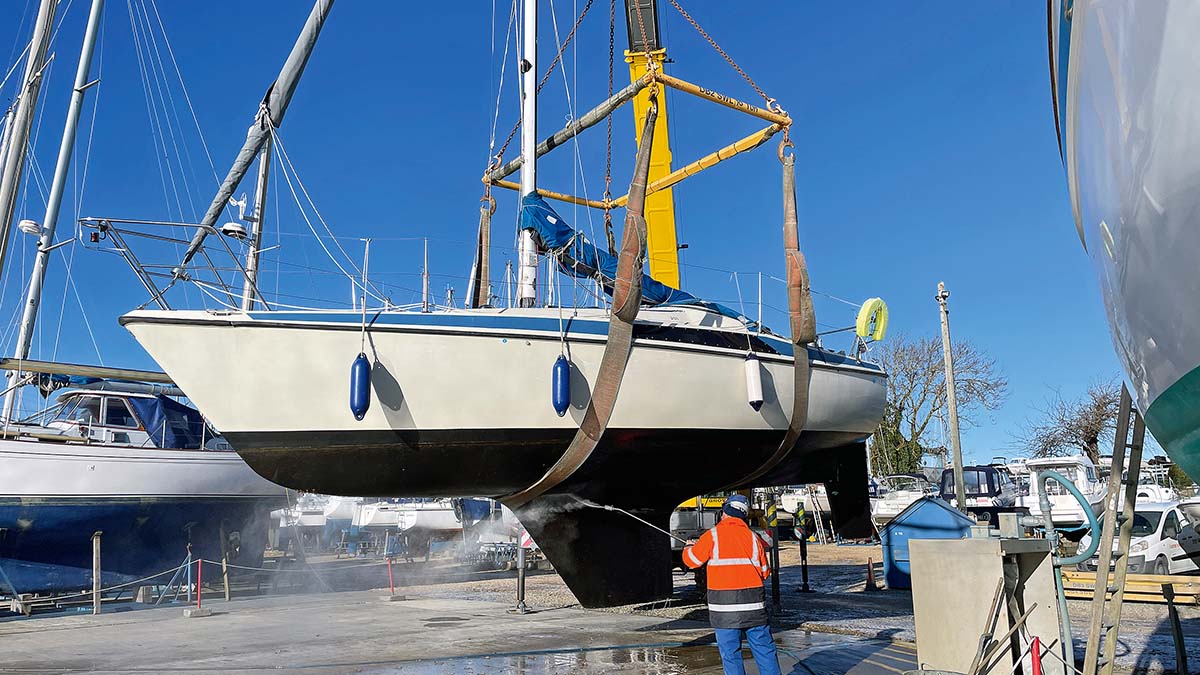
Richard gives Maximus a jet wash, though very little pressure is required
Dean gave them the all clear, and the crane straps were released, leaving Maximus’s keel to take the weight. The cradle is just there to offer side support. “It’s a fixed cradle, and we make them here on site,” said Dean. “Nothing’s going to wobble. However, you do want a tiny bit of movement so you know there’s not too much pressure on the hull.”
Once Maximus was fixed in position, we were free to move around as we liked. However, Dean warned us never to try and remove the supports. “If you need to move them to repaint or anything, go into the office and speak to a member of staff,” he advised.
Preparing for winter
With Maximus snug and secure in her winter home, we removed the berth and cockpit cushions, and plugged in the 45W Victron solar panel to keep our three Exide 115A dual batteries topped up when the sun was out.
Our marine electrician, Adam McMenemy of ACM Marine, advised that this way of ‘exercising batteries’ was much better than keeping them permanently charged on shore power. However, should they run too low, I could always buy a card from Davis’s Yard and plug in to the mains.
I popped back occasionally over the winter to check on the boat. When I checked the battery voltage on the Victron Smart Monitor it varied between 12.7V (which is fine for a non-charged battery) to 13.75V on sunny days.
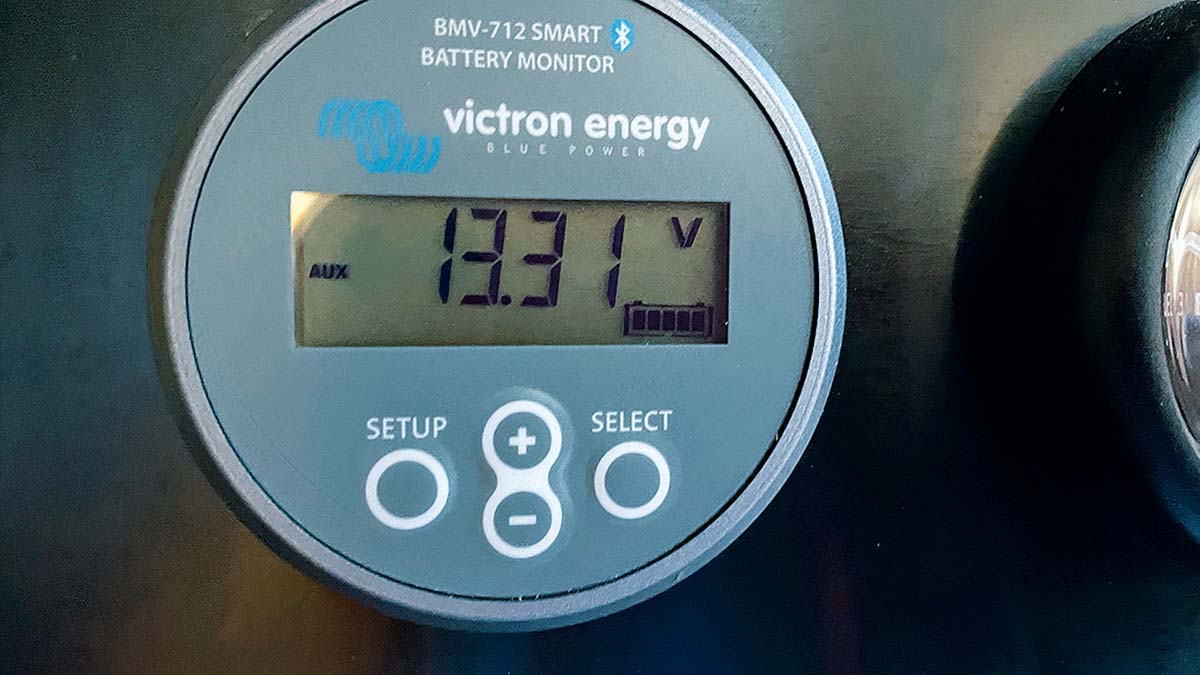
The battery monitor reads 13.31V – not bad for a winter sunshine top-up in early 2023
I also left some packs of BirchSorb desiccant around – a product designed for shipping containers, which has an absorption rate three times its own weight in moisture – to keep the cabins dry.
Last winter, when we were alongside at Cobb’s Quay, I plugged in two 135W energy saving tubular heaters from TLC Heating. These use less than 50W per foot– similar to an ordinary lightbulb – and have a heat-safety cut-out.
They don’t keep you warm, but they do protect against frost and reduce condensation. This, together with the work we’d done resealing windows and deck vents, was enough to keep the water out. Each time I returned to Maximus, I expected to find a puddle or smell mildew, but she was surprisingly dry, and smelled fresh.
This year, however, I didn’t want to use shorepower at all, so decided to see how we’d get on. Again, Maximus stayed reasonably dry, though the windows were damp with condensation and a cockpit cushion I’d accidentally left on board gathered mildew. To a degree, this is inevitable, and on the plus side we were using no mains electricity, just solar power.
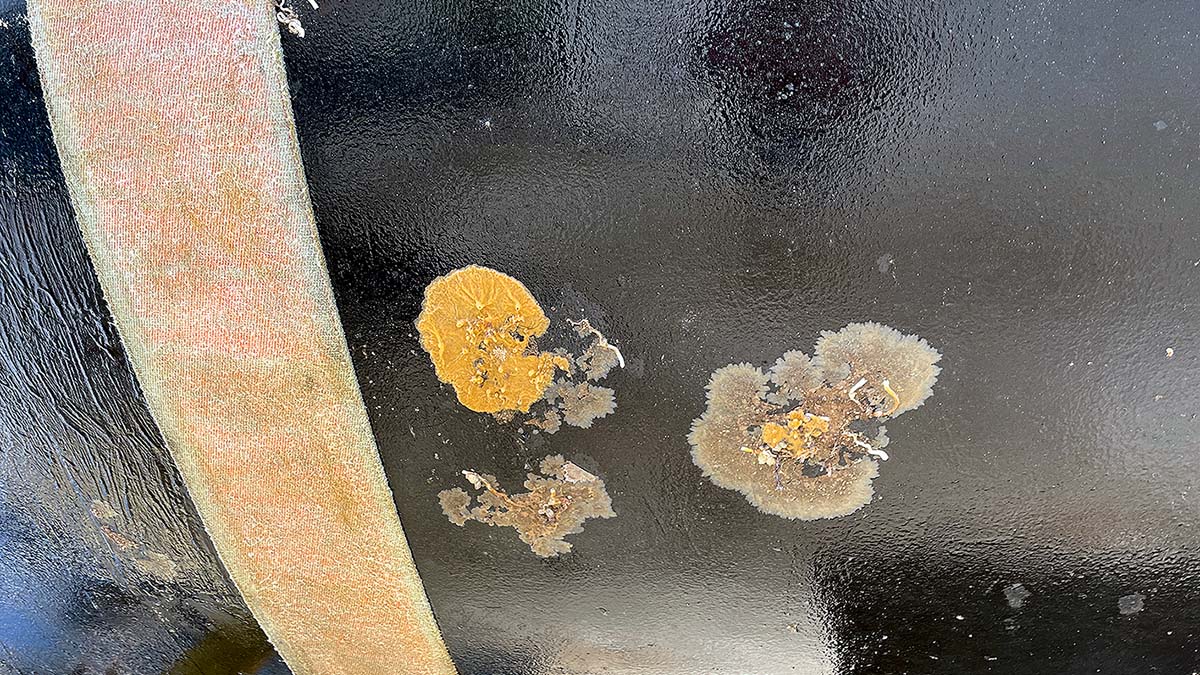
Small patches of marine growth where Maximus was originally chocked
Topping up the patches
As spring approached we decided it was time to top-up the patches where we’d originally applied less antifouling. Maximus was now in a different position in her cradle so these could easily be accessed.
Sander Koole, technology manager at Seajet, sent us some advice on how to repair damaged spots. There was one small patch on the rudder where the silicone antifoul had scraped back to gelcoat.
For this, he said to roughen the surface with sandpaper, clean it with thinner and apply Seajet 117 epoxy primer (2.5lt = £79), followed by the tie coat (2.5lt = £112) and then the Seajet Bioclean Eco (750ml = £110).
Unfortunately, we didn’t have the primer, so tried applying the tie coat thickly on this spot. It didn’t go on easily, tending to slip off, so we’ll see how it fares. The patches, which were originally under side supports, already had old self-polishing antifoul underneath the silicone, so application was much easier, and the tie coat adhered well.
It did strike me that £301 is a high cost for covering such a small area, and once the tins are opened they will start to cure, so you can’t re-use them at a later date. Seajet confirmed to me that it is looking into making a ‘repair set’, and Seajet Bioclean is also now available in 250ml cans; tie coat in 750ml cans.
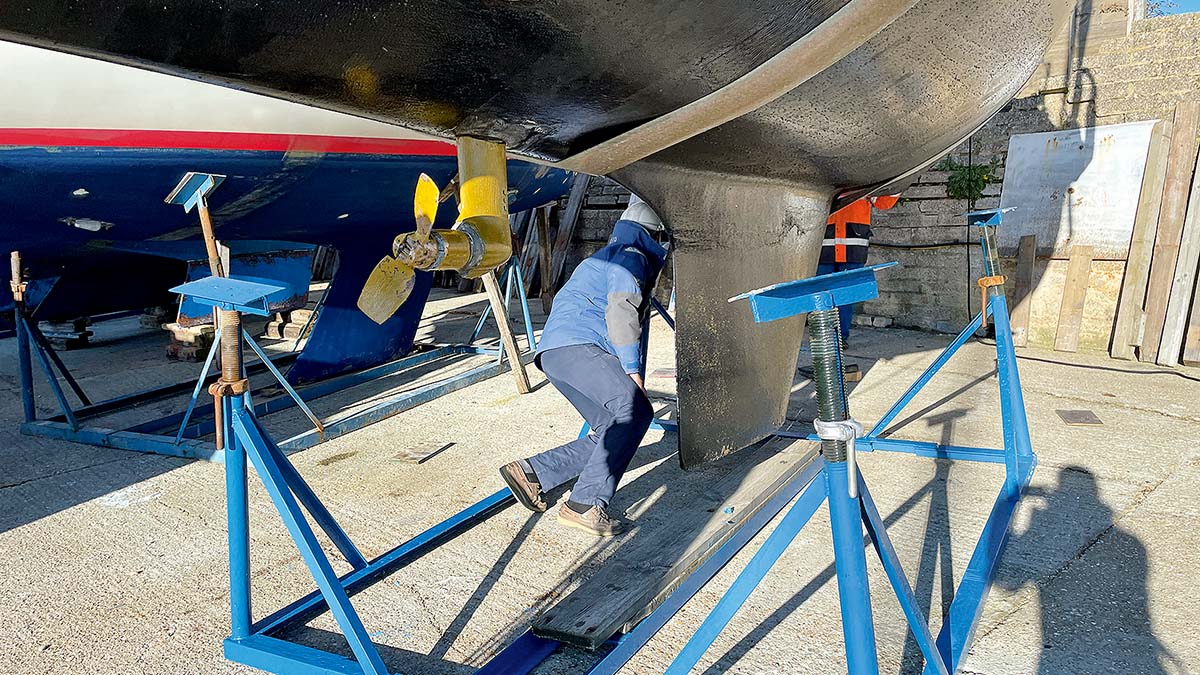
Spring ‘23: Maximus is lowered onto a fixed frame, built by hand by the staff at the yard
Compatibility
I asked Sander if you can apply a different brand of silicone antifoul over the top of an old silicone antifoul. He said no, due to the different resins and solids. You can apply coats of Seajet Bioclean Eco over each other, with no tie coat needed; make sure the hull has been properly cleaned first.
If you want to apply silicone antifouling over old conventional antifouling, you will need to apply a tie coat first before application to ensure adhesion between the old and new system. “Silicone doesn’t mix with normal paint. The different surface tensions will result in bad adhesion and fisheyes throughout the applied coating,” said Sander.
Prop and saildrive leg
Next it was time to re-do the propeller and saildrive leg. The sacrificial anodes had done their job nicely, so that the pitting was contained to the anodes, leaving the metal in good condition. The Seajet Pellerclean had also performed well, leaving very little fouling, but it had worn away in patches and the whole lot would need replacing.
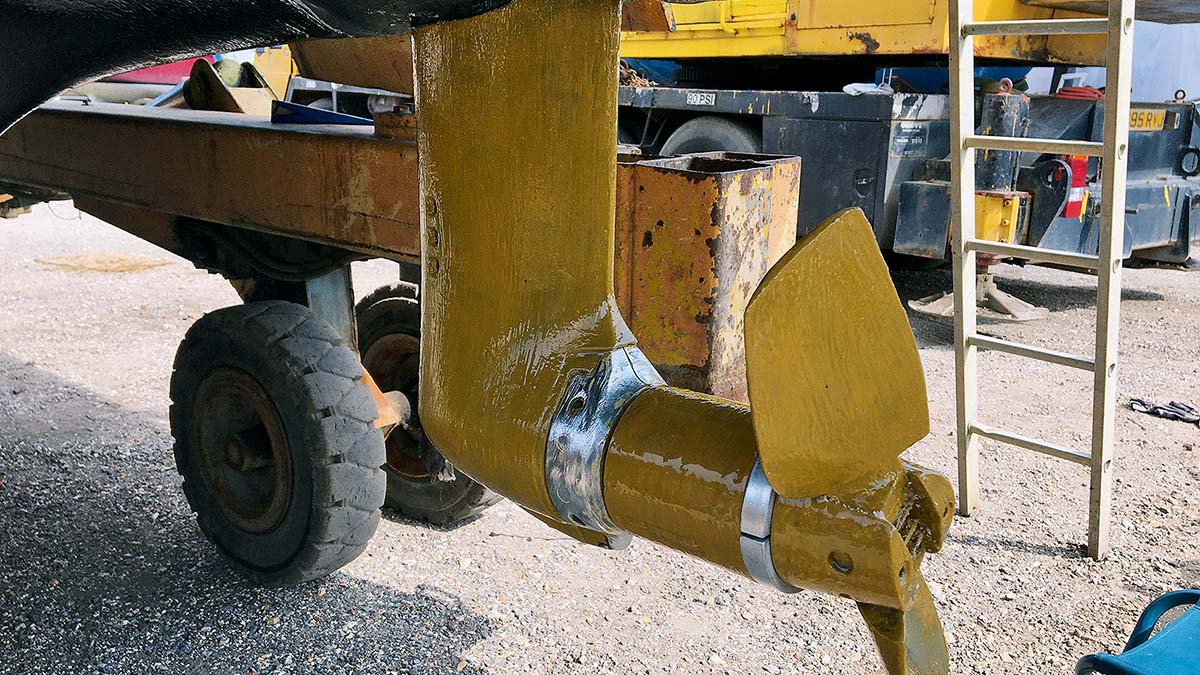
The Pellerclean and anodes had done a good job protecting the saildrive leg and propeller
I had a chat with our engine expert Stu Davies, and he pointed out that he’s tried many brands of antifouling for metal, and has never found anything that keeps the beasties off! It’s just an annual job you have to do.
At twice the price with half the coverage of Seajet’s Triple Pack, you do pay a premium for the eco credentials of silicone-based Pellerclean. However, there was not a lot of area to cover, and given that Maximus now lives in an SSSI, Pellerclean seemed like a good idea.
Sander advised us to sand back to the substrate and build-up the full Pellerclean system again, otherwise the primer wouldn’t adhere properly. The old coating came off easily when hand-sanded with 80-grit sandpaper (tip – bring lots of sandpaper as the silicone gunks it up quickly). Application was straightforward with a paint brush.
Conclusion
After 16 months in the water, Maximus’s Seajet Bioclean Eco silicone antifoul was as good as new, apart from the patches where we’d not been able to apply the recommended number of coats. However, even here, the light covering of weed came off very easily.
The non-antifouled areas around the saildrive diaphragm and bottom of the keel were proof that there was an abundance of fouling in Poole Harbour, so the silicone antifoul had certainly done its job well on the rest of the hull.
At £301 for the standard-sized tins, the full cost of patching would be expensive. We skipped the primer on a very small patch of gelcoat on the keel, and may well lose the paint here due to poor adherence. However, the tie coat worked well over the patches of old antifoul topped with last year’s silicone.
How to apply silicone antifoul: Step-by-step guide
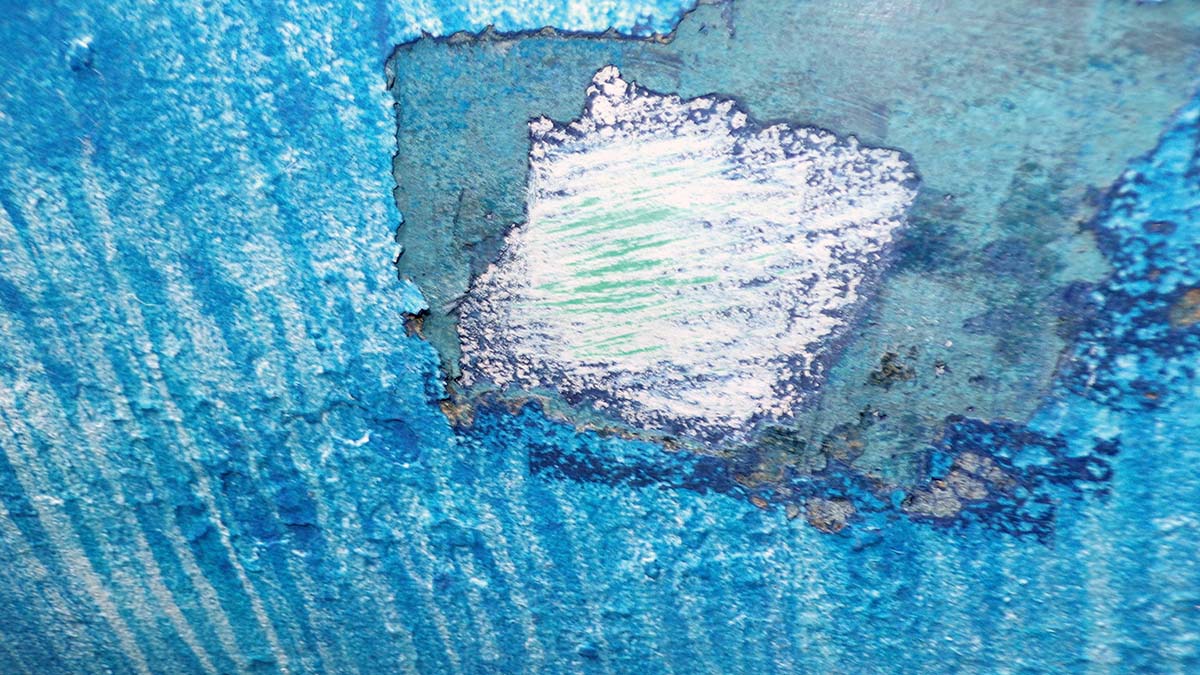
1. The original self-polishing antifouling is flaking away.
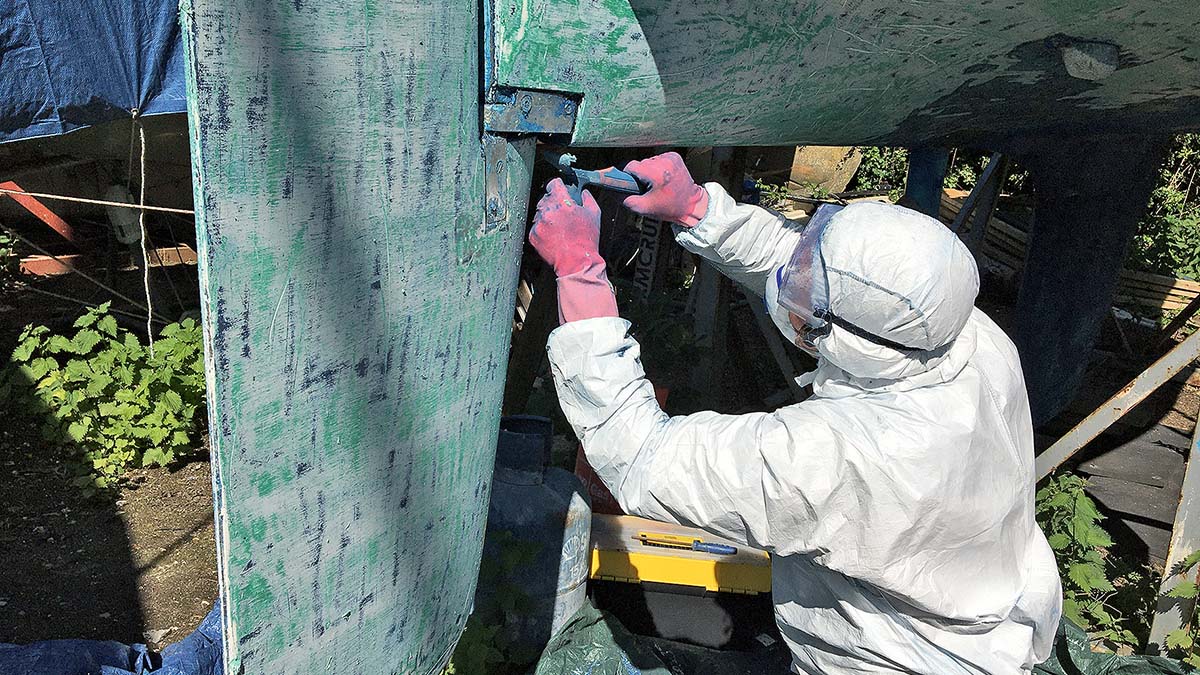
2. James scrapes Maximus’s hull with a two-handed Bahco scraper.
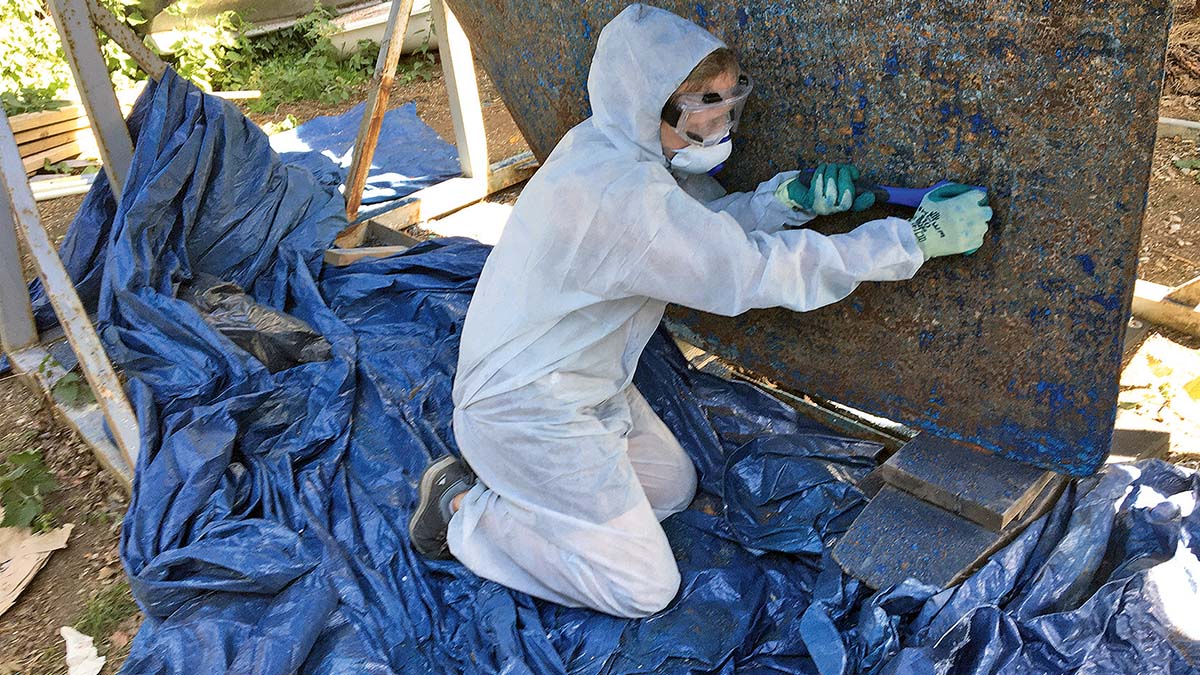
3. Ali gets to work scraping the antifouling off the keel.
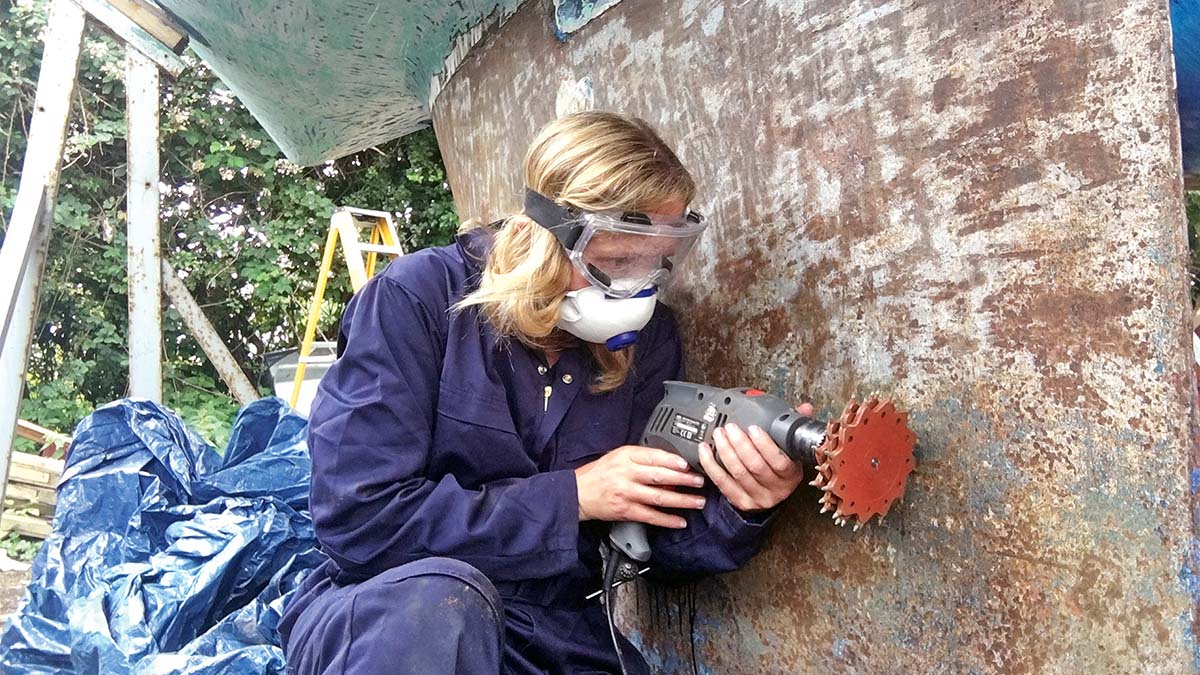
4. After hand-scraping the antifouling on the keel Ali grinds away the rust.
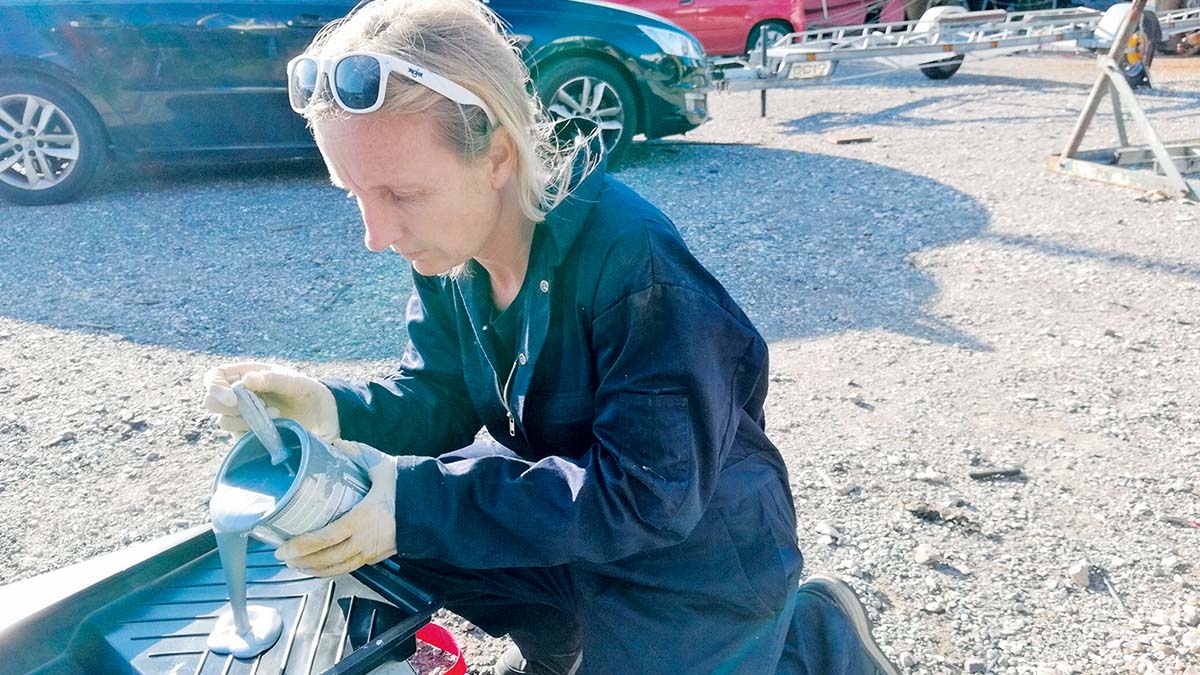
5. Preparing the primer – it has to be applied quickly on a hot, sunny day.
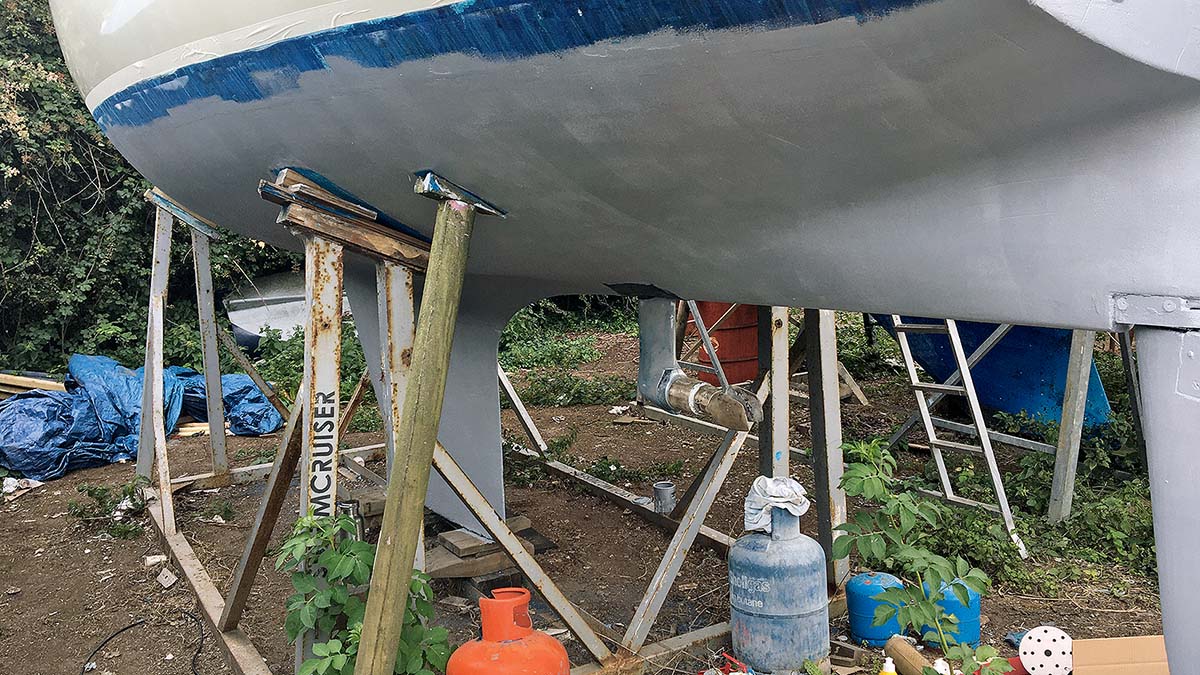
6. The primer is on. Next step is the black tie coat.
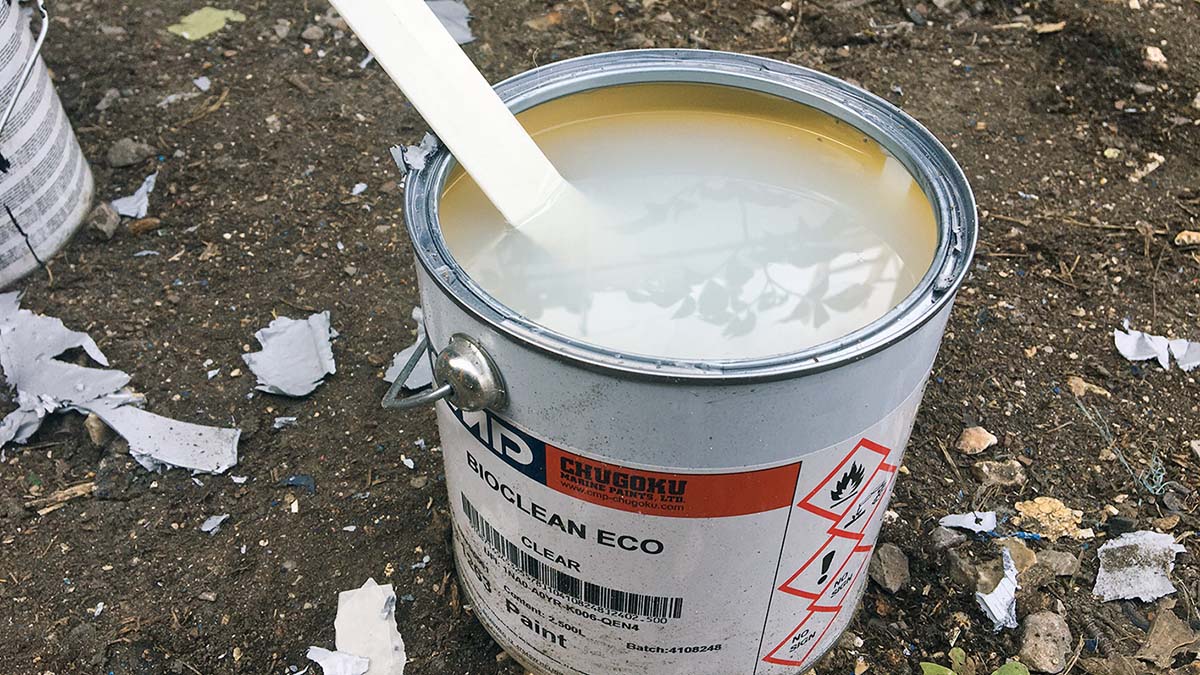
7. Bioclean Eco antifouling is clear and goes over the black tie coat.
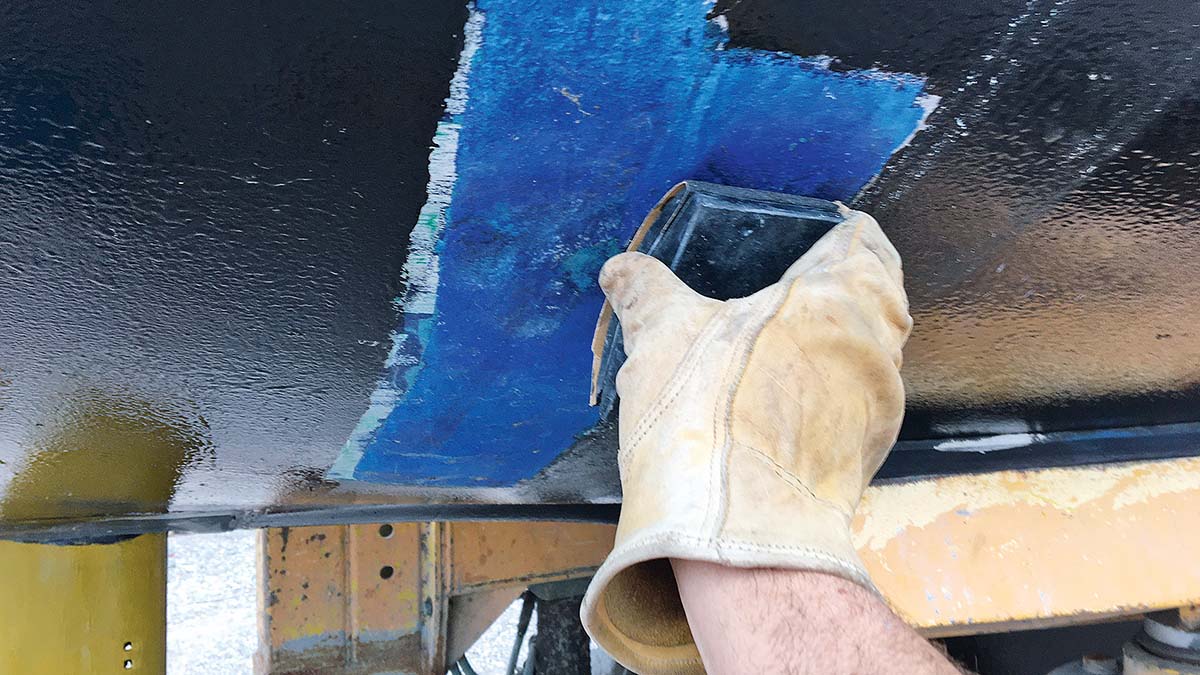
8. With Maximus on the crane we have 24 hours to work on the patches.
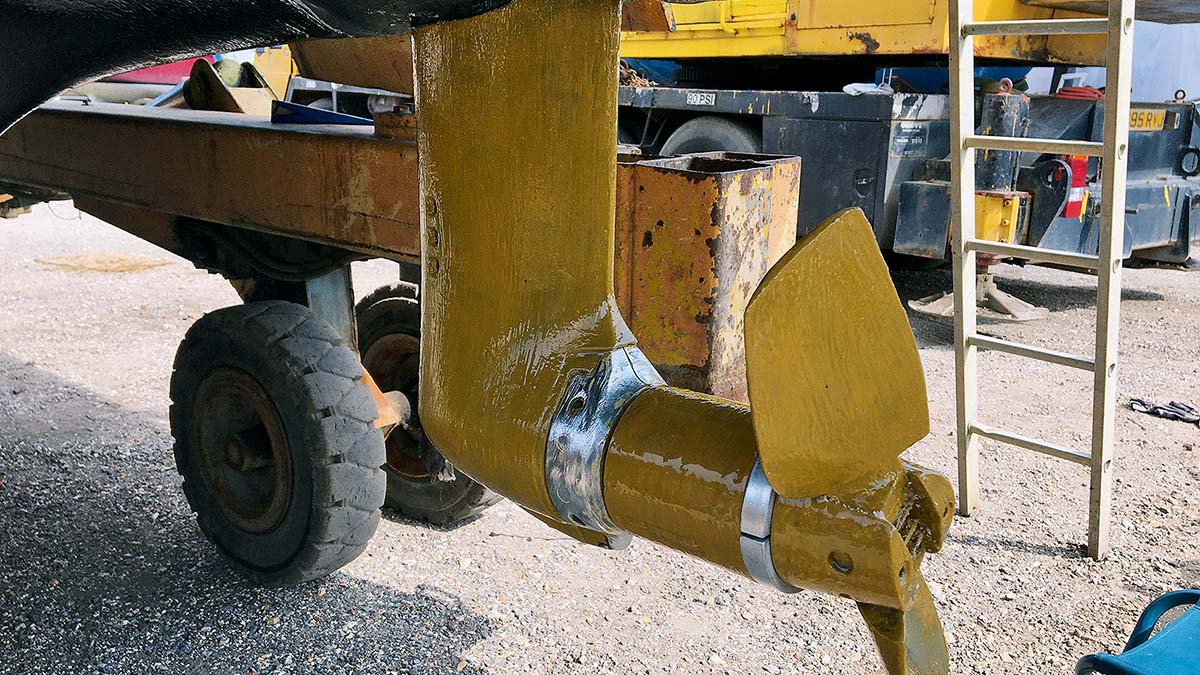
9. We apply Pellerclean to the metal work and replace the anodes.
Will marinas accept silicone antifoul?
We were recently contacted by a Beneteau owner from Essex who was refused a liftout at a Yacht Haven marina because of his silicone antifoul.
“Yacht Havens, with nine marinas, said they will not lift any boat with Hempel Silic One,” said the reader. “This now makes the choice of responsible green antifouling limited. Would it be possible to look into this?”
We got in touch with Yacht Havens and several UK marina groups to see what their policy is on silicone antifoul.
Change of heart
We’re pleased to say that Yacht Havens collected feedback from their boatyards and reviewed their policy. “All Yacht Havens boatyards can lift boats with Silic One or silicone antifoul,” said group marketing manager Jonathan Cook.
“As with all vessels, the boat owner needs to inform us of the type of antifoul on the hull of their vessel prior to lifting. This allows us time to consider if any additional precautionary steps need to be taken.
“This may include discussing the hull profile and lifting points with the boat owner, assessing the boat manufacturer’s guidelines for lifting, and taking advice from the hull coating manufacturers.”
We called Cobb’s Quay, owned by MDL Marinas, to see if they’d lift out Maximus and they said they would. However, Joe Walton, Head of Health, Safety and Environment at MDL Marinas, points out there are many factors that need to be taken into consideration when lifting, such as the polished bottoms of race boats, boats with vinyl wraps and even the make and style of vessel.
Staying sensibly safe
“Generally, a lifting team will only know exactly what type of antifoul has been used on a vessel if the owner has informed them correctly prior to the lift, and in reality, owners themselves may not even know,” he adds.
“If the teams are concerned regarding the safety of any lift, they will cease the lift and discuss their concerns to see if another suitable solution can be offered to lift the vessel safely.”
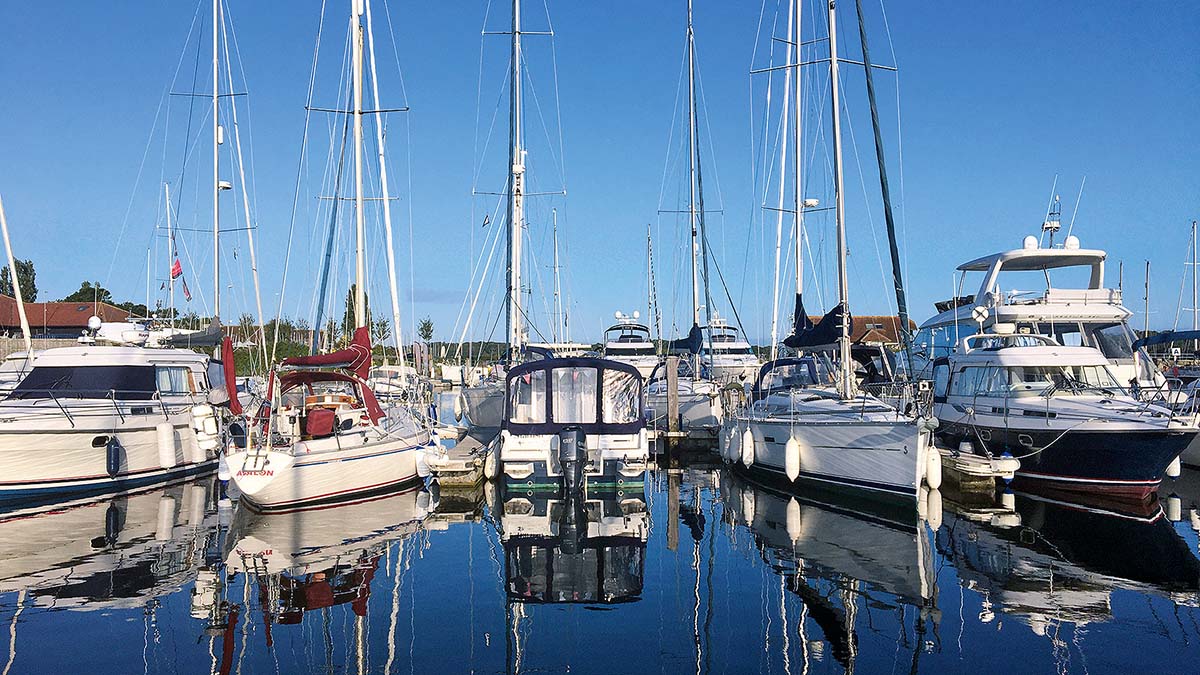
Premier Marinas, Chichester
We also called Premier Marinas in Chichester, where Maximus was berthed previously. They said a 28ft vessel with silicone antifoul would be no problem. However, they would need to take extra care to see that it was properly secured.
Nick Gill, head of boatcare at Boatfolk Marinas, said: “We do offer a lift out service for boats with Silic One or silicone antifoul. It is becoming more popular and we want to ensure we can provide a one-stop shop for all boat repair and maintenance tasks, especially if it means we can support our customers to use products that have less impact on the environment.
“When customers book in for lifting services, they will have a thorough consultation with a member of the boatcare team to confirm what has been used previously, to the best of the customer’s knowledge.
“This ensures we can follow the most appropriate procedure. As silicone antifoul is designed to be more slippery, we can take further precautions to make sure the boat is fully secure.
“For example this might include covering or tying the lifting straps together to prevent them from spreading apart, or adding another ratchet strap to reduce movement.”
Why not subscribe today?
This feature appeared in the July 2023 edition of Practical Boat Owner. For more articles like this, including DIY, money-saving advice, great boat projects, expert tips and ways to improve your boat’s performance, take out a magazine subscription to Britain’s best-selling boating magazine.
Subscribe, or make a gift for someone else, and you’ll always save at least 30% compared to newsstand prices.
See the latest PBO subscription deals on magazinesdirect.com